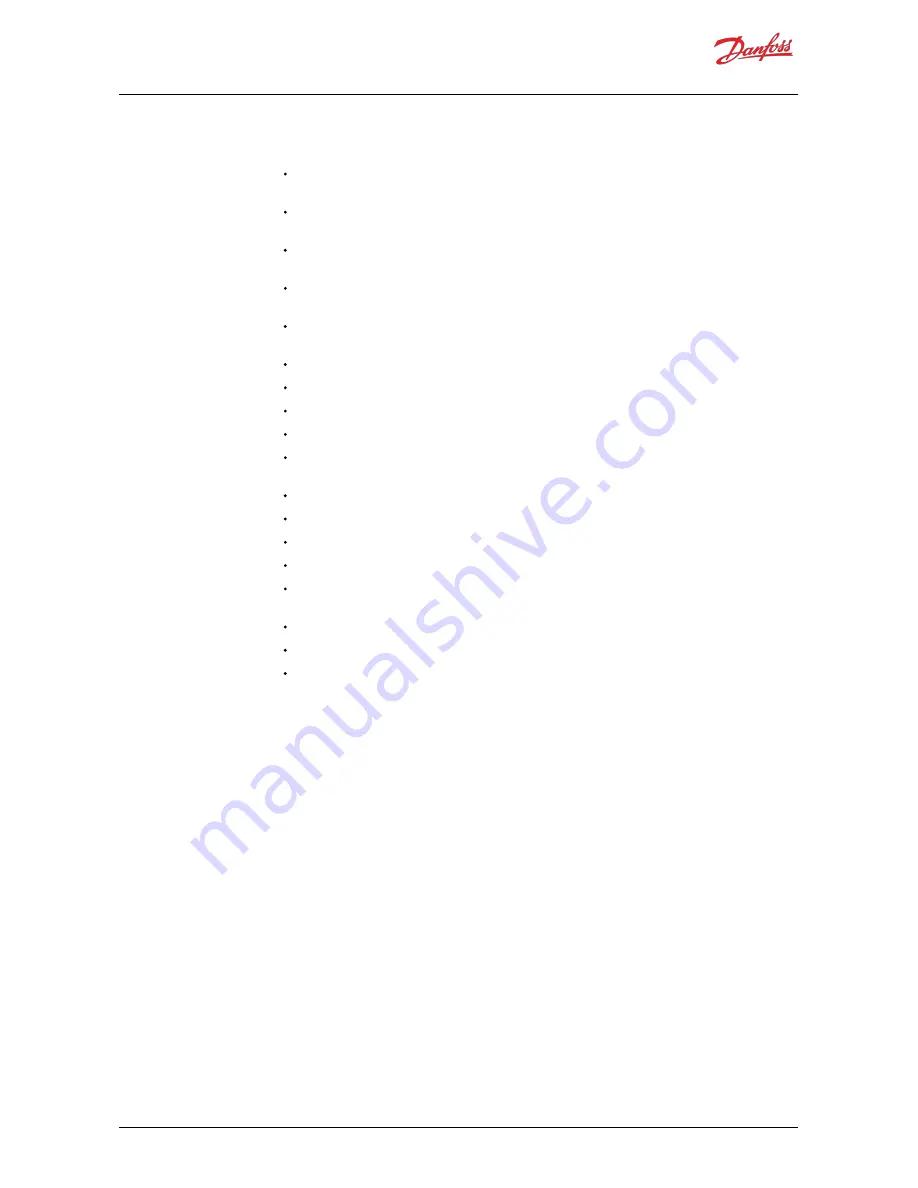
Using non-original service parts of wrong material causing corrosion problems and mechanical
failures in time.
Operating and performing maintenance for the electric machine without appropriate personal
protective equipment.
Using electric machine parts like frame, shaft end or terminal box for climbing or for support
for other structures.
Causing any kind of impact forces to the electric machine (for example hitting or hammering
or dropping objects).
Operating the electric machine with electric connections other than de ned in the manual
and/or other documents.
Operating the electric machine with insufficiently tightened connections or cable glands.
Operating the electric machine with power cables routed against the instructions.
Operating the electric machine without properly dimensioned and operating cooling system.
Operating the electric machine without following the bearing lubrication instructions.
Accessing the connection box(es) of the electric machine, doing maintenance or adjustment
operations on the electric machine with the electricity connected.
Accessing the connection box(es) if the shaft can be turned by an external prime mover.
Lifting the electric machine from wrong lifting points and without correct lifting equipment.
Lifting additional load with the machine.
Storing the electric machine outdoors in wet or dusty conditions.
Storing the electric machine without correct support to prevent rolling or falling of the
machines.
Using the electric machine in potentially explosive environment.
Allowing dirt or liquid to enter into the electric machine or connection box.
Using cables that can't withstand the maximum currents of the electric machine .
Used technology
The electric machine is a Syncronous Reluctance assisted Permanent Magnet (SRPM) machine. This
technology has several bene ts compared to standard permanent magnet (PM) technology and
traditional induction machine (IM) technology. The SRPM technology combines the bene ts of PM
and Syncronous Reluctance technology, having increased torque capability over wide speed range
and ability to produce torque to higher speeds. The electric machine efficiency at lower speeds is
also good.
The supply current to the machine stator windings create rotating magnetic eld, which in turn
rotates the rotor containing permanent magnets. In the syncronous permanent magnet machine,
the rotation of the rotor (shaft) is syncronized with the frequency of the power supply current. The
reluctance technology maximizes the pull-out torque of the machine.
The permanent magnets of the rotor are of salient-pole design, having embedded permanent
magnets in the rotor structure. This structure makes the electric machine mechanically more
stable and capable of higher speed operations. See Figure below illustrating the magnet topology
of the electric machine. The gure shows the principle only, and is not an exact illustration of the
structure.
EM-PMI375
3. Product overview
| BC265856307805en-000105
©
Danfoss | Produced By: Danfoss Power Solutions | January 2019 | 17
Summary of Contents for EM-PMI375-T1100
Page 1: ...User Guide Motor Generator EM PMI375 danfoss com...
Page 77: ......