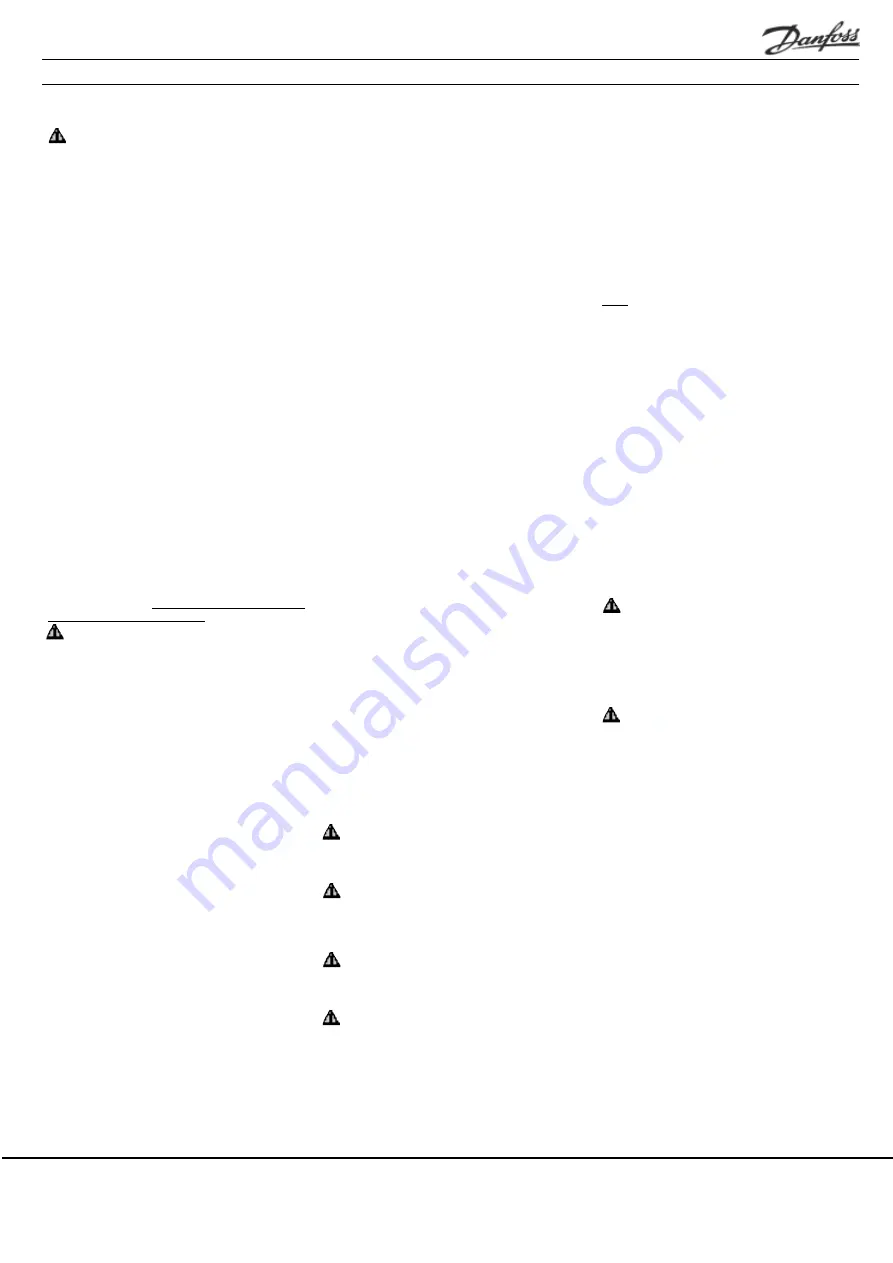
refrigerant flow and pressure drops (sol
enoid valve, filter dryer, expansion valve, etc.),
refrigerant charge.
