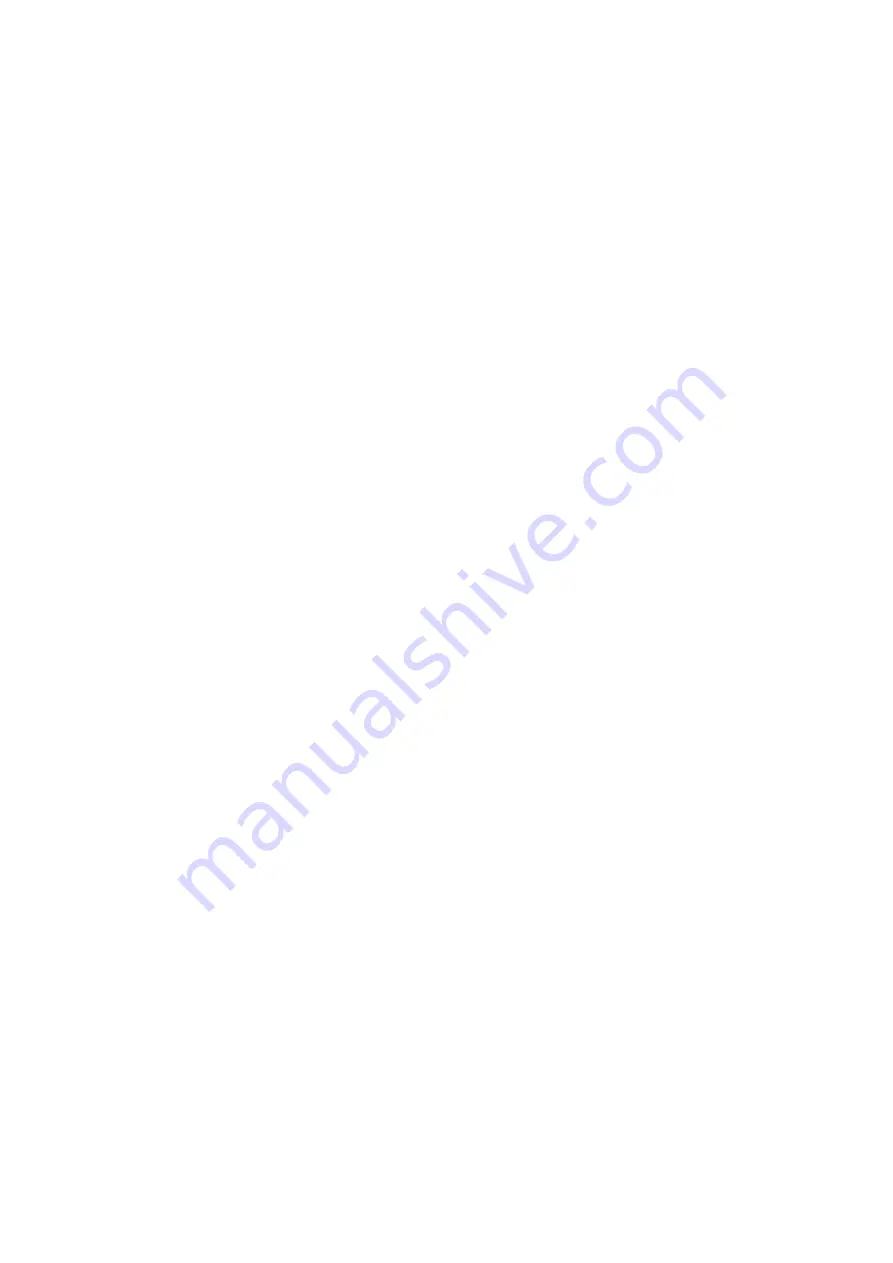
20
Installation, operation and maintenance instructions - VMGFE102
The system calculates the measured pressure diff erential
value, compares it with the user-selected set point value and
modulates the pump speed as necessary. The result is:
•
an increased fl ow rate, if a lower value than the set point
is measured,
•
an decreased fl ow rate, if a higher value than the set
point is measured.
