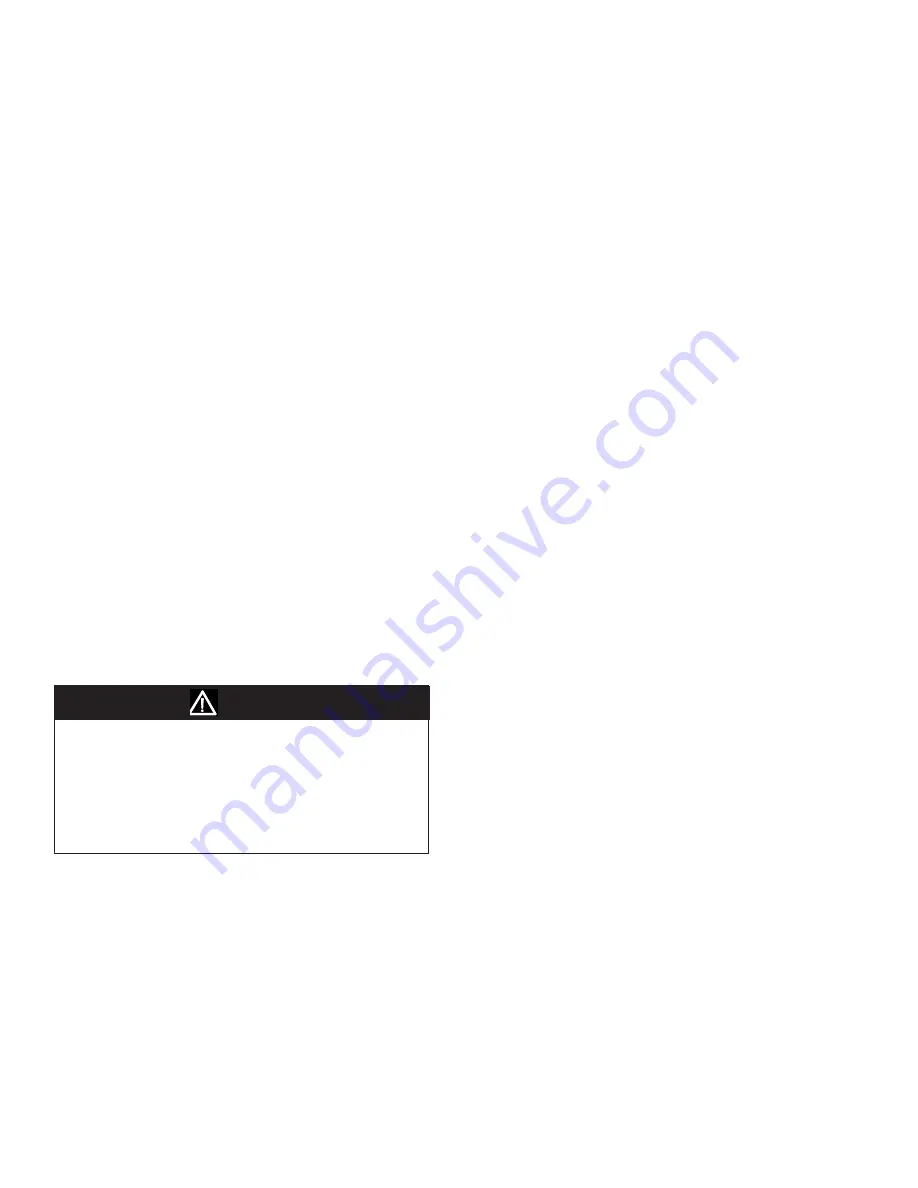
IM 1068-2 / Page 22 of 28
Scheduled Maintenance
Incremental conditioners are built to last. With proper care,
the unit should provide uninterrupted service for many years.
Scheduled maintenance of this equipment, as described
below, is the key to the equipment’s longevity. Air filters must
be cleaned at regular intervals. Twice annually may be ad-
equate in some areas while twice monthly may be required in
others. Areas with high dirt and lint content or heavy usage of
units require more frequent filter maintenance that those areas
of relatively clean operating or low usage conditions. Unit
malfunction may occur if air filters are not kept clean.
The standard filter supplied with the Type K unit is a per-
manent wire mesh type. This type of filter should be rinsed
with hot water and a mild detergent. Let dry and oil lightly to
enhance dust collecting ability.
The Type K is also available with a carbon filter, a zeolite
filter or electrostatic filter. The electrostatic filter is renewable
by rinsing with hot water and replacing in the unit once dry.
The carbon or zeolite filters must be discarded and replaced.
The frequency of this replacement depends on the air quality
of the room being filtered. Rooms with heavy smoke or am-
monia content will require more frequent filter changes than
rooms with minimal degrees of smoke or ammonia.
Note: When replacing the standard filter with an optional
carbon, electrostatic, or zeolite filter, compress the
filter brackets slightly. The optional filters are slightly
thinner than the standard filter and will stay in place
better if the brackets are squeezed slightly.
It is recommended that the chassis be removed every year for
a thorough check-up. The heat section need not be removed
but should be inspected or cleaned if necessary.
Should the heat section blowers or motor need service, the e
tire fan board can be easily removed from the unit for service.
To access the unit for cleaning or service, proceed as follows:
WARNING
Residential and institutional cleaning compounds can cause
permanent damage to the packaged terminal unit. To avoid
damage to unit controls and heat transfer surfaces, do not spray
cleaning compounds onto the return air opening or unit controls.
Normal cleaning can be accomplished by wiping the unit surface
with a damp cloth. When using cleaning compounds on carpets,
floors or walls, turn the unit off to avoid drawing potentially
damaging vapors into the package terminal unit.
1. Disconnect power to the unit.
2. Remove the front panel and the kickplate.
3. Unplug the chassis from the control box and remove the
chassis from the wall sleeve. Replace with spare chassis or
weatherplate.
4. Move chassis to maintenance area and check all seals,
wires, and insulation and repair as required.
5. Cover motor and protect all electrical components before
washing dirt from chassis.
6. Clean condensate drain and clear weep holes.
7. Dry equipment thoroughly, especially electric parts and
insulation.
8. Clean any rust spots with steel wool and paint with rustm
inhibiting paint.
9. Check all fasteners and tighten if necessary.
10. Check the motor nameplate for routine oiling instructions.
11. Test run chassis before reinstalling or returning to spare
parts stock.
Recommended Spare Parts
An advantage of the Incremental system is that failure of
anyone part affects only one Incremental conditioner and
does not interrupt the operation of the rest of the system.
A further advantage is that a failed part can be quickly and
easily replaced, thus minimizing the inoperative time of the
equipment. This is so, however, only if a replacement part is
quickly available. In order to replace a failed part quickly and
keep all Incremental conditioners in good operating condition,
Daikin recommends that at the time Incremental conditioners
are purchased, owners arrange for a small stock of replace-
ment parts.
Where an owner carries such a stock, immediate replacement
of a defective part is possible. The defective part can then be
returned to Daikin or one of its authorized service stations. So
long as it is still in warranty, it is repaired or replaced and re-
turned to the owner without cost for shop labor and material.
Thus, the stock of replacement parts is constantly replenished.
To the right is listed the kind of parts which Daikin recom-
mends be carried in stock, together with the quantity of parts
recommended per 100 Incremental conditioners installed.
Qty. Per
Part Name
100 Units
Cooling Chassis ...................................................................... 1
Compressor Overload Device ................................................. 1
Compressor Running Capacity ............................................... 1
Indoor Fan Motor .................................................................... 1
Outdoor Fan Motor ................................................................. 1
Outdoor Fan Motor Capacitor ................................................. 1
Push button Switch ................................................................. 2
Damper Switch ........................................................................ 2
Thermostat .............................................................................. 2
Knob for Thermostat ............................................................... 6
Control Relay .......................................................................... 2
Damper Motor ......................................................................... 2
Hydronic Valve ....................................................................... 4
Spare Filter ............................................................................ 10
Touch-up Paint (1 Pt. Spray Can) ........................................... 1
For the current spare parts list, and applicable prices, see our
Daikin representative or write:
DaikinMcQuayService, P.O Box 1551, Minneapolis, MN
55440.
Summary of Contents for IM 1068-2
Page 26: ...IM 1068 2 Page 26 of 28 ...
Page 27: ...IM 1068 2 Page 27 of 28 ...