·
Low refrigerant charge : The correct refriger-
ant charge is given by the liquid sight glass indica-
tion, the condenser delta T in relation to the refrig-
erant pressure tables (pressure-temperature), the su-
perheat and the sub-cooling, etc. ((if additional
charge is deemed necessary, refer to the “Filling
the system” section).
·
Compressor short cycling : The number of
cycles shall never exceed 12 starts per hour.
12 - Maintenance
·
Performer
®
compressors do not necessitate
any special maintenance procedure. However, it
must be recalled that proper operations and main-
tenance of the system serve to prevent against
system-related compressor problems. The follow-
ing preventive maintenance checks, to be per-
for med at regular intervals, are highly
recommended:
o Control operating conditions (evaporating
temperature, condensing temperature, com-
pressor discharge temperature, temperature
difference on heat exchangers, superheat,
sub-cooling). These conditions must always
remain within compressor operation limits.
o Verify that safety devices are operational
and properly set.
o Check the compressor oil level and
quality; this step may include an acid test,
humidity check, spectrometer analysis, etc.
whenever the oil becomes discolored.
o Ensure that the circuit is leak tight.
o Verify the proper operation of heat exchangers
and, if necessary, clean them.
o Check the current draw on the
compressor motor as well as proper voltage
balance between phases.
o Check that all electrical connections are
still adequately fastened.
o Make sure the compressor is clean and in
good working order; verify the absence of rust
on the compressor shell, piping and electrical
connections.
o Make sure the refrigerant charge is suitable
for both winter and summer operation.
·
Ensure that periodic in-service inspections
required by local regulations are performed.
13 – Replacement
Precaution must be taken when disconnecting,
cutting or drilling holes in the tubing to ensure that
no refrigerant under pressure is present in the
system.
The refrigerant shall not be discharged
directly into the atmosphere; rather, it must be
removed using approved reclamation techniques
and equipment and then safely stored, in accordance
with applicable legislation.
The presence of refrigerant vapor can dis-
place air and lead to suffocation. Proper ventila-
tion is mandatory at all times when servicing the
equipment.
A refrigeration system component change
must be carried out in compliance with local
regulations.
·
Make sure that the main power supply has been
switched off.
·
Before replacement, it is necessar y to
determine the cause of failure and implement
remedial action. If such analysis and repair are
not performed, repetitive failure may occur.
Note that an oil acidity test always proves helpful in
8510197P01-D © Danfoss Maneurop
06-2002
5
Instructions
diagnosis when undertaking compressor replacement.
·
Check that the new Performer
®
compressor
and the on-site compressor to be replaced dis-
play the same electrical and refrigeration perfor-
mance characteristics.
·
Use the rubber grommets and gaskets sup-
plied with the new compressor.
·
Whenever piping needs to be modified, please
refer to the “Safety measures prior to assembly”
section.
·
For further details on replacement steps, refer
to the previous sections of this manual.
Note: In the event of motor failure, flush and clean
the entire circuit before replacing the compressor
in order to remove acids and contaminants.
Systematically install a new filter dryer on the
liquid line. Prior to this step (if necessary), run the
system for at least 2 hours with anti-acid
cartridges (in such instances, the installation of a
suction filter might also be required). After an
operating period of approximately 2 weeks, check
the level of oil acidity. If the oil acid test proves
positive, drain and replace the oil, replace the
anti-acid liquid line filter dryer cartridges and the
suction filter previously installed. Repeat oil and
filter dryer replacements until the system is clean
and acid-free. When there is no longer any sign of
acidity, replace the anti-acid cartridges by the stan-
dard model and remove the suction strainer car-
tridge as required.
14 - User advisory
I
nsist that all service operations only be
performed by qualified personnel.
The compressor and tubing surface tempera-
tures may exceed 100
°
C (212
°
F) and cause se-
vere bodily burns. Special precaution must be
taken when working around the compressor and
refrigerant tubing. Moreover, a compressor in
operation can generate very cold surface tempera-
tures (as low as -25
°
C / -13
°
F), thereby exposing
personnel to the risk of freezing burns.
