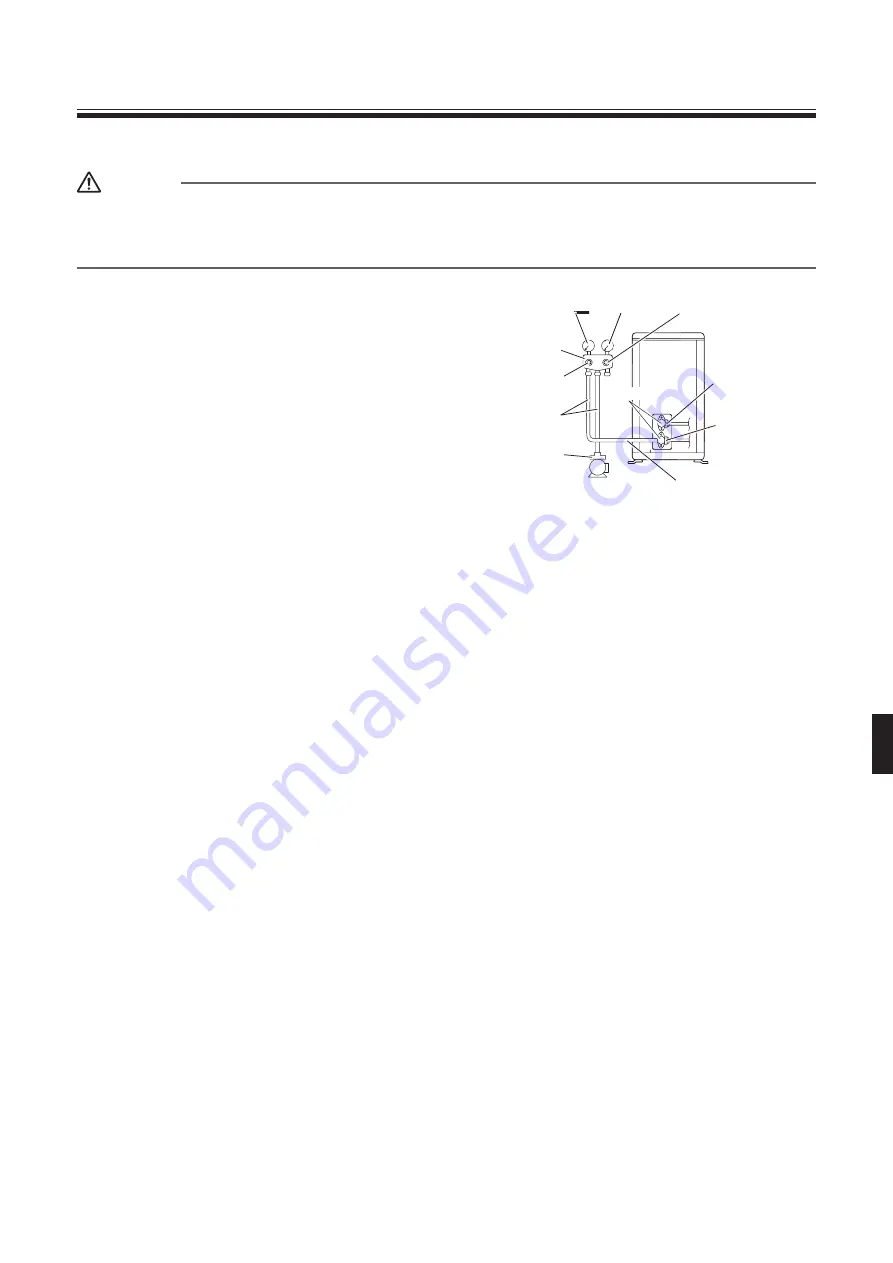
14
14
6.
Evacuating the air with a vacuum pump and checking gas leakage
WARNING
• Do not mix any substance other than the specifi ed refrigerant (R32) into the refrigeration cycle.
•
When refrigerant gas leaks occur, ventilate the room as soon and as much as possible.
•
R32, as well as other refrigerants, should always be recovered and never be released directly into the environment.
•
Use tools for R32 or R410A (such as the gauge manifold, charging hose, or vacuum pump adapter).
•
When piping work is completed, it is necessary to evacuate
the air with a vacuum pump and check for gas leakage.
• Use a hexagonal wrench (4mm) to operate the stop valve rod.
• All refrigerant pipe joints should be tightened with a torque
wrench at the specifi ed tightening torque.
Compound
pressure gauge
Pressure
meter
Gauge
manifold
Low-pressure
valve
High-pressure
valve
Charging
hoses
Vacuum pump
adapter
Vacuum pump
Valve caps
Gas stop
valve
Service port
Liquid stop
valve
1)
Connect projection side of charging hose (which comes from gauge manifold) to gas stop valve’s service port.
2) Fully open gauge manifold’s low-pressure valve (Lo) and completely close its high-pressure valve (Hi).
(High-pressure valve subsequently requires no operation.)
3) Do vacuum pumping and make sure that the compound pressure gauge reads –0.1MPa (–76cmHg).
(The vacuum pump should run for at least 10 minutes.)
4) Close gauge manifold’s low-pressure valve (Lo) and stop vacuum pump.
(Keep this state for a few minutes to make sure that the compound pressure gauge pointer does not swing back.)*1
5)
Remove covers from liquid stop valve and gas stop valve.
6)
Turn the liquid stop valve’s rod 90° counterclockwise with a hexagonal wrench to open valve.
Close it after 5 seconds, and check for gas leakage.
Using soapy water, check for gas leakage from indoor unit’s fl are and outdoor unit’s fl are and valve rods.
After the check is complete, wipe all soapy water off.
7)
Disconnect charging hose from gas stop valve’s service port, then fully open liquid and gas stop valves.
(Do not attempt to turn valve rod beyond its stop.)
8)
Tighten valve caps and service port caps for the liquid and gas stop valves with a torque wrench at the specifi ed torques.
*1 If the compound pressure gauge pointer swings back, refrigerant may have water content or a loose pipe joint may exist. Check all
pipe joints and retighten nuts as needed, then repeat steps 2) through 4).
01_EN_3P338604-1E.indd 14
2/18/2019 14:09:24