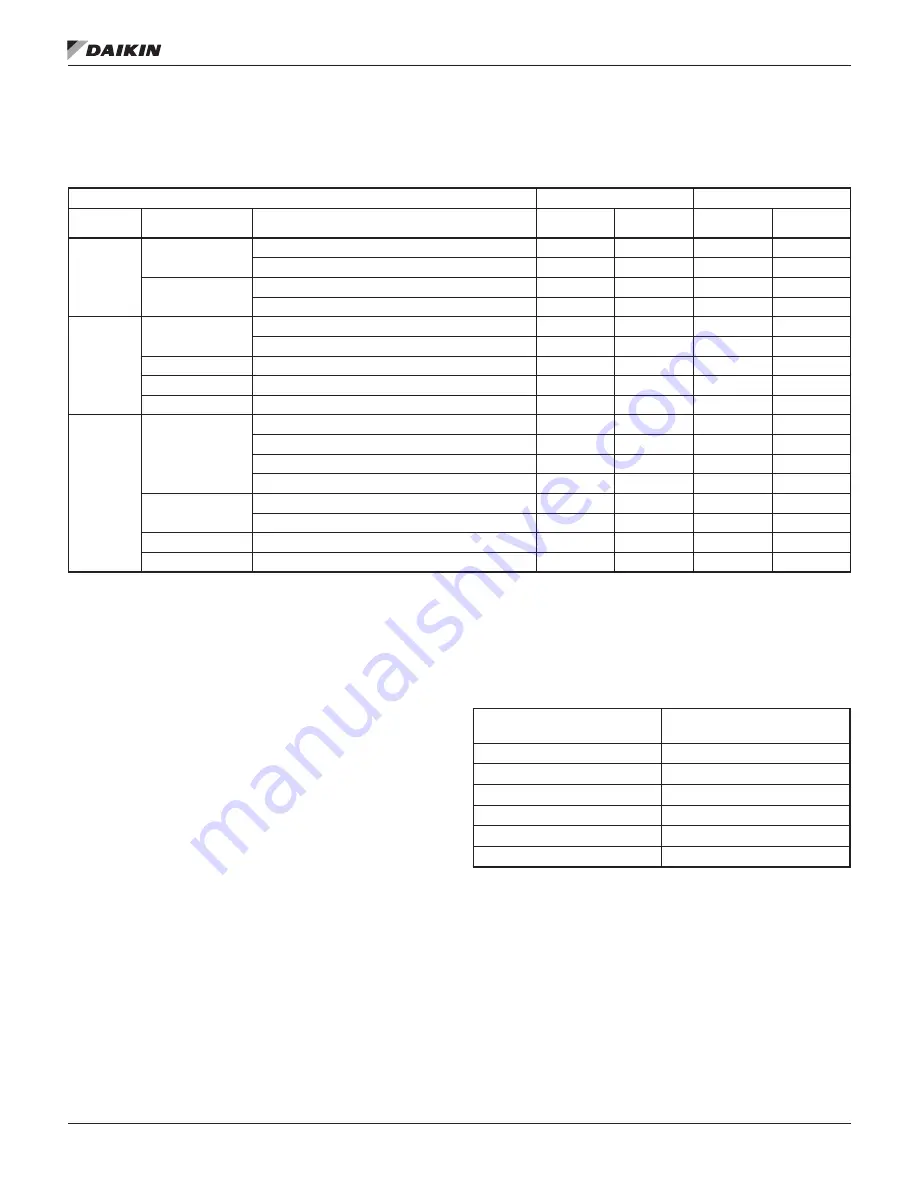
Installation
www.DaikinApplied.com
9
IOM 1274-3 • CENTRIFUGAL WATER CHILLERS
Operating Limits
Table 2: Operating/Standby Limits
Acceptable Temperatures (WSC, HSC, TSC)
1
R-513A
R-134a
Condition
Component
Description
Min Temp
°F (°C)
Max Temp
°F (°C)
Min Temp
°F (°C)
Max Temp
°F (°C)
Standby
Evaporator
Entering Fluid
35 (1.7)
86 (30)
35 (1.7)
90 (32.2)
Entering Fluid w/ Antifreeze
2
20 (-6.7)
86 (30)
20 (-6.7)
90 (32.2)
Equipment Room
Air w/ Water in Vessels & Oil Cooler
40 (4.4)
104 (40)
40 (4.4)
104 (40)
Air w/ no Water in Vessels & Oil Cooler
0 (-17.8)
0 (-17.8)
0 (-17.8)
113 (45)
Startup
Evaporator
Entering Fluid
38 (3.3)
100 (37.8)
38 (3.3)
100 (37.8)
Entering Fluid w/ Antifreeze
2
20 (-6.7)
100 (37.8)
20 (-6.7)
100 (37.8)
Condenser
Entering Fluid
35 (1.7)
110 (43.3)
35 (1.7)
111 (43.9)
Oil Cooler
Entering Fluid
35 (1.7)
80 (26.7)
35 (1.7)
80 (26.7)
Equipment Room
Air
40 (4.4)
104 (40)
40 (4.4)
104 (40)
Operating
Evaporator
Entering Fluid
38 (3.3)
86 (30)
38 (3.3)
90 (32.2)
Leaving Fluid
38 (3.3)
60 (15.6)
38 (3.3)
60 (15.6)
Entering Fluid w/ Antifreeze
2
20 (-6.7)
86 (30)
20 (-6.7)
90 (32.2)
Leaving Fluid w/ Antifreeze
2
20 (-6.7)
60 (15.6)
20 (-6.7)
60 (15.6)
Condenser
Entering Fluid
55 (12.8)
104 (40)
55 (12.8)
105 (40.6)
Leaving Fluid
See Note
3
110 (43.3)
See Note
3
111 (43.9)
Oil Cooler
Entering Fluid
35 (1.7)
80 (26.7)
35 (1.7)
80 (26.7)
Equipment Room
Air
40 (4.4)
104 (40)
40 (4.4)
104 (40)
NOTES:
1
Contact a Daikin Applied representative for performance at specific operating conditions, as some limits depend on unit configuration (including heating and
heat recovery mode limits)
2
Antifreeze temperature limits must have appropriate glycol concentration
3
Depends on specific selection/rating conditions
Field Insulation
If the optional factory-installation of thermal evaporation
insulation is not ordered, insulation should be field installed
to reduce heat loss and prevent condensation from forming.
Insulation should cover:
• the evaporator barrel, tube sheet, and waterboxes.
• the suction line from the top of the evaporator to the
compressor inlet flange.
• the compressor support brackets welded to the
evaporator.
• the liquid line from the expansion valve to the evaporator
inlet, including the expansion valve.
• the part load balance valve to the evaporator.
Approximate total square footage of insulation surface required
for individual packaged chillers is tabulated by code and can
be found in
Table 4
. Condenser references included for TSC
model units only.
Table 4: Insulation Area Required for Vessels
Vessel Code
Insulation Area
sq. ft. (m2)
E2612 / C2612
102 (9.4)
E3012 / C3012
115 (10.6)
E3612 / C3612
129 (11.9)
E4212 / C4212
148 (13.7)
E4216 / C4216
264 (24.5)
E4816 / C4816
302 (28.1)
Water Piping
All evaporators and condensers have OGS-type grooved water
connections (adhering to Standard AWWA C606) or optional
flange connections. The installing contractor must provide
matching mechanical connections. Be sure that water inlet
and outlet connections match certified drawings and nozzle
markings. PVC piping should not be used.