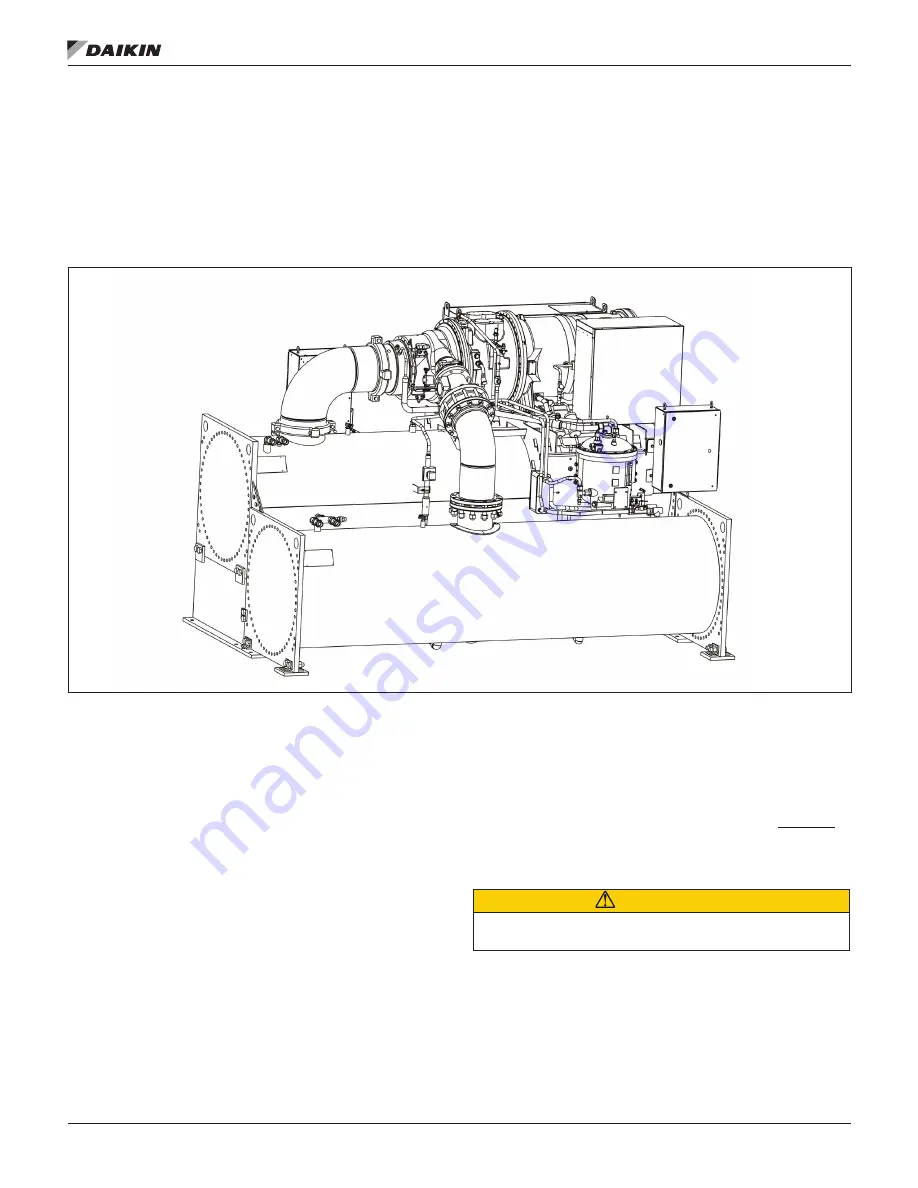
IOM 1274-3 • CENTRIFUGAL WATER CHILLERS 24 www.DaikinApplied.com
Installation
Retrofit Knockdown
Various knockdown arrangements are available as options and are ideal for retrofit applications with tight installation clearances.
Bolt-Together Construction - Type A
Chillers are built and shipped completely assembled with bolt-together construction on major components for field disassembly and
reassembly on the job site.
Figure 19: Bolt-Together Construction Option - Representative Schematic
Scope:
• Site disassembly and reassembly must be supervised or
completed by Daikin Applied service personnel.
• Unit is fully tested at the factory prior to shipment.
• The chiller is shipped completely assembled with the
full refrigerant charge, which must be recovered before
breaking any refrigerant connection.
• The refrigerant charge must be removed from the unit
if the vessels are to be separated. Exert the proper
precautions before attempting any disassembly, assume
the condenser isolation valves may have leaked and that
any component of the chiller may be pressurized with
refrigerant.
•
Suction and discharge lines have bolt-on flanges.
• Motor cooling line is brazed at mechanical connections.
•
Blockoff plates are required to cover any refrigerant
connection left open for extended periods of time. Contact
Daikin Applied service to obtain these parts.
• Check that no power is being applied to the unit. Before
disconnecting any wire, it is prudent to label its function
and connection point to facilitate re-connection.
• Unit ships with vessel and/or head insulation, if ordered.
• Unit ships with replacement refrigerant gaskets and
O-rings, stick-on wire ties, and touch-up paint. Some
insulation repair and touch-up painting may be required.
CAUTION
Standard torque specs must be followed when re-installing
bolts. Contact Daikin Applied service for this information.
NOTE: Schematic
shown without
waterboxes