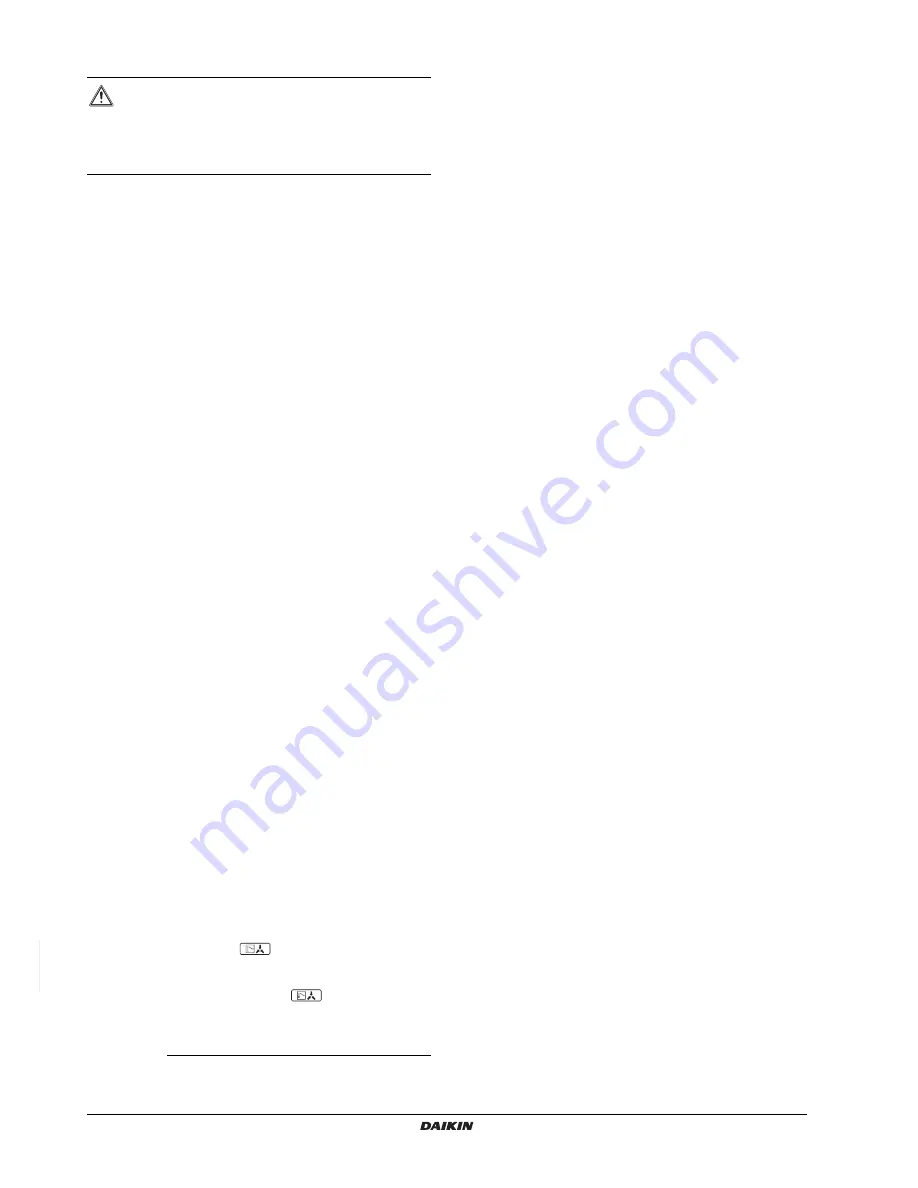
Installation and operation manual
59
RYYQ+RYMQ+RXYQ8~20T7Y1B
VRV IV System Air Conditioner
4P329765-1 – 2012.09
8.
Maintenance
8.1.
Maintenance after a long stop period (e.g., at the
beginning of the season)
Check and remove everything that might be blocking inlet and
outlet vents of indoor units and outdoor units.
Clean air filters and casings of indoor units
(9)
. Refer to the
operation manual supplied with the indoor units for details on
how to proceed and make sure to install cleaned air filters back
in the same position.
Turn on the power at least 6 hours before operating the unit in
order to ensure smoother operation. As soon as the power is
turned on, the user interface display appears.
8.2.
Maintenance before a long stop period (e.g., at the
end of the season)
Let the indoor units run in fan only operation for about half a day
in order to dry the interior of the units. Refer to
"6.1. Cooling,
heating, fan only, and automatic operation" on page 55
for
details on fan only operation.
