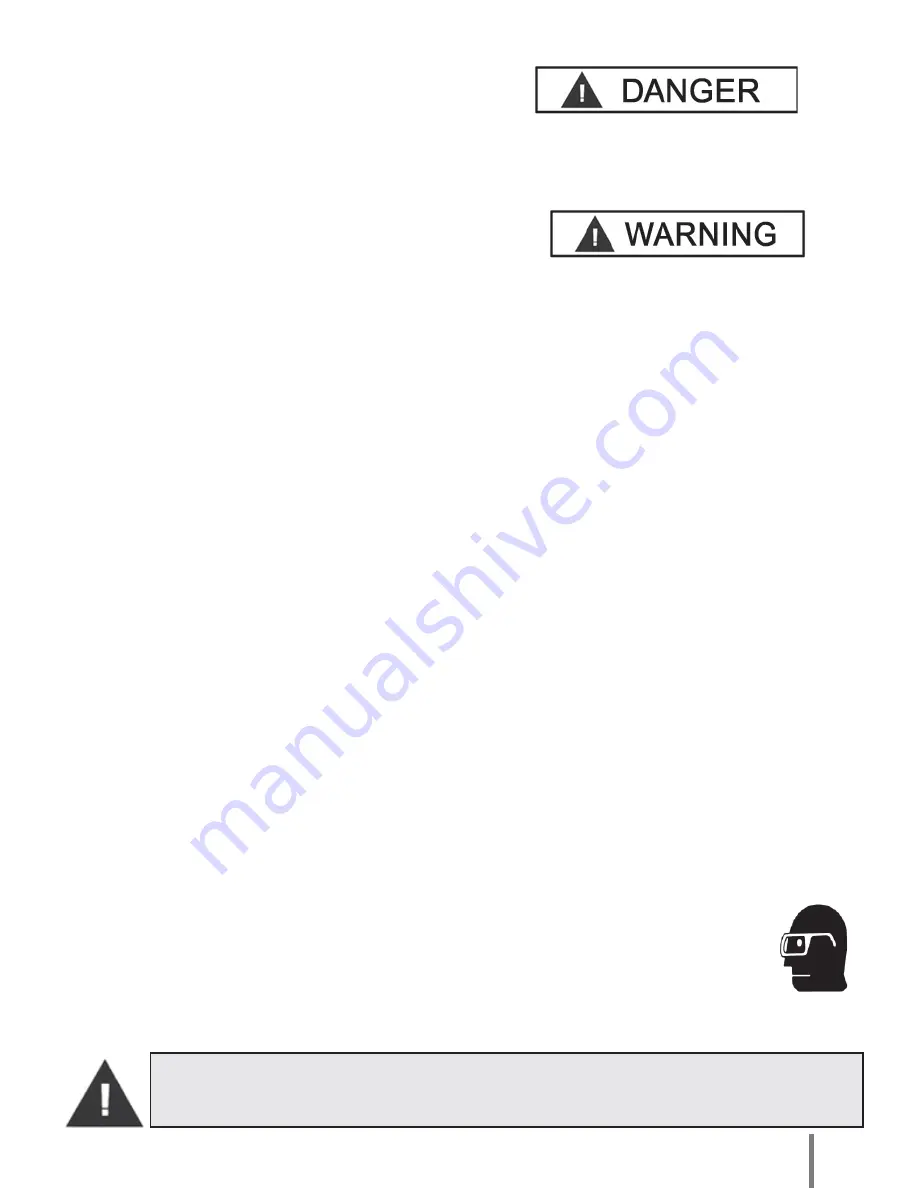
5
INSTALLER / OPERATOR
PLEASE READ AND FULLY
UNDERSTAND.
BY PROCEEDING YOU AGREE TO
THE FOLLOWING.
I have visually inspected the site where the lift is to
be installed and verified the concrete to be in good condi-
tion and free of cracks or other defects. I understand that
installing a lift on cracked or defective concrete could
cause lift failure resulting in personal injury or death.
I understand that a level floor is required for proper
installation and level lifting.
I understand that I am responsible if my floor is of
questionable slope and that I will be responsible for all
charges related to pouring a new level concrete slab if
required and any charges.
I understand that the lifts are supplied with concrete
fasteners meeting the criteria of the American National
Standard “Automotive Lifts - Safety Requirements
for Construction, Testing, and Validation” ANSI/ALI
ALCTV-1998, and that I will be responsible for all charges
related to any special regional structural and/or seismic
anchoring requirements specified by any other agencies
and/or codes such as the Uniform Building Code (UBC)
and/or International Building Code (IBC).
I will assume full responsibility for the concrete floor
and condition thereof, now or later, where the above
equipment is to be installed. Failure to follow danger,
warning, and caution instructions may lead to serious per-
sonal injury or death to operator or bystander or damage
to property.
I understand that Dannmar/ MaxJax lifts are designed
to be installed in indoor locations only. Failure to follow
installation instructions may lead to serious personal
injury or death to operator or bystander or damage
to
property or lift.
Failure to follow danger, warning, and caution
instructions may lead to serious personal injury or death
to operator or bystander or damage to property.
Please read entire manual prior to installation.
Do not operate this machine until you read and
understand all the dangers, warnings and cautions
in this manual. For additional copies
or further information, contact:
Dannmar Equipment
646 Flinn Ave. Suite A
Moorpark, CA. 93021
Tel: 1-877-432-6627
Fax: 1-805-530-1909
INSTALLER / OPERATOR
PROTECTIVE EQUIPMENT
Personal protective equipment helps makes installation
and operation safer, however, it does not take the place
of safe operating practices. Always wear durable work
clothing during any installation and/or service activity.
Shop aprons or shop coats may also be worn, however
loose fitting clothing should be avoided. Tight fitting
leather gloves are recommended to protect technician
hands when handling parts. Sturdy leather work shoes
with steel toes and oil resistant soles should be used by
all service personnel to help prevent injury during typical
installation and operation activities.
Eye protection is essential during installation and
operation activities. Safety glasses with side shields,
goggles, or face shields are acceptable.
Back belts provide support during lifting
activities and are also helpful in providing
worker protection. Consideration should
also be given to the use of hearing protec-
tion if service activity is performed in an
enclosed area, or if noise levels are high.
THIS SYMBOL POINTS OUT IMPORTANT SAFETY INSTRUCTIONS WHICH IF NOT FOLLOWED
COULD ENDANGER THE PERSONAL SAFETY AND/OR PROPERTY OR YOURSELF AND OTHERS
AND CAN CAUSE PERSONAL INJURY OR DEATH. READ AND FOLLOW ALL INSTRUCTIONS IN
THIS MANUAL BEFORE ATTEMPTING TO OPERATE THIS MACHINE.