This fl ow rate variation is realised, observing the minimum
and maximum admissible unit fl ow rates as well as the
minimum and maximum pump supply frequency values.
The pressure diff erential value maintained can in certain
cases be diff erent from the set point value:
•
If the set point value is too high (achieved for a higher
fl ow rate than the maximum value or a higher frequency
than the maximum value), the system settles at the
maximum fl ow rate or maximum frequency and this
results in a lower pressure diff erential than the set point.
•
If the set point value is too low (achieved for a lower fl ow
rate that the minimum value or a lower frequency than the
minimum value), the system settles at the minimum
fl ow rate or minimum frequency and this results in a
higher pressure diff erential than the set point.
Hydronic circuit cleaning procedure
First of all any possible pollution in the hydronic circuit must
be eliminated.
•
Start-up the pump using the forced start command (refer
to the controls manual).
•
Set the frequency to the maximum value to achieve a
higher fl ow rate.
•
If a “maximum fl ow rate exceeded” alarm occurs,
decrease the frequency until the correct value is found.
•
Read the fl ow rate at the user interface (refer to the
controls manual).
•
Let the pump run for two consecutive hours to clean the
hydronic circuit of the system (presence of solid
contaminants).
•
Repeat the fl ow rate reading and compare this value
with the initial value.
•
If the fl ow rate has decreased, this indicates that the
screen fi lter must be removed and cleaned, as the
hydronic circuit contains solid particles. In this case close
the shut-off valves at the water inlet and outlet (item 17)
and remove the screen fi lter (item 1) after emptying the
hydronic section of the unit (item 6).
•
Purge the air from the circuit (items 5 and 15).
•
Renew, if necessary, to ensure that the fi lter is not
contaminated.
Pressure diff erential set point control procedure
Once the circuit has been cleaned, select the hydronic circuit
confi guration for which the unit selection has been made (in
general, all receivers are open and all emitters are in the
on-state).
Read the fl ow rate on the user interface and compare the
value obtained to the theoretical selection value:
•
If the fl ow rate reading is higher than the specifi ed value,
decrease the pump supply frequency to decrease the
fl ow rate value (consult the control manual).
•
If the fl ow rate reading is lower than the specifi ed value,
increase the pump supply frequency to increase the fl ow
rate value (consult the control manual).
Continue this procedure until the nominal fl ow rate at the
required unit operating point is reached.
Read the pressure value at the unit outlet that corresponds to
the operating point reached (consult the control manual).
Stop the forced operation of the pump and proceed with the
confi guration of the unit for the required control mode
(consult the control manual).
Adjust the control parameters (refer to the control manual):
• Water
fl ow rate control method (pressure)
•
Pressure value to be controlled
The unit default confi guration is fi xed speed, 50 Hz.
NOTES:
•
If the low or high frequency limits are reached before the
specifi ed fl ow rate is reached, keep the frequency control
within the low or high limit and read the pressure value at
the unit outlet.
•
If the user knows the unit outlet pressure value to be
maintained in advance, this can be entered directly as the
correct parameter. The hydronic circuit cleaning procedure
must not be left out.
12.4 - Units with hydronic module and variable-speed
pump - temperature diff erence control
The system fl ow rate is not controlled by a nominal value.
It is adjusted by the system (pump speed variation) to
maintain the user-selected temperature diff erence value
(delta T) at the heat exchanger.
The temperature probes at the heat exchanger inlet and
outlet (items 8 and 9 in the typical hydronic circuit diagram)
are used as means of control.
The system reads the measured temperature values, calcu-
lates the corresponding temperature diff erence, compares it
with the user-selected set point value and modulates the
pump speed as necessary:
•
If a higher delta T value than the set point is measured,
the fl ow rate is increased.
•
If a lower delta T value than the set point is measured,
the fl ow rate is decreased.