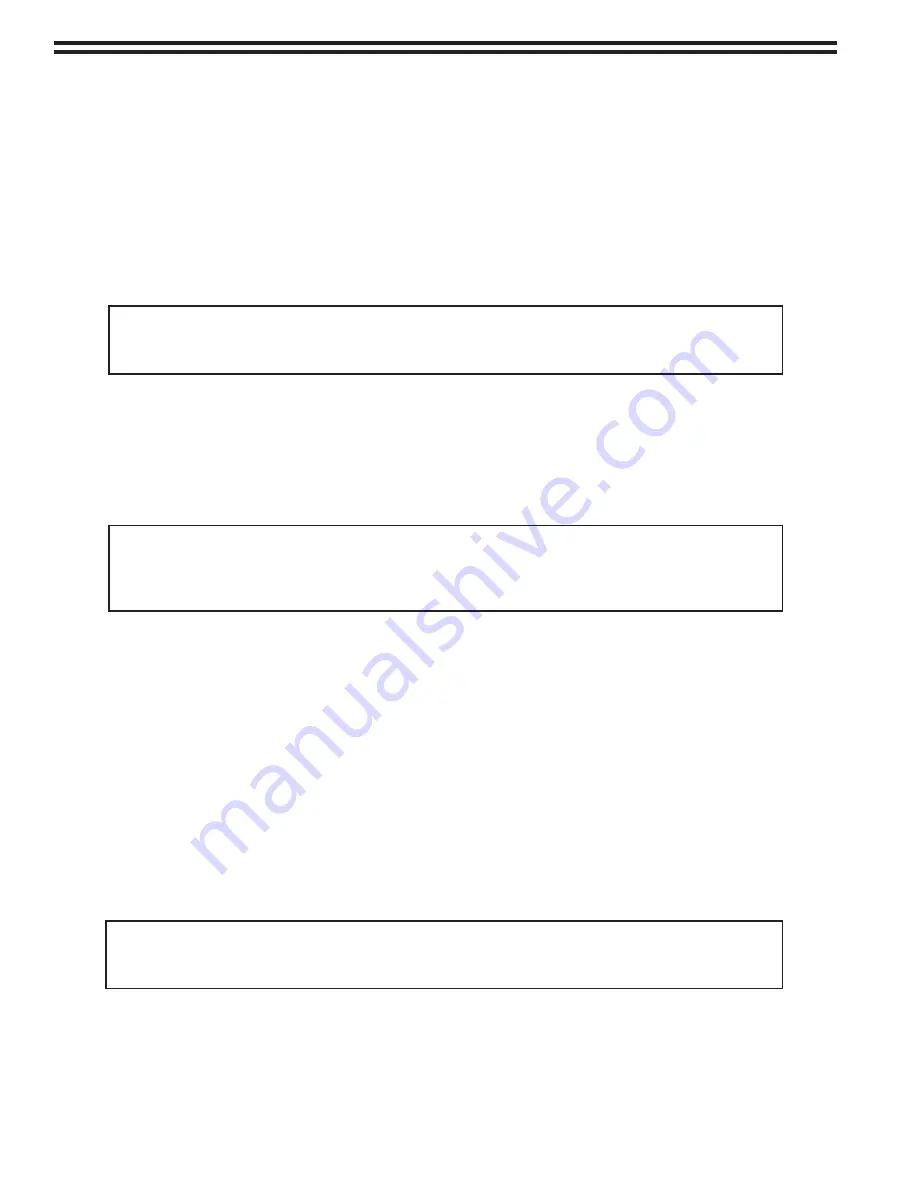
115.6031.0
- 30 -
NOTE:
Figures 12, 13 & 14 show the effect of the ambient temperature on the pressure in the gas source containers.
This relationship is shown as the solid line on the graphs. Setting the heater temperature controller during cooler
ambient temperatures will require that the controller set point be increased as the ambient temperature rises in
order to maintain the proper superheat shown on the dotted line of the graphs. Setting the controller during high
ambient temperature conditions will allow functioning during cooler conditions without having to reset the
temperature controller.
8) Finally, adjust the high and low temperature alarm settings to 15°F (8°C) above and below the final controller
temperature setting.
9) Daily, monitor operation of the Vaporizer. Confirm superheat, pressure, and cathodic protection are operating
per this instruction manual.
CAUTION
The high temperature alarm should never be set higher than 210°F for Chlorine and Ammonia.
The high temperature alarm should never be set higher than 205°F for Sulfur Dioxide.
3.8
Checking Vaporizer Performance
Vaporizer performance is based and evaluated on the number of degrees of superheat being added to the gas prior
to its discharge to the dispensing system. This is the only criterion which can be used to establish that the Vaporizer is
operating satisfactorily, i.e., within its design capabilities and at a safe level of liquid chemical in the vaporizing
chamber. The minimum superheat requirement is 20°F for Chlorine, 30°F for Sulfur Dioxide and 12 °F for Ammonia.
WARNING
It is imperative that the superheat be maintained at or above the minimum specified value for the gas
in question. A lesser value is indicative that the level of liquid chemical in the vaporizing chamber is
above a safe operating level and may permit the liquefied gas to pass through the Vaporizer.
The number of degrees of superheat is determined by observing the values of the pressure and temperature of
the gas being discharged to the using system and locating the point on the appropriate graph (Figure 12,13, or
14 whichever is applicable) which represents the relationship between these two values. The minimum superheat
requirement is met when this point falls either on or to the right of the dashed curve on the graph in question at the
maximum expected operating gas feed rate. Using Chlorine as an example (Figure 12), the gas temperature gauge
must indicate 86°F or more when the gas pressure gauge indicated 80 psig.
To increase the number of degrees of superheat, increase the setting on the water temperature controller; to de-
crease the superheat, decrease the setting. Adjustments should be made in increments of 5°F and sufficient time
(approximately 10 minutes) must be allowed for temperature equilibrium to be attained before making further
adjustments. After each change in setting, set the water low temperature alarm 15°F below (and the water high
temperature alarm 15°F above) the new temperature set point value. The water temperature control set point should
never be set higher than 205°F for Chlorine and Ammonia. The high temperature alarm should never be set higher
than 210°F for Chlorine and Ammonia. Sulfur Dioxide systems may be set for operation at 200°F maximum provided
the high temperature alarm activates no higher than 205°F. Water overflow should be minimized to avoid wasted
heat, however it must be carefully controlled to makeup for loss of water due to evaporation.
NOTE
Adjustments for superheat will have to be reset periodically to compensate for
seasonal changes in ambient temperature.
Experience will demonstrate that the minimum setting of the water temperature controller required to maintain
the minimum superheat required will increase with time. This is simply the result of the gradual fouling of the outer
and/or inner surfaces of the vaporizing chamber and the accompanying reduction in the heat transfer efficiency
through the wall of the chamber. Water quality determines the rate of fouling of the outer surface, while the quality
and quantity of the liquid chemical being handled determines the rate of fouling of the inner space. Obviously, each
incremental increase in operating temperature is accompanied by an increase in power consumption.
Summary of Contents for Capital Controls 71V3B Series
Page 1: ... 1 115 6031 0 Instruction Manual Series 71V3B Electrically Heated Vaporizer CAPITAL CONTROLS ...
Page 9: ... 9 115 6031 0 Figure 1 Sectional Diagram ...
Page 17: ... 17 115 6031 0 Figure 4 Outline Mounting Dimensions 12 kW 15 kW Heaters ...
Page 18: ...115 6031 0 18 Figure 5 Outline Mounting Dimensions 18 kW Heater ...