Turn off the power. The user interface display disappears.
Clean air filters and casings of indoor units
(9)
. Refer to the
operation manual supplied with the indoor units for details on
how to proceed and make sure to install cleaned air filters back
in the same position.
9.
Symptoms that are not air conditioner
troubles
Following symptoms are not air conditioner troubles:
Symptom 1: The system does not operate
The air conditioner does not start immediately after the ON/OFF
button on the user interface is pressed. If the operation lamp
lights, the system is in normal condition. To prevent overloading
of the compressor motor, the air conditioner starts 5 minutes
after it is turned ON again in case it was turned OFF just before.
The same starting delay occurs after the operation mode
selector button was used.
If "Under Centralized Control" is displayed on the user interface
and pressing the operation button causes the display to blink for
a few seconds indicating that the central device is controlling the
unit. The blinking display indicates that the user interface cannot
be used.
The system does not start immediately after the power supply is
turned on. Wait one minute until the micro computer is prepared
for operation.
Symptom 2: Cool/Heat cannot be changed over
When the display shows
(change-over under centralized
control), it shows that this is a slave user interface.
When the cool/heat changeover remote control switch is
installed and the display shows
(change-over under
centralized control). This is because cool/heat changeover is
controlled by the cool/ heat changeover remote control switch.
Ask your dealer where the remote control switch is installed.
Symptom 3: Fan operation is possible, but cooling and heating
do not work
Immediately after the power is turned on. The micro computer is
getting ready to operate and is performing a communication
check with all indoor units. Please wait 12 minutes (max.) till this
process is finished.
Symptom 4: The fan strength does not correspond to the setting
The fan speed does not change even if the fan speed
adjustment button in pressed. During heating operation, when
the room temperature reaches the set temperature, the outdoor
unit goes off and the indoor unit changes to whisper fan speed.
This is to prevent cold air blowing directly on occupants of the
room. The fan speed will not change even if the button is
pressed, when another indoor unit is in heating operation.
Symptom 5: The fan direction does not correspond to the
setting
The fan direction does not correspond with the user interface
display. The fan direction does not swing. This is because the
unit is being controlled by the micro computer.
Symptom 6: White mist comes out of a unit
Symptom 6.1: Indoor unit
When humidity is high during cooling operation
If the interior of an indoor unit is extremely contaminated, the
temperature distribution inside a room becomes uneven. It is
necessary to clean the interior of the indoor unit. Ask your dealer
for details on cleaning the unit. This operation requires a
qualified service person.
Immediately after the cooling operation stops and if the room
temperature and humidity are low. This is because warm
refrigerant gas flows back into the indoor unit and generates
steam.
Symptom 6.2: Indoor unit, outdoor unit
When the system is changed over to heating operation after
defrost operation. Moisture generated by defrost becomes
steam and is exhausted.
Symptom 7: The user interface display reads "
U4
" or "
U5
" and
stops, but then restarts after a few minutes
This is because the user interface is intercepting noise from
electric appliances other than the air conditioner. The noise
prevents communication between the units, causing them to
stop. Operation automatically restarts when the noise ceases.
Symptom 8: Noise of air conditioners
Symptom 8.1: Indoor unit
A "zeen" sound is heard immediately after the power supply is
turned on.
The electronic expansion valve inside an indoor unit starts
working and makes the noise. Its volume will reduce in about
one minute.
A continuous low "shah" sound is heard when the system is in
cooling operation or at a stop.
When the drain pump (optional accessories) is in operation, this
noise is heard.
A "pishi-pishi" squeaking sound is heard when the system stops
after heating operation.
Expansion and contraction of plastic parts caused by
temperature change make this noise.
A low "sah", "choro-choro" sound is heard while the indoor unit is
stopped.
When the other indoor unit is in operation, this noise is heard. In
order to prevent oil and refrigerant from remaining in the system,
a small amount of refrigerant is kept flowing.
CAUTION
Pay attention to the fan.
It is dangerous to inspect the unit while the fan is running.
Be sure to turn off the main switch and to remove the fuses
from the control circuit located in the outdoor unit.
(9) Contact your installer or maintenance person to clean air filters
and casings of the indoor unit. Maintenance tips and
procedures for cleaning are provided in the
installation/operation manuals of dedicated indoor units.
Summary of Contents for RYYQ8T7Y1B
Page 68: ......
Page 69: ......
Page 70: ......
Page 72: ...4P329765 1 2012 09 Copyright 2012 Daikin 4P329765 1 0000000U...