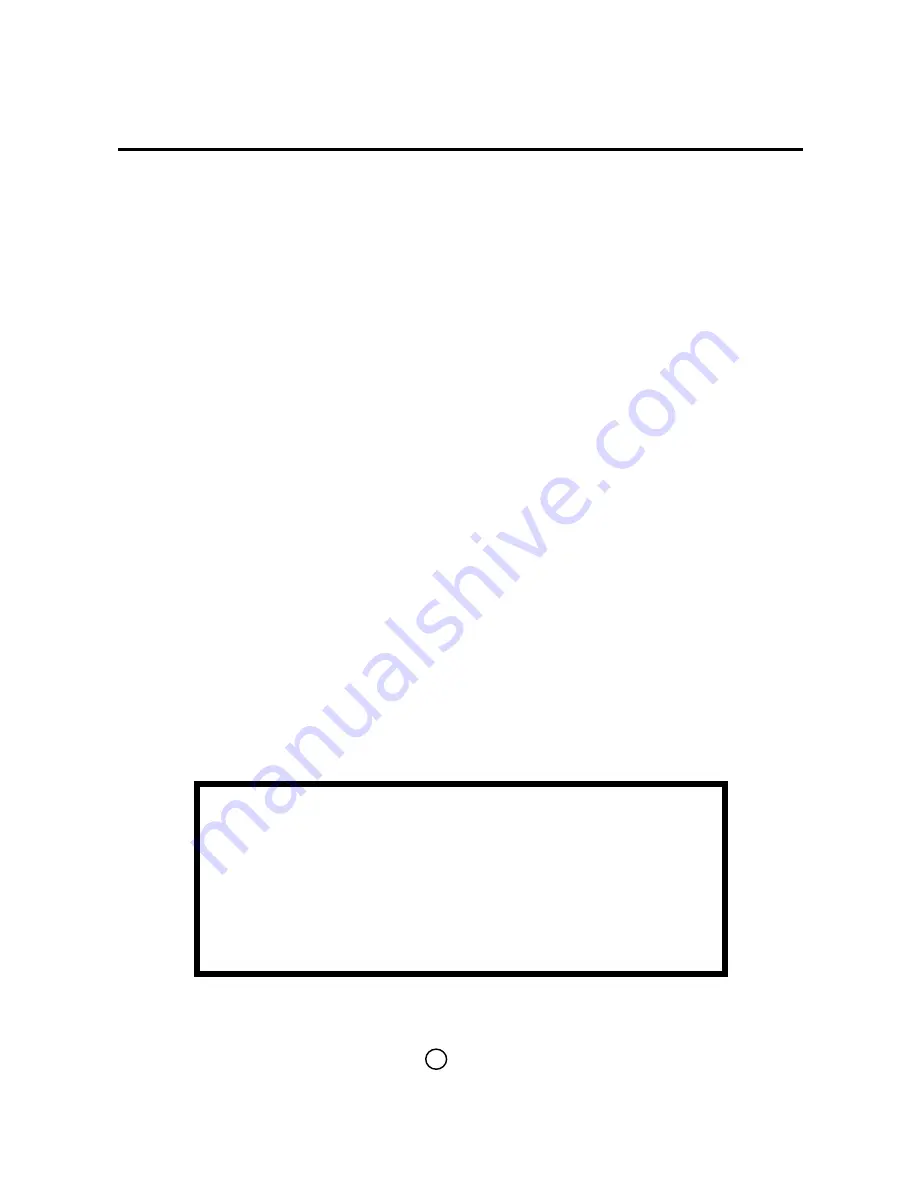
vii
SAFETY PRECAUTIONS
LASER SAFETY
The following information is provided to comply with the rules imposed by
international authorities and refers to the correct use of the DS41 scanner.
Standard Regulations
This scanner utilizes a low-power laser diode. Although staring directly at the
laser beam momentarily causes no known biological damage, avoid staring
at the beam as one would with any very strong light source, such as the sun.
Avoid that the laser beam hits the eye of an observer, even through reflective
surfaces such as mirrors, etc.
This product conforms to the applicable requirements of both IEC 825-1 and
CDRH 21 CFR 1040 at the date of manufacture. The scanner is classified as
a Class 2 laser product according to IEC 825-1 regulations and as a Class II
laser product according to CDRH regulations.
There is a safety device which allows the laser to be switched on only if the
motor is rotating above the threshold for its correct scanning speed.
The laser beam can be switched off through a software command (see also
“Beam Shutter” in the WINHOST Help On Line).
WARNING
Use of controls or adjustments or performance of
procedures other than those specified herein may
result in exposure to hazardous visible laser light.
The laser light is visible to the human eye and is emitted from the window on
the front of the scanner (Figure A,
10
).