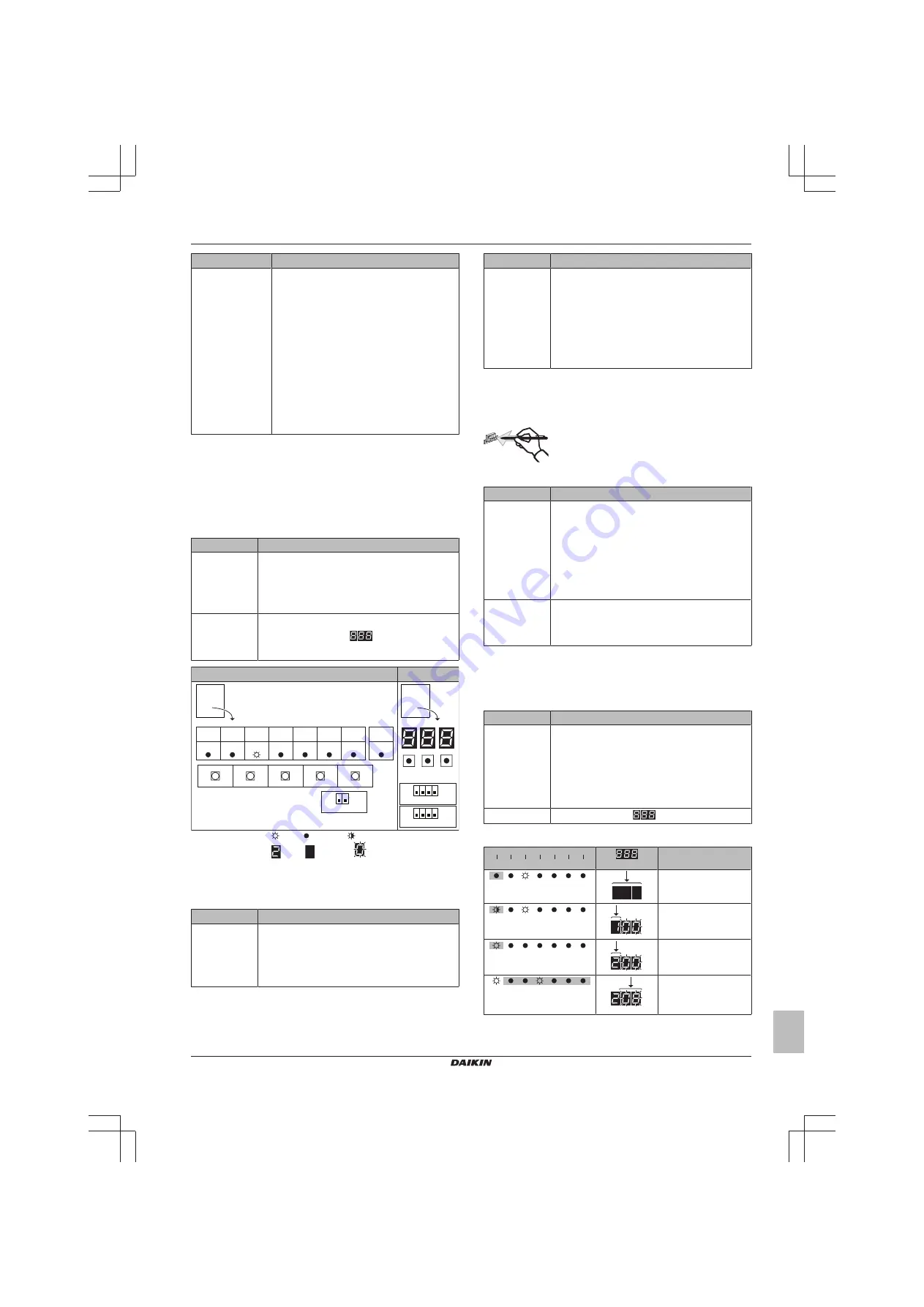
6 Configuration
Installation and operation manual
19
8T7Y1B
VRV IV compressor unit for indoor installation
4P408443-1B – 2016.04
Mode
Description
Mode 2
(field settings)
Mode 2 is used to change the field settings of
the system. Consulting the current field setting
value and changing the current field setting
value is possible.
