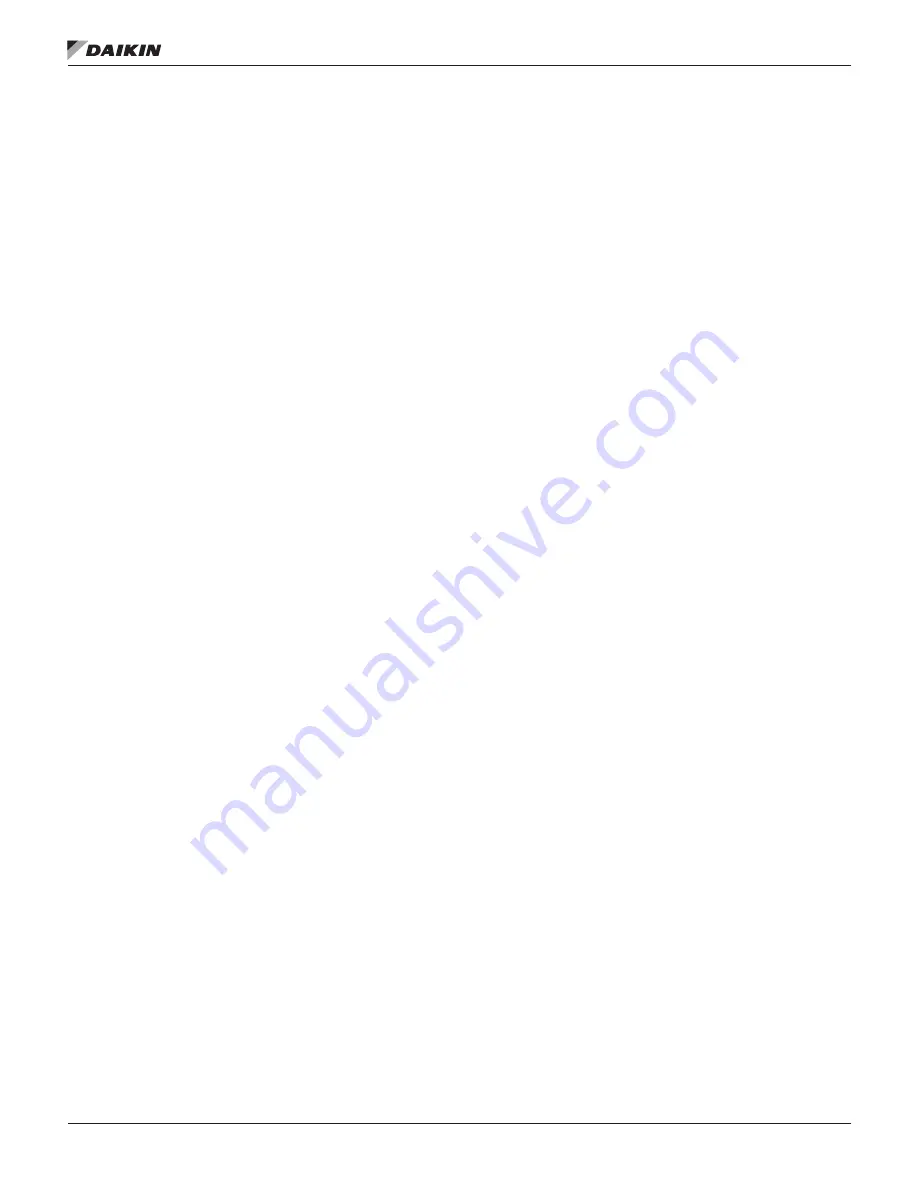
IOM 1274-3 • CENTRIFUGAL WATER CHILLERS 68 www.DaikinApplied.com
Unit Startup and Maintenance
are more hygroscopic than mineral oils and can contain much
more water in solution. For this reason, it is imperative that
extra care be used when handling polyolester oils to minimize
their exposure to ambient air. Extra care must also be used
when sampling to ensure that sample containers are clean,
moisture-free leak proof and non-permeable.
Daikin Applied has done extensive testing in conjunction
with refrigerant and lubricating oil manufacturers and has
established guidelines to determine action levels and the type
of action required.
