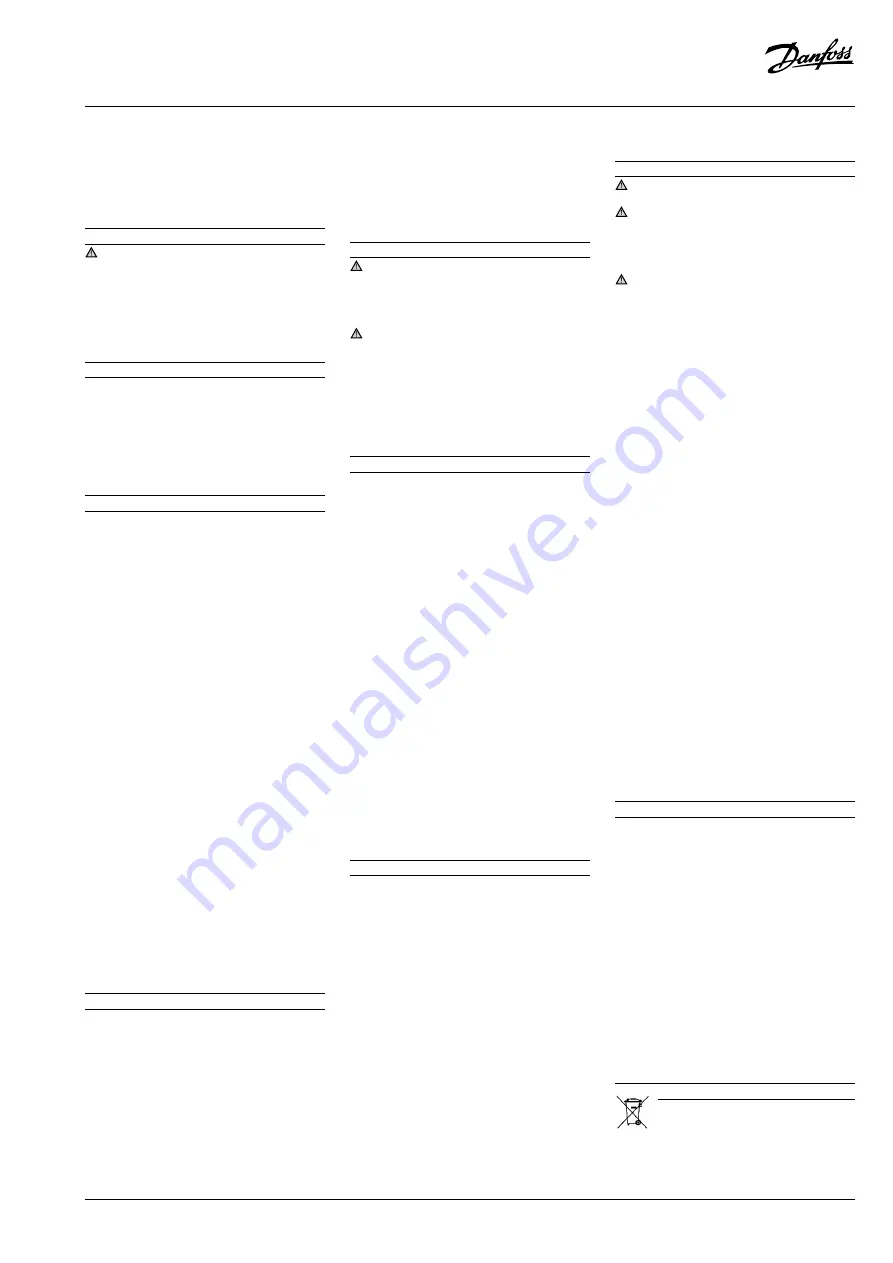
• Braze with great care using state-of-the-art tech-
nique and vent piping with nitrogen gas flow.
• Connect the required safety and control de-
vices. When the schrader port is used for this,
remove the internal valve.
• It is recommended to insulate the suction pipe
up to the compressor inlet with 19 mm thick
insulation.
5 – Leak detection
Never pressurize the circuit with oxygen or
dry air. This could cause fire or explosion.
• Do not use dye for leak detection.
• Perform a leak detection test on the complete
system.
• The maximum test pressure is 32 bar.
• When a leak is discovered, repair the leak and
repeat the leak detection.
6 – Vacuum dehydration
• Never use the compressor to evacuate the system.
• Connect a vacuum pump to both the LP & HP
sides.
• Pull down the system under a vacuum of 500
μm Hg (0.67 mbar) absolute.
• Do not use a megohmmeter nor apply power
to the compressor while it is under vacuum as
this may cause internal damage.
7 – Electrical connections
• Switch off and isolate the main power supply.
• Ensure that power supply can not be switched
on during installation.
• All electrical components must be selected as
per local standards and unit requirements.
• Refer to wiring diagram for electrical connec-
tions details.
• Ensure that the power supply corresponds
to the unit characteristics and that the power
supply is stable (nominal voltage ±10% and
nominal frequency ±2,5 Hz).
• Dimension the power supply cables according
to unit data for voltage and current.
• Protect the power supply and ensure correct
earthing.
• Make the power supply according to local stan-
dards and legal requirements.
• The unit is equipped with high and low pressure
switches, which directly cut the power supply to
the compressor in case of activation. Parameters
for high and low pressure cut outs should be
set by installer considering compressor model,
refrigerant and application. Units with Danfoss
MLZ and LLZ compressors are also equipped
with phase sequence relay to protect the unit
against phase loss/sequence/ asymmetry and
under-/over-voltage.
For units with a 3-phase scroll compressor, cor-
rect phase sequence for compressor rotation
direction shall be observed.
• Determine the phase sequence by using a
phase meter in order to establish the phase
orders of line phases L1, L2 and L3.
• Connect line phases L1, L2 and L3 to main swit-
ch terminals T1, T2 and T3 respectively.
8 – Filling the system
• Wear protective stuff like goggles and protec-
tive gloves.
• Never start the compressor under vacuum.
Keep the compressor switched off.
• Before charging the refrigerant, verify that the
oil level is between ¼ and ¾ on the compressor
oil sight glass. If additional oil is required please
refer to the compressors label for type of oil.
• Use only the refrigerant for which the unit is
designed for.
• Fill the refrigerant in liquid phase into the
condenser or liquid receiver. Ensure a slow
charging of the system to 4 – 5 bar for R404A /
R507A or R22 and approx. 2 bar for R134a.
• Do not put liquid refrigerant through suction line.
• It is not allowed to mix additives with the oil
and/or refrigerant
• The remaining charge is done until the instal-
lation has reached a level of stable nominal
condition during operation.
• Never leave the filling cylinder connected to
the circuit.
9 – Verification before commissioning
Use safety devices such as safety pressure
switch and mechanical relief valve in compliance
with both generally and locally applicable regu-
lations and safety standards. Ensure that they
are operational and properly set.
Check that the settings of high-pressure swit-
ches and relief valves don’t exceed the maximum
service pressure of any system component.
• Verify that all electrical connections are properly
fastened and in compliance with local regulations.
• When a crankcase heater is required, it must be
energized at least 12 hours before initial start-
up and start-up after prolonged shut-down
period.
10 – Start-up
• Never start the unit when no refrigerant is char-
ged.
• All service valves must be in the open position.
See picture 3.
• Check compliance between unit and power
supply.
• Check that the crankcase heater is working.
• Check that the fan can rotate freely.
• Check that the protection sheet has been re-
moved from the backside of condenser.
• Balance the HP/LP pressure.
• Energize the unit. It must start promptly. If
the compressor does not start, check wiring
conformity, voltage on terminals and sequence
phase.
• Eventual reverse rotation of a 3-phase com-
pressor can be detected by following phe-
nomena; unit doesn’t start, the compressor
doesn’t build up pressure, it has abnormally
high sound level and abnormally low power
consumption. In such case, shut down the unit
immediately and connect the phases to their
proper terminals.
• If the rotation direction is correct the low pres-
sure indication on the low pressure gauge shall
show a declining pressure and the high pres-
sure indication on the high pressure gauge
shall show an increasing pressure.
11 – Check with running unit
• Check the fan rotation direction. Air must flow
from the condenser towards the fan.
• Check current draw and voltage.
• Check suction superheat to reduce risk of slug-
ging.
• When a sight glass is provided observe the oil
level at start and during operation to confirm
that the oil level remains visible.
• Respect the operating limits.
• Check all tubes for abnormal vibration. Move-
ments in excess of 1.5 mm require corrective
measures such as tube brackets.
• When needed, additional refrigerant in liquid
phase may be added in the low-pressure side as
far away as possible from the compressor. The
compressor must be operating during this pro-
cess.
• Do not overcharge the system.
• Never release refrigerant to atmosphere.
• Before leaving the installation site, carry out
a general installation inspection regarding
cleanliness, noise and leak detection.
• Record type and amount of refrigerant charge
as well as operating conditions as a reference
for future inspections.
12 – Maintenance
Always switch off the unit at main switch
before remove fan panel.
Internal pressure and surface temperature
are dangerous and may cause permanent injury.
Maintenance operators and installers require
appropriate skills and tools. Tubing temperature
may exceed 100°C and can cause severe burns.
Ensure that periodic service inspections to
ensure system reliability and as required by local
regulations are performed.
To prevent system related problems, following
Periodic maintenance is recommended:
• Verify that safety devices are operational and
properly set.
• Ensure that the system is leak tight.
• Check the compressor current draw.
• Confirm that the system is operating in a way
consistent with previous maintenance records
and ambient conditions.
• Check that all electrical connections are still
adequately fastened.
• Keep the unit clean and verify the absence of
rust and oxidation on the unit components,
tubes and electrical connections.
The condenser must be checked at least once
a year for clogging and be cleaned if deemed
necessary. Access to the internal side of the
condenser takes place through the fan panel.
Microchannel coils tend to accumulate dirt on
the surface rather than inside, which makes
them easier to clean than fin-&-tube coils.
• Switch off the unit at main switch before re-
move any panel from the condensing unit.
• Remove surface dirt, leaves, fibres, etc. with
a vacuum cleaner, equipped with a brush or
other soft attachment. Alternatively, blow com-
pressed air through the coil from the inside out,
and brush with a soft bristle. Do not use a wire
brush. Do not impact or scrape the coil with the
vacuum tube or air nozzle.
If the refrigerant system has been opened, the
system has to be flushed with dry air or nitrogen
to remove moisture and a new filter drier has to
be installed. If evacuation of refrigerant has to be
done, it shall be done in such a way that no refri-
gerant can escape to the environment.
13 - Warranty
Always transmit the model number and serial num-
ber with any claim filed regarding this product.
The product warranty may be void in following
cases:
• Absence of nameplate.
• External modifications; in particular, drilling,
welding, broken feet and shock marks.
• Compressor opened or returned unsealed.
• Rust, water or leak detection dye inside the
compressor.
• Use of a refrigerant or lubricant not approved
by Danfoss.
• Any deviation from recommended instructions
pertaining to installation, application or main-
tenance.
• Use in mobile applications.
• Use in explosive atmospheric environment.
• No model number or serial number transmit-
ted with the warranty claim.
14 – Disposal
Danfoss recommends that condensing
units and oil should be recycled by a
suitable company at its site.
Instructions
© Danfoss | DCS (CC) | 2017.02 | 5
FRCC.PI.051.A1.03