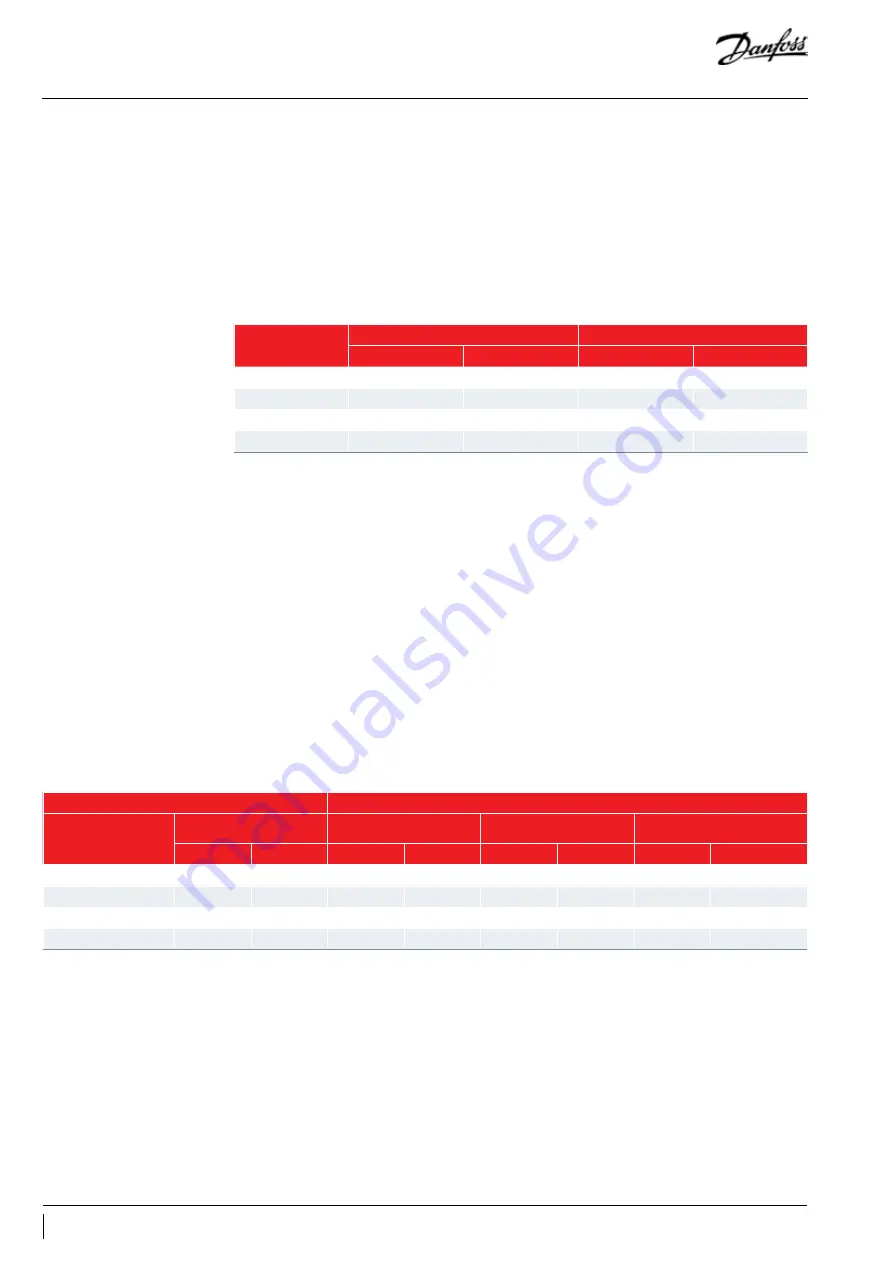
Battery protection system
There is a protection system for the battery that
prevents the compressor from operating if the
available voltage becomes too low. The battery
protection level should be set up as following:
• By programming:
Voltage limits for battery protection can be freely
set, by the customer for every system (12-14V,
24-28V, 36-42V or special) by means of the serial
port of a PC connected to the SPI port of the
electronic driver using the FxC programming
package provided by the manufacturer upon
request. In that option cut-out and cut-in values
must respect the rule defined by Table 2.
In Table 2, ΔV is the difference between cut-out
and cut-in, that is, the cut-in value is the result of
adding ΔV to the cut-out value.
Table 2. Limits of battery
protection parameters
Table 3. IN1, IN2 and COM
connection for battery
protection set up 0=open
connection; 1=shortened
Rated voltage
range (V)
Cut-out (V)
ΔV
min
max
min
max
12-14
9,0
12,0
1,0
1.5
24-28
20,0
26,0
2,0
3,0
36-42
34,0
40,0
2,0
3,0
Special
9,0
40,0
1,0
3,0
• Externally, using COM, IN1 and IN2 of SPI:
· This option prevents from the possibility of
setting up the speed externally using COM, IN1
and IN2 of SPI as defined in point 6.
· The external battery protection set up option
must be previously programmed for external
adjustment of the protection limits.
· Voltage limits are set up by means of a PC
through its serial port connected to the
electronic driver SPI. It can be done by the
customer itself using the FxC programming
package.
· The cut-out (battery voltage at which the
driver stops operating) and the cut-in (battery
voltage at which driver re-starts operation
after a cut-off) values are set up by connecting
the SPI connector terminals IN1 and IN2 to
COM. according to the connection made, four
protection levels can be selected as shown in
Table 3.
Protection limits (V)
Rated operating voltage range
Protection
level
Connection to COM
12-14 V
24-28 V
36-42 V
IN1
IN2
cut-out
cut-in
cut-out
cut-in
cut-out
cut-in
Standard
0
0
10,0
11,5
22,0
24,5
36,0
38,5
Low
1
0
9,0
10,5
20,0
22,5
34,0
36,5
High
0
1
11,0
12,5
24,0
26,5
38,0
40,5
Very high
1
1
12,0
13,5
26,0
28,5
40,0
42,5
10
FRCC.PC.041.A1.02