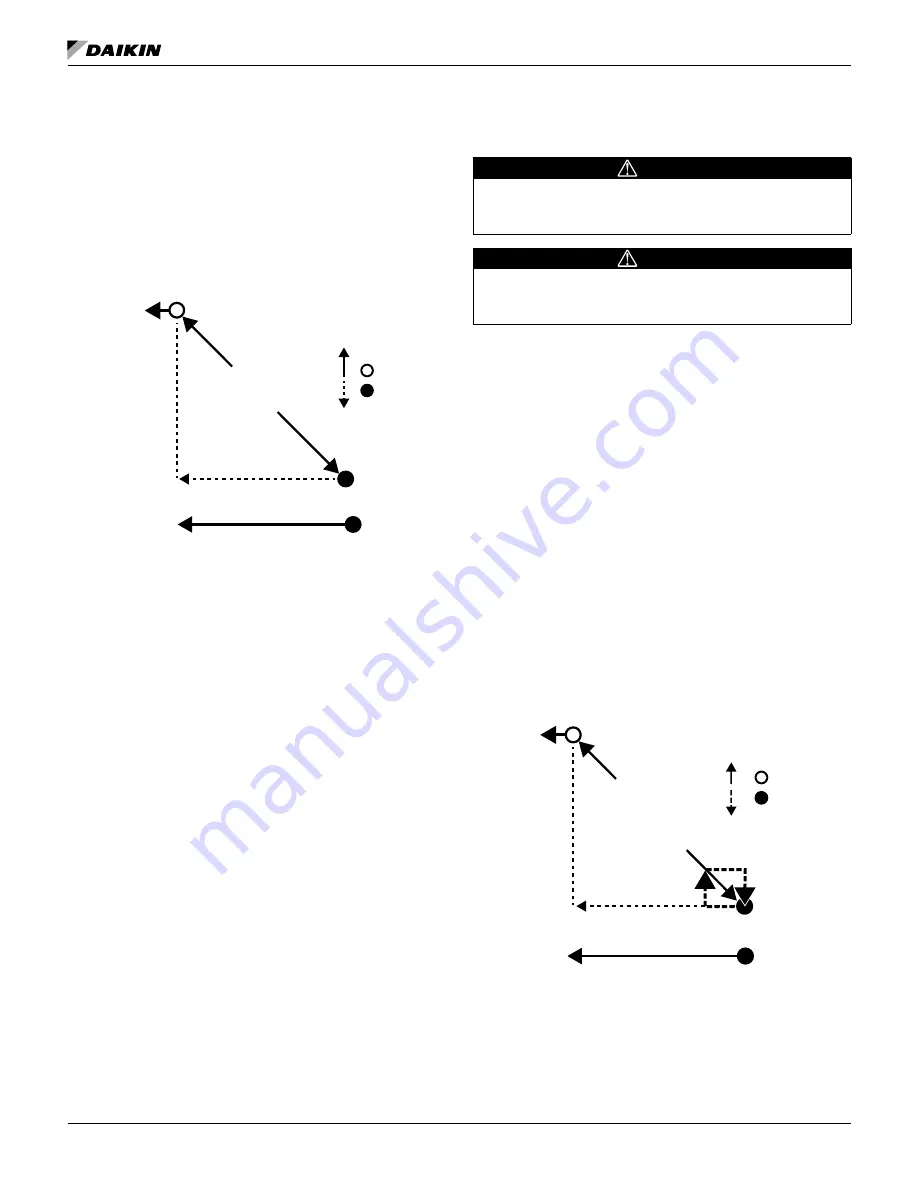
OM 1280-2 • MICROTECH UNIT CONTROLLER 16 www.DaikinApplied.com
Description of Operation
Wet Heat Valve Control
If the UVC is configured for a modulating wet heat valve or a
modulating chilled water valve both are operated by proportional
actuators. The modulating valve actuator contains a spring that
ensures that the wet heat valve is open and that the chilled water
valve is closed upon loss of power. Each proportional actuator is
driven by the UVC using 0-10VDC outputs (scaled to 2-10VDC).
Figure 8: Heat State Operation - Valve Control
The 2-way modulating hot water (or 2-pipe CW/HW) valve is
furnished to fail open to the coil. 24VAC is required to power
the valve actuator. When the actuator is powered, a controller
will provide a 2-10VDC signal to the actuator. A signal of 2VDC
or less will drive the valve closed; the valve will drive open as
the signal increases to a maximum of 10VDC.
If 24VAC is lost to the actuator, valve will spring-return to its
fail position (open to the coil for hot water or 2-pipe CW/HW
valves).
The 3-way modulating hot water (or 2-pipe CW/HW) valve is
furnished to fail open to the coil. 24VAC is required to power
the valve actuator. When the actuator is powered, a controller
will provide a 2-10VDC signal to the actuator. A signal of 2VDC
or less will drive the valve closed (bypassing coil); the valve will
drive open as the signal increases to a maximum of 10VDC
(flow through the coil).
If 24VAC is lost to the actuator, valve will spring-return to its fail
position (open to the coil for Hot Water or 2-Pipe HW/CH water
valves).
The 2-way modulating steam valve is furnished to fail open to
the coil. 24VAC is required to power the valve actuator. When
the actuator is powered, a controller will provide a 2-10VDC
signal to the actuator. A signal of 2VDC or less will drive the
valve closed; the valve will drive open as the signal increases
to a maximum of 10VDC.
If 24VAC is lost to the actuator, valve will spring-return to its fail
position (open to the coil for steam valves).
Wet Heat Face and Bypass Damper and
End-of-Cycle Valve Control
CAUTION
Both a wet-heat end-of-cycle (EOC) valve and a chilled water end-of-cycle
(EOC) valve are strongly recommended by Daikin. If an EOC valve is not
installed, it is likely that over-heating or over-cooling of the space will occur.
CAUTION
An end-of-cycle (EOC) valve is required for DX units with hydronic heat and
F&BP dampers units since the wet coil and the refrigerant coil share the same
air path. If an EOC valve is not installed, overheating of the space can occur.
The UVC can be configured for a two-position, normally-open wet
heat end-of-cycle (EOC) valve and/or a two-position, normally
closed chilled water end-of-cycle valve. The two-position valve
actuators contain springs that ensures that the wet heat valve is
open and the chilled water valve is closed upon loss of power.
The two-position actuators are driven by the UVC using one
binary output per actuator.
Face and Bypass (F&BP) dampers are used in conjunction with
2 or 3 way End of Cycle (EOC) valves. The UVC is configured for
a face and bypass damper operated by a proportional actuator.
The proportional actuator is driven by the UVC using a 0-10 VDC
output (scaled to 2-6VDC).
When the F&BP damper is used with an EOC valve, the F&BP
damper maintains the DATS. When there is no call for hydronic
heating, the EOC valve will isolate water flow unless there is a
Valve Freeze Protect condition, in which case the valve will go full
open and the F&BP damper will be used to maintain the control
temperature.
Figure 9: Heat State Operation Face & Bypass Heating
Discharge Air
0%
100%
Valve Position
Primary
Capacity
Colder
Satisfied
SatLo
SatHi
Staging
Down
Staging
Up
Auxiliary
Heating
Discharge Air
-EOC Valve Open
0%
100%
F&B
P Damper Position
Primary
Heating
Auxiliary
Heating
Satisfied
Colder
SatLo
SatHi
Staging
Down
Staging
Up
-EOC Valve Closed
Summary of Contents for MicroTech
Page 77: ......