Pressure inside the compressor can reach
dangerously high levels (e.g. abnormal operation,
fire,…) leading to personnel injury if suddenly
released; therefore, never drill, weld or cut the com-
pressor shell and adjacent tubing (release of liq-
uid refr igerant can cause flash freezing on
exposed skin).
Be aware that the product warranty may be
deemed null and void in the following cases:
·
external modifications to the compressor
(absence of nameplate, drilling, welding, broken
feet, shock marks),
·
compressor opened by the user or returned
unsealed (i.e. open discharge or suction ports),
·
presence of rust or water inside the compres-
sor
·
addition of leak-detection fluid in the lubricant
·
use of a refrigerant or lubricant not approved
by Danfoss Maneurop S.A.,
·
any deviation from recommended instructions
pertaining to installation, application or maintenance,
·
use in mobile applications (boats, trains, trucks,
etc.) or under explosive atmospheric conditions
(the compressor connecting box is not
explosion-proof).
The date of production of the compressor is
indicated on the nameplate. Ensure that
the model and serial number information is
always transmitted with any claim filed regarding
this product.
10 - Start up
Never start the compressor in the absence
of a refrigerant charge.
·
Do not bypass the LP or any other safety
switches during start-up.
·
Check current draw and voltage levels.
·
Monitor the oil sight glass (when mounted) for
60 min. to ensure proper oil return to the compressor.
·
Suction superheat setting: Optimal compres-
sor suction superheat would be around 10K, with
the maximum allowable superheat being 30K.
·
In all cases, the application limits of the
compressor must be respected; moreover, high
superheat values lead to high discharge
temperatures and decrease compressor capacity.
The maximum discharge temperature is 130
°
C :
operating at a higher temperature may result in
refrigerant decomposition.
·
Under steady-state operating conditions, check
refrigerant piping or capillary tubes for abnormal
vibrations (refrigeration line movement in excess
of 1.5 mm necessitates corrective actions, pipe
brackets, etc.).
·
After 2 to 4 hours of operations under
established conditions, check the oil level and
add oil if necessary (refer to TI bulletin 1-025).
If oil return continues to perform poorly, fur ther
investigation of the piping design is required.
·
Ensure that refrigerant flow through the liquid
line sight glass (when mounted) is adequate and
that operating temperatures correspond with
system specifications.
·
When needed, refrigerant may be added in the
liquid phase, carefully throttling the refrigerant on
the low-pressure side and as far as possible from
the compressor. The compressor must be
operating during this process.
Do not overcharge the system
.
11 – Troubleshooting
·
Compressor failure to start: Verify that the
compressor is hooked up to the power supply;
check the power lead connections. If these
verifications reveal no abnormality, control the
motor windings with an ohmmeter.
Note: When the internal motor protector has
tripped out (SM/SZ 084 -090- 100 - 110 - 120 -
161), it may take up to several hours to reset and
restart the compressor.
·
Compressor failure to build up pressure:
Check to make sure that all bypass valves in the
system have not been open. Also check that all
solenoid valves are in their proper position.
For S240 and S300 models, if the internal
pressure relief valve is opened, the compressor
sump will be warm and the compressor will trip
out on the motor protector. If this happens, it may
take up to 2 or 3 hours to reset.
·
Abnormal running noise: Ensure the absence
of any liquid flood-back to the compressor by
means of measuring the return gas superheat and
compressor
sump temperature. The sump should
be at least 10K above the saturated suction
temperature under steady-state operating conditions.
·
The high-pressure switch trips out: Check
condenser operations (condenser cleanliness, fan
operations, water flow and water pressure valve,
water filter, etc.). If above check out OK, the prob-
lem may be due to either refr igerant over
charging or the presence of a non-condensable
(e.g. air) in the circuit.
·
The low-pressure switch trips out: Check
evaporator operations (coil cleanliness,fan
operations, water flow, water filter, etc.), liquid