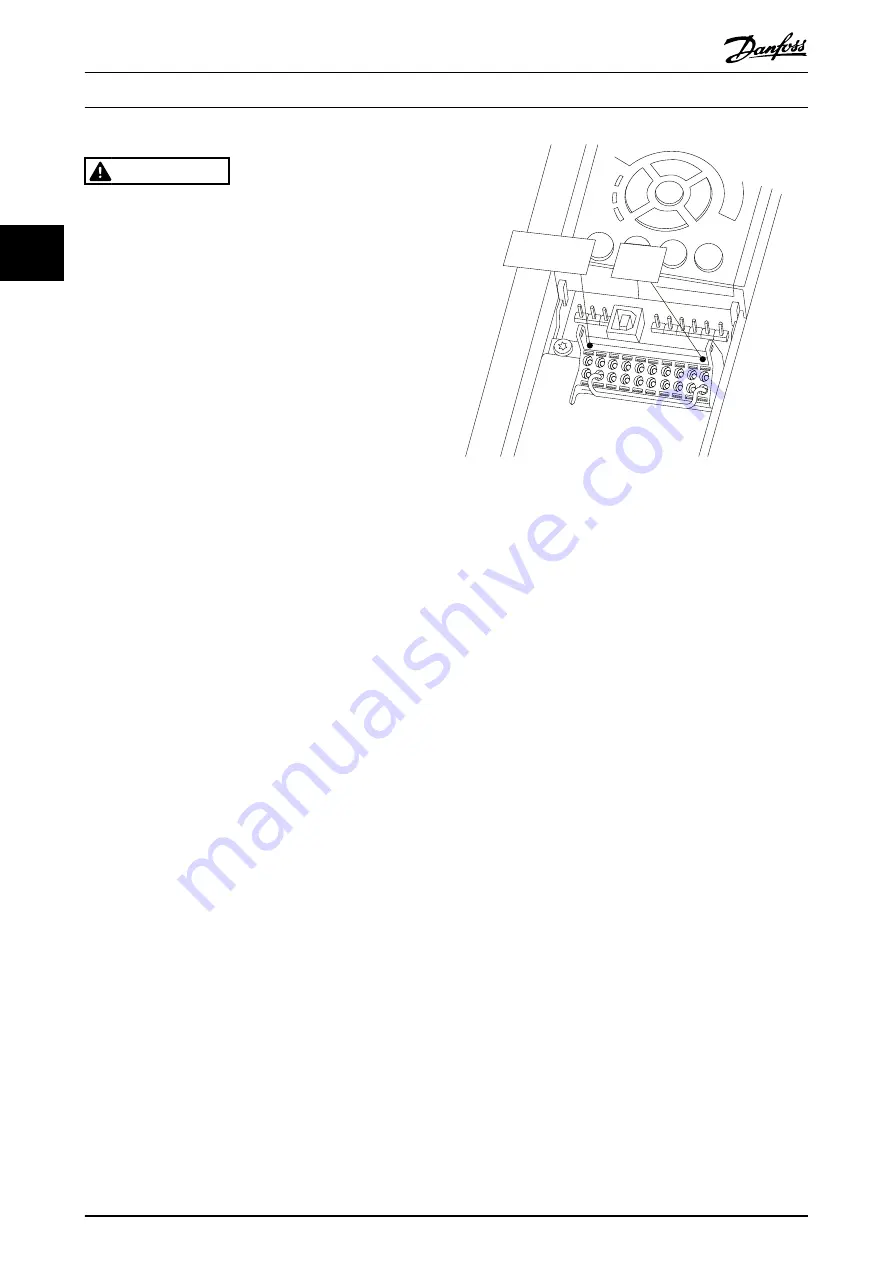
Safe Stop Installation and Set-Up
WARNING
SAFE STOP FUNCTION!
The safe stop function does NOT isolate mains voltage to
the frequency converter or auxiliary circuits. Perform work
on electrical parts of the frequency converter or the motor
only after isolating the mains voltage supply and waiting
the length of time specified under Safety in this manual.
Failure to isolate the mains voltage supply from the unit
and waiting the time specified could result in death or
serious injury.
•
It is not recommended to stop the frequency
converter by using the Safe Torque Off function.
If a running frequency converter is stopped by
using the function, the unit will trip and stop by
coasting. If this is not acceptable, e.g. causes
danger, the frequency converter and machinery
must be stopped using the appropriate stopping
mode before using this function. Depending on
the application a mechanical brake may be
required.
•
Concerning synchronous and permanent magnet
motor frequency converters in case of a multiple
IGBT power semiconductor failure: In spite of the
activation of the Safe torque off function, the
frequency converter system can produce an
alignment torque which maximally rotates the
motor shaft by 180/p degrees. p denotes the pole
pair number.
•
This function is suitable for performing
mechanical work on the frequency converter
system or affected area of a machine only. It does
not provide electrical safety. This function should
not be used as a control for starting and/or
stopping the frequency converter.
The following requirements have to be meet to perform a
safe installation of the frequency converter:
1.
Remove the jumper wire between control
terminals 37 and 12 or 13. Cutting or breaking
the jumper is not sufficient to avoid short-
circuiting. (See jumper on
.)
2.
Connect an external Safety monitoring relay via a
NO safety function (the instruction for the safety
device must be followed) to terminal 37 (safe
stop) and either terminal 12 or 13 (24V DC). The
Safety monitoring relay must comply with
Category 3 (EN 954-1) / PL “d” (ISO 13849-1).
12/13
37
130BA874.10
Illustration 2.22 Jumper between Terminal 12/13 (24V) and 37
Installation
VLT
®
AQUA Drive
Operating Instructions
20
MG.20.M8.02 - VLT
®
is a registered Danfoss trademark
2
2