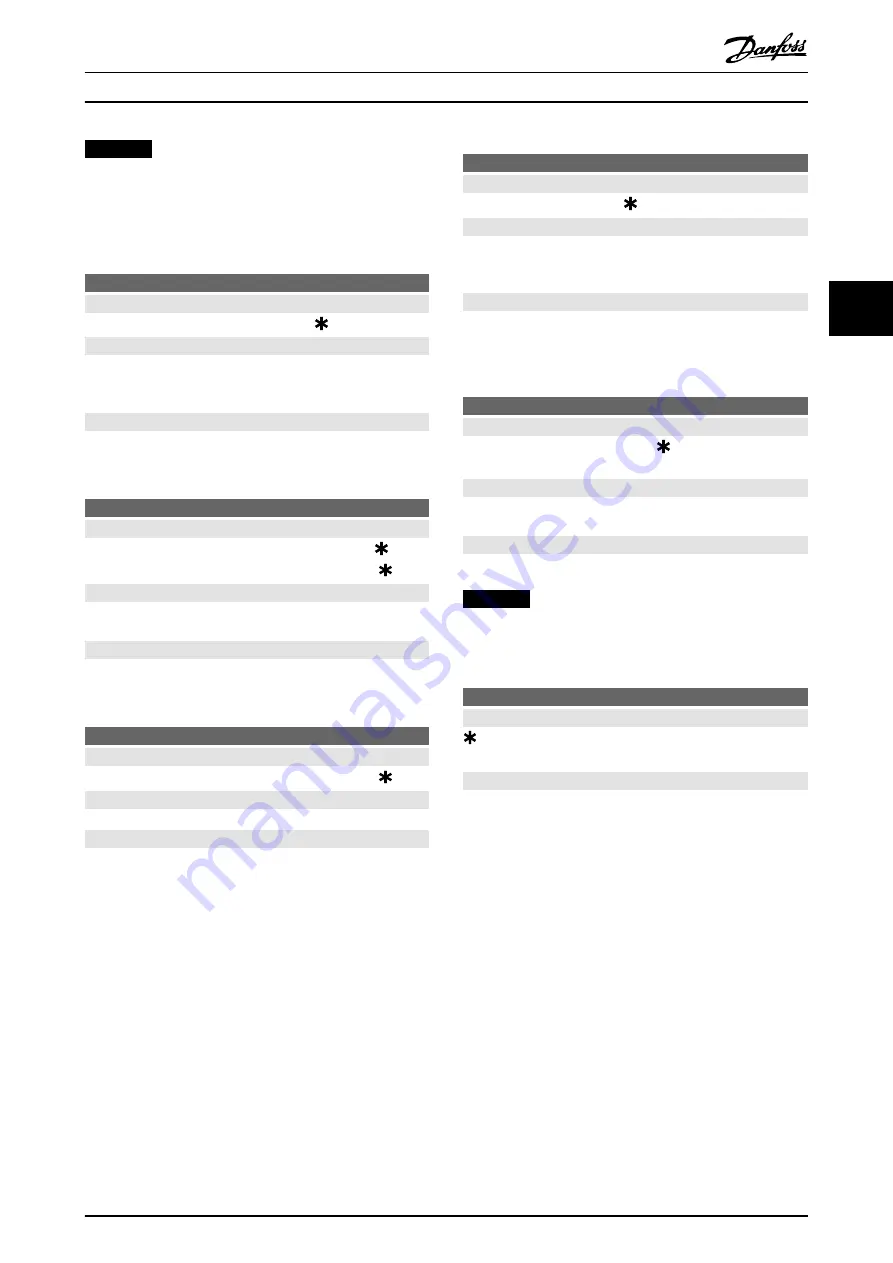
NOTICE
Note that if a value set in the nameplate parameters
102-106 is changed, there is an automatic change of
parameter 108 Stator resistance
and
parameter 109 Stator
reactance
.
102
Motor power P
M,N
Value:
0.25 - 22 kW
Depends on unit
Function:
Set a power value [kW] P
M,N
, corresponding to the motor's
rated power. The factory sets a rated power value [kW] P
M,N
, that depends on the type of unit.
Description of choice:
Set a value that matches the nameplate data on the
motor. Settings between one size below and one size over
the factory setting are possible.
103
Motor voltage U
M,N
Value:
For 200 V units: 50 - 999 V
230 V
For 400 V units: 50 - 999 V
400 V
Function:
Set the rated motor voltage U
M,N
for either star Y or delta
Δ.
Description of choice:
Select a value that corresponds to the nameplate data on
the motor, regardless of the frequency converter's mains
voltage.
104
Motor frequency f
M,N
Value:
24-1000 Hz
50 Hz
Function:
Select the rated motor frequency f
M,N
.
Description of choice:
Select a value that corresponds to the nameplate data on
the motor.
105
Motor current I
M,N
Value:
0,01 - I
MAX
Depends on choice of motor
Function:
The nominal, rated current of the motor I
M,N
forms part of
the frequency converter calculation of features such as
torque and motor thermal protection.
Description of choice:
Set a value that corresponds to the nameplate data on the
motor. Set the motor current I
M,N
taking into account
whether the motor is star-connected Y or delta-connected
Δ.
106
Rated motor speed
Value:
100 - f
M,N
x 60 (max.
60000 rpm)
Depends on parameter
104
Motor frequency, f
M,N
Function:
Set the value that corresponds to the rated motor speed
n
M,N
that can be seen from the nameplate data.
Description of choice:
Select a value that corresponds to the nameplate data on
the motor.
NOTICE
The maximum value equals f
M,N
x 60. f
M,N
to be set in
parameter 104 Motor frequency, f
M,N
.
107
Automatic motor tuning, AMT
Value:
Optimisation off (AMT off)
[0]
Optimisation on (AMT start)
[2]
Function:
Automatic motor tuning is an algorithm that measures
stator resistance R
S
without the motor axle turning. This
means that the motor is not delivering any torque.
AMT can be used for optimising adjustment of the
frequency converter to the motor being used. This is used
in particular when the factory setting does not sufficiently
cover the motor.
For the best possible tuning of the frequency converter, it
is recommended that AMT is performed on a cold motor.
Note that repeated AMT runs can cause heating of the
motor, resulting in an increase in the stator resistance R
S
.
As a rule, however, this is not critical.
AMT is performed as follows:
Start AMT:
1.
Give a STOP signal.
2.
Parameter 107 Automatic motor tuning
is set at
value
[2] Optimisation on
.
3.
A START signal is given and
parameter 107
Automatic motor tuning
is reset to
[0] Optimisation
off
when AMT has been completed.
Programming
Design Guide
MG27E402
Danfoss A/S © Rev. May/2014 All rights reserved.
69
4
4