In general Daikin Applied does not recommend changing
lubricating oils and filters on a periodic basis. The need to
change lubricating oil and filters should be based on a careful
consideration of oil analysis, vibration analysis and knowledge
of the operating history of the equipment. A single oil sample is
not sufficient to estimate the condition of the chiller. Oil analysis
is only useful if employed to establish wear trends over time.
Changing lubricating oil and filter prior to when its needed will
reduce the effectiveness of oil analysis as a tool in determining
machinery condition.
The following metallic elements or contaminates and their
possible sources will typically be identified in an oil wear
analysis:
Aluminum
Typical sources of aluminum are bearings, impellers, seals
or casting material. An increase in aluminum content in the
lubricating oil may be an indication of bearing, impeller or other
wear. A corresponding increase in other wear metals may also
accompany an increase in aluminum content.
Copper
The source of copper can be the evaporator or condenser
tubes, copper tubing used in the lubrication and motor cooling
systems or residual copper from the manufacturing process.
The presence of copper may be accompanied by a high TAN
(total acid number) and high moisture content. High copper
contents may also result from residual mineral oil previously
used in machines. Some mineral oils contained wear inhibitors
which react with copper and result in high copper content in
lubricating oil.
Iron
Iron in the lubricating oil can originate from compressor
castings, oil pump components, shells, tube sheets, tube
supports, shaft material and rolling element bearings. High iron
content may also result from residual mineral oil previously
used in machines. Some mineral oils contain wear inhibitors
which react with iron and can result in a high iron content in the
lubricating oil.
Tin
The source of tin may be from bearings.
Zinc
There is no zinc used in the bearings on Daikin Applied chillers.
The source, if any, may be from additives in some mineral oils.
Lead
The source of lead in Daikin Applied centrifugal chillers is the
thread sealant compounds used during chiller assembly. The
presence of lead in the lubricating oil in Daikin Applied chillers
does not indicate bearing wear.
Silicon
Silicon can originate from residual particles of silicon left from
the manufacturing process, filter drier material, dirt or anti-foam
additives from residual mineral oil which may be present in
machines.
Moisture
Moisture in the form of dissolved water can be present in
lubricating oil to varying degrees. Some polyolester oils may
contain up to 50 parts per million (ppm) of water from new
unopened containers. Other sources of water may be the
refrigerant (new refrigerant may contain up to 10 ppm water),
leaking evaporator condenser tubes or oil coolers, or moisture
introduced by the addition of either contaminated oil or
refrigerant or improperly handled oil.
Liquid R-134a has the ability to retain up to 1400 ppm of water
in solution at 100 degrees F. With 225 ppm of water dissolved
in liquid R-134a, free water would not be released until the
liquid temperature reached -22 degrees F. Liquid R-134a can
hold approximately 470 ppm at 15 degrees F (an evaporator
temperature which could be encountered in ice applications).
Since free water is what causes acid production, moisture
levels should not be of a concern until they approach the free
water release point.
A better indicator of a condition which should be of concern is
the TAN (Total Acid Number). A TAN below 0.09 requires no
immediate action. TANs above 0.09 require certain actions.
In the absence of a high TAN reading and a regular loss of
refrigerant oil (which may indicate a heat transfer surface leak)
a high moisture content in an oil wear analysis is probably due
to handling or contamination of the oil sample. It should be
noted that air (and moisture) can penetrate plastic containers.
Metal or glass containers with gasket in the top will slow
moisture entry.
In conclusion, a single element of an oil analysis should not
be used as the basis to estimate the overall internal condition
of a Daikin Applied chiller. The characteristics of the lubricants
and refrigerants, and knowledge of the interaction of wear
materials in the chiller must be considered when interpreting
a wear metal analysis. Periodic oil analysis performed by a
reputable laboratory and used in conjunction with compressor
vibration analysis and operating log review can be helpful tools
in estimating the internal condition of a Daikin Applied chiller.
Normal Sample Intervals
Daikin Applied recommends that an oil analysis be performed
annually. Professional judgment must be exercised under
unusual circumstances, for example, it might be desirable to
sample the lubricating oil shortly after a unit has been placed