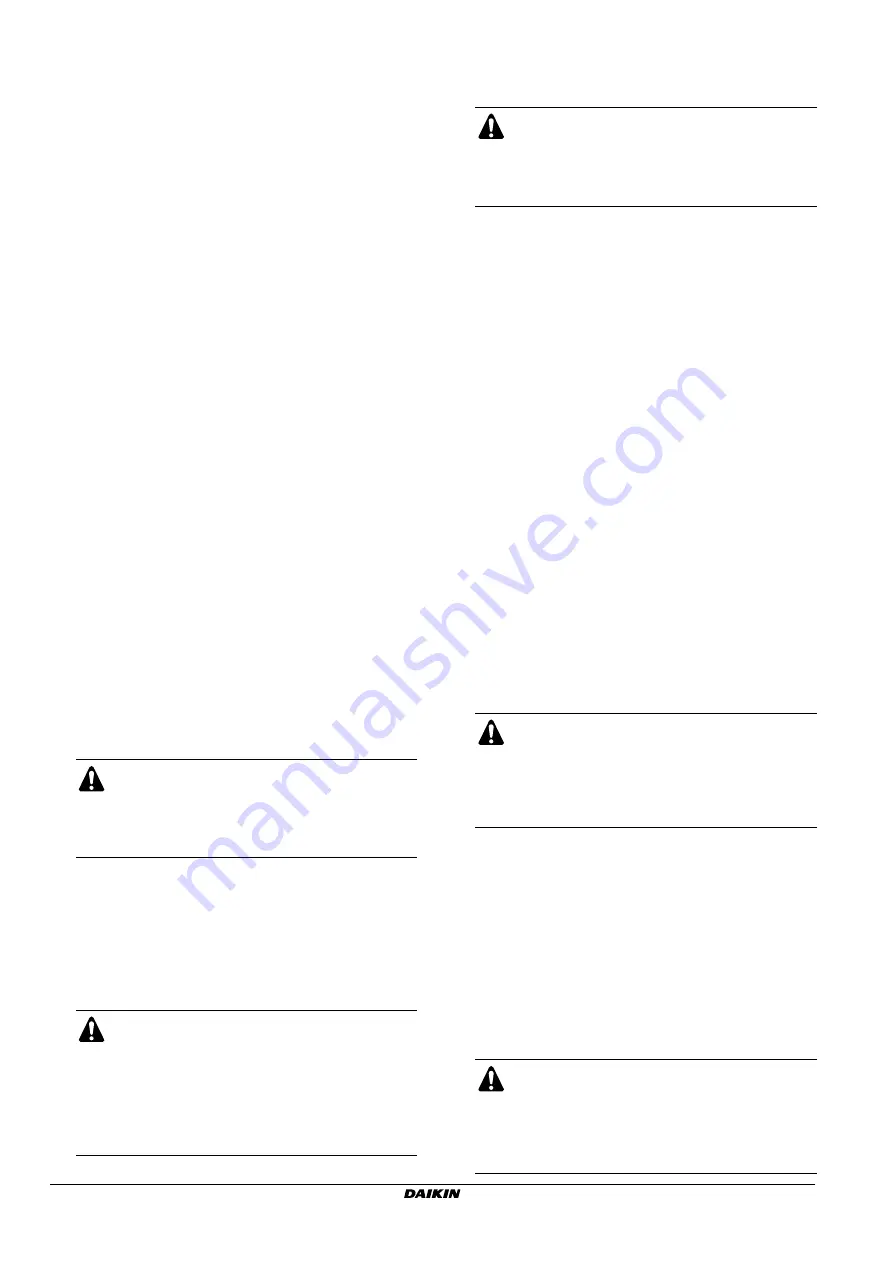
Installation and operation manual
6
EWWD440~850AAYNNO**
Packaged water-cooled water chillers
4PW25558-1B
As the refrigerant circulates through the unit, changes in its state or
condition occur. These changes are caused by the following main
components:
■
Compressor
The compressor (M*C) acts as a pump and circulates the
refrigerant in the refrigeration circuit. It compresses the refri-
gerant vapour coming from the evaporator at the pressure at
which it can easily be liquefied in the condenser.
■
Condenser
The function of the condenser is to change the state of the
refrigerant from gaseous to liquid. The heat gained by the gas in
the evaporator is discharged through the condenser to the
water, and the vapour condenses to liquid.
■
Filter/drier
The filter installed behind the condenser removes small particles
from the refrigerant to prevent blockage of the tubes.
The drier takes water out of the system.
■
Expansion valve
The liquid refrigerant coming from the condenser enters the
evaporator via an expansion valve. The expansion valve brings
the liquid refrigerant to a pressure at which it can easily be
evaporated in the evaporator.
■
Evaporator
The main function of the evaporator is to take heat from the
water that flows through it. This is done by turning the liquid
refrigerant, coming from the condenser, into gaseous
refrigerant.
■
Water in/outlet connection
The water inlet and outlet connection allow an easy connection
of the unit to the water circuit of the air handling unit or industrial
equipment.
I
NSTALLATION
Selection of installation site and foundation work
■
This is a class A product. In a domestic environment this product
may cause radio interference in which case the user may be
required to take adequate measures.
■
Indoor installation: This is an indoor-only model
Do not install this product at places subject to effect of weather
and places exposed to water splash.
Do not install this product at places exposed to direct sunlight.
■
Well-ventilated installation sites
Set up a ventilation facility so that the leakage of refrigerant
does not lead to oxygen deficiency.
Even in case the capacity of the machine room is big enough to
the extent that leakage of refrigerant does not lead to critical
concentration in terms of volumes, depending on the density
characteristics of the refrigerant gas, places with high
concentration may form locally and oxygen deficiency accidents
may result.
■
An atmosphere with flammable gas is not allowed.
Because this product is not explosion-proof, do not install this
product at places in atmospheres with flammable gas or places
with risk of leakage of flammable gas.
■
Avoid installing this product at high temperature or low
temperature places and at places with high humidity.
Avoid installing this product where the temperature exceeds
35°C or temperature only reaches 0°C or less.
Avoid installing this product at places with relative humidity of
90% or more.
Mounting this product at places where the temperature variation
per hour exceeds 8°C or more is also inappropriate.
If you use this product in cold climates, consideration must be
given not only to the unit but also to freezing of chilled and
cooling water facilities.
■
Do not install this product near a flame
As a rule, install this product in a separate room away from
flame facilities including boilers, etc.
When you install this product in the same room where a boiler is
placed, restriction may arise on the installation conditions.
Therefore, please consult with the responsibles of competent
public agencies before doing so.
■
Special atmosphere is not allowed
Do not install the unit in atmospheres that attack metal, electric