In general, normal operation can be resumed
without special intervention after changing field
settings.
Some field settings are used for special
operation (e.g., 1 time operation, recovery/
vacuuming setting, manual adding refrigerant
setting, etc.). In such a case, it is required to
abort the special operation before normal
operation can restart. It will be indicated in
below explanations.
6.1.2
To access the field setting components
"5.1.1 To open the compressor unit" on page 10
6.1.3
Field setting components
The components to make field settings differ depending on the
model.
Model
Field setting components
5 HP
▪ Push buttons (BS1~BS5)
▪ 7‑LEDs display (H1P~H7P)
▪ H8P: LED for indication during initialisation
▪ DIP switches (DS1)
8 HP
▪ Push buttons (BS1~BS3)
▪ 7‑segments display (
)
▪ DIP switches (DS1 and DS2)
5 HP
BS2
SET
BS1
MODE
BS3
RETURN
BS4
TEST
BS5
RESET
H1P
H2P
H3P
H4P
H5P
H6P
H7P
H8P
1 2
OFF
ON
DS1
1 2 3 4
OFF
ON
DS1
1 2 3 4
OFF
ON
DS2
MULTI
DEMAND
L.N.O.P.
SLAVE
MASTER
IND
TEST/
HWL
MODE
8 HP
A1P
BS1 BS2 BS3
A1P
ON (
) OFF ( ) Flashing (
)
ON (
) OFF (
) Flashing (
)
DIP switches
Only change the factory settings if you install a cool/heat selector
switch.
Model
DIP switch
5 HP
▪ DS1‑1: COOL/HEAT selector (refer to the
manual of the cool/heat selector switch).
OFF=not installed=factory setting
▪ DS1‑2: NOT USED. DO NOT CHANGE THE
FACTORY SETTING.
Model
DIP switch
8 HP
▪ DS1‑1:
COOL/HEAT
selector
(see
"3.3.1 Possible options for the compressor unit
and heat exchanger unit" on page 6
). OFF=not
installed=factory setting
▪ DS1‑2~4: NOT USED. DO NOT CHANGE THE
FACTORY SETTING.
▪ DS2‑1~4: NOT USED. DO NOT CHANGE THE
FACTORY SETTING.
Push buttons
Use the push buttons to make the field settings. Operate the push
buttons with an insulated stick (such as a closed ball-point pen) to
avoid touching of live parts.
The push buttons differ depending on the model.
Model
Push buttons
5 HP
▪ BS1: MODE: For changing the set mode
▪ BS2: SET: For field setting
▪ BS3: RETURN: For field setting
▪ BS4: TEST: For test operation
▪ BS5: RESET: For resetting the address when
the wiring is changed or when an additional
indoor unit is installed
8 HP
▪ BS1: MODE: For changing the set mode
▪ BS2: SET: For field setting
▪ BS3: RETURN: For field setting
7‑LEDs display
The display gives feedback about the field settings, which are
defined as [Mode-Setting]=Value.
The display differs depending on the model.
Model
Display
5 HP
7‑LEDs display:
▪ H1P: Shows the mode
▪ H2P~H7P: Shows the settings and values,
represented in binary code
(H8P: NOT used for field settings, but used during
initialisation)
8 HP
7‑segments display (
)
Example:
H1P H2P H3P H4P H5P H6P H7P
-
+
+
+
+
+
[
H1P
32 16
8
4
2
1]
Description
(H1P OFF)
Default situation
(H1P flashing)
Mode 1
(H1P ON)
Mode 2
+
+
+
+
+
0
0
8
0
0
0
(H2P~H7P = binary 8)
Setting 8
(in mode 2)
Summary of Contents for VRV IV RKXYQ8T7Y1B
Page 41: ......
Page 42: ......
Page 43: ......
Page 44: ...4P408443 1 B 0000000 4P408443 1B 2016 04 Copyright 2015 Daikin ...