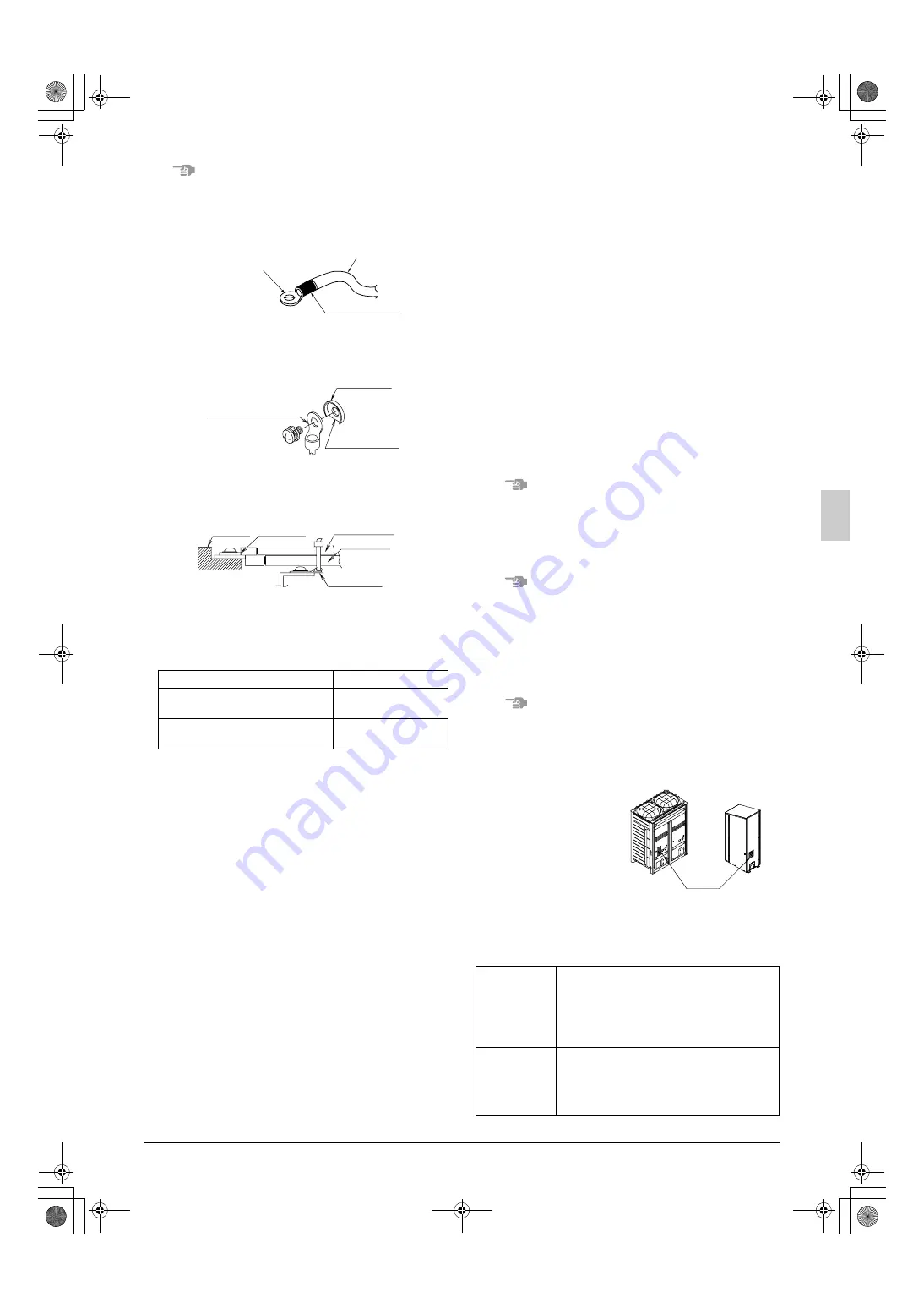
English
14
Note
•
For wiring, use the designated power wire and connect firmly,
then secure to prevent outside pressure being exerted on the ter-
minal board.
•
Be sure to use crimp-style terminal with insulating sleeves for
connections. (See the figure below.)
•
When pulling the ground wire out, wire it so that it comes through
the cut out section of the cup washer. (See the figure below.) An
improper ground connection may prevent a good ground from
being achieved.
•
When two wires are connected to a single terminal, connect them
so that the rear sides of the crimp contacts face each other. Also,
make sure the thinner wire is on top, securing the two wires simul-
taneously to the resin hook using the included clamp (1).
•
Use an appropriate screwdriver for tightening the terminal screws.
A screwdriver with a small head will strip the head and make
proper tightening impossible.
Over-tightening the terminal screws may break them.
See the following table for the tightening torque of the terminal
screws.
7-6 Procedure for Wiring Inside Units
•
Referring to figure 27 and 28, secure and wire the power and
transmission wiring using the included clamp (1), (2), and (3).
•
Wire so that the ground wiring does not come into contact with the
compressor lead wiring.
If they touch, this may have an adverse effect on other devices.
•
Make sure all wiring do not contact to the pipes (hatching parts in
the figure 27 and 28).
•
The transmission wiring must be at least 50 mm away from the
power wiring.
(Refer to figure 27)
1.
For RTSQ8 to RTSQ12PY1
2.
For RTSQ14 and RTSQ16PY1
3.
In the case of pulling in the power wire and ground wire
from the left-hand side.
4.
Conduit
5.
Stay
6.
Fix to the stay with the included clamp (3).
7.
Power wiring
8.
Ground wiring
9.
Transmission wiring
10.
In the case of pulling in the power wire and ground wire
from the right-hand side.
11.
In the case of pulling in the transmission wire from the
piping outlet.
12.
In the case of pulling in the power wiring and ground wir-
ing from the front side.
13.
Separate at least 50 mm.
14.
In the case of pulling in the transmission wiring from the
front side.
15.
Fix to the rear side of the side plate with the included clamp (2).
16.
Support
17.
Fix to the rear side of the support with the included clamp (1).
18.
Fix to the rear side of the support with the included clamp (2).
19.
Perform wiring carefully so that the sound blanket of the
compressor will not be dismounted.
(Refer to figure 28)
1.
For BTSQ20PY1
2.
Power wiring
3.
Ground wiring
4.
Transmission wiring
5.
In the case of pulling in the power wiring and ground wir-
ing from the left-hand side.
6.
In the case of pulling in the power wiring and ground wir-
ing from the right-hand side.
7.
Pull in the transmission wiring from the piping outlet.
8.
Perform wiring (on both right- and left-hand sides) so that
the sealing materials on the bottom of the
EL.COMPO.BOX will not be deformed.
9.
Perform wiring carefully so that the sound blanket of the
compressor will not be dismounted.
Note
•
After wiring work is completed, check to make sure there are no
loose connections among the electrical parts in the
EL.COMPO.BOX.
8.
TESTS AND INSULATION WORK
Note
•
Always use nitrogen gas for the airtightness test.
•
Absolutely do not open the shutoff valve until the main power ciruit
insulation measurement (refer to 8-3) has been completed. (mea-
suring after the shutoff valve is opened will cause the insulation
value to drop.)
8-1 Air tight test and vacuum drying
•
After finished piping work, carry out air tight test and vacuum drying.
Note
•
Be sure to conduct the airtight test and vacuum drying through the
service port of the shutoff valves of the liquid pipe and gas pipe,
and shutoff valve of the equalizer pipe (for the multi outdoor unit
system only) of the outdoor unit and the service port of the liquid
pipe and gas pipe of the function unit.
See the [R410A] Label
attached to the front plate of
the each unit for details on
the location of the service
port (see figure at right).
•
See
[Shutoff valve opera-
tion procedure]
in “
9-1
Before working
” for details
on handling the shutoff valve.
•
Pay attention to refrigerant
leakage when connecting a
charge hose to the refrigerant charge port. The refrigerant charge
port is connected to the piping inside the product, and the piping
is charged with refrigerant before shipping from the factory.
<Needed tools>
Screw size
Tightening torque (N·m)
M8 (Power and ground terminals of
outdoor unit)
5.5 - 7.3
M5 (Power and ground terminals of
outdoor unit)
2.0 - 3.0
Power wire
Crimp-style terminal
Insulating sleeve
Crimp-style terminal
Cup washer
Cut out section
Terminal
block
Crip style
terminal
Wire : narrow
Wire : thick
Resin hook
Gauge manifold
Charge hose
valve
• To prevent entry of any impurities and insure
sufficient pressure resistance, always use the
special tools dedicated for R410A.
• Use charge hose that have pushing stick for
connecting to service port of shutoff valves or
refrigerant charge port.
Vacuum pump
• Take care the pump oil never flow backward
into the refrigerant pipe during the pump stops.
• The vacuum pump for vacuum drying should
be able to lower the pressure to –100.7kPa
(5 Torr –755mm Hg).
[R410A] Label
Outdoor unit
Function unit
01_EN_3P201178-10P.fm Page 14 Wednesday, September 2, 2009 11:10 AM