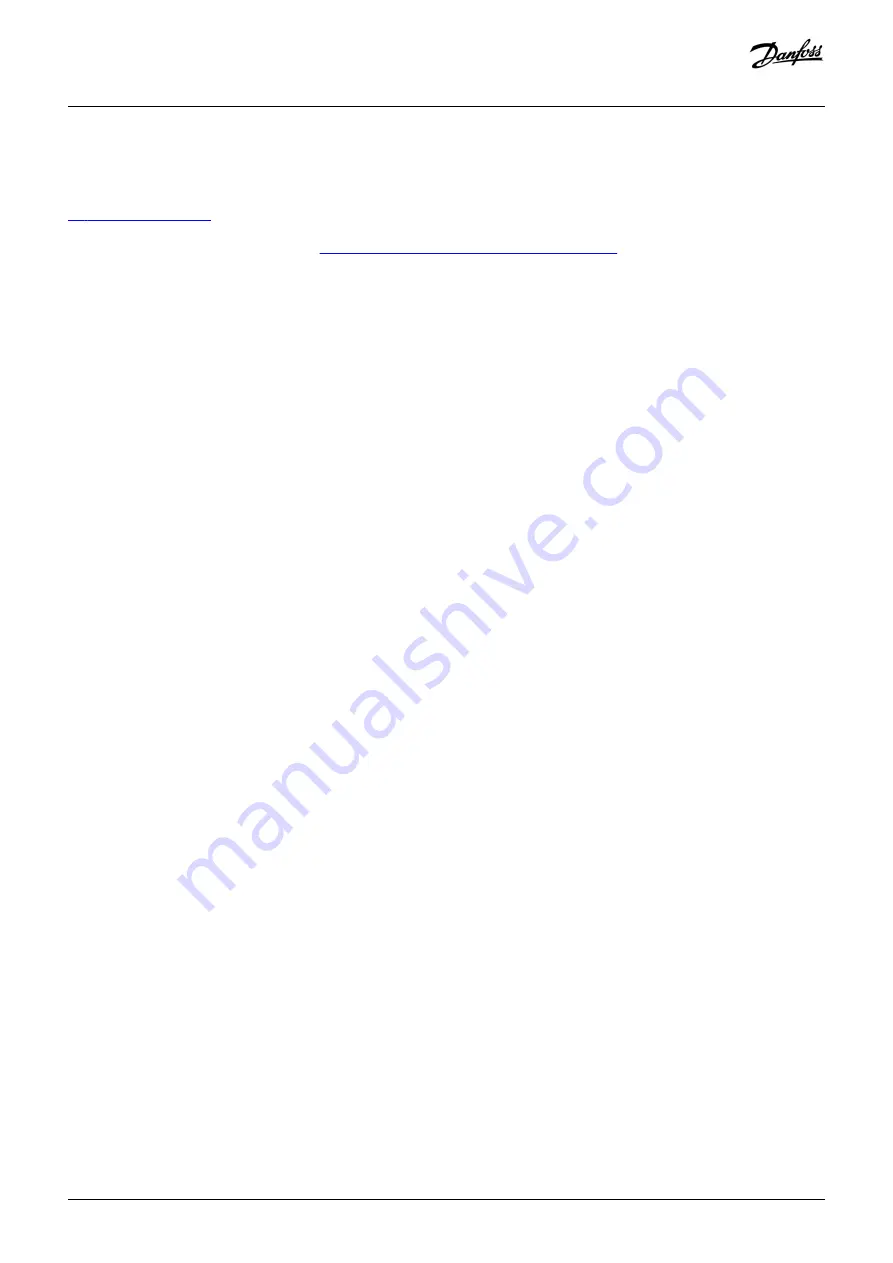
Prerequisites:
Make sure that the delivery contains all necessary components. For the installation, the contents of the accessories bag is needed, see
Open the covers according to instructions in
6.4.4 Get Access and Locate the Terminals for FR8/FI8
.
Electrical Installation
Operating Guide | VACON® NX Inverters FI4-FI8
AQ299433367205en-000101 / DPD00908
56 | Danfoss A/S © 2019.07
Summary of Contents for VACON NX FI4
Page 1: ...Operating Guide VACON NX Inverters FI4 FI8...
Page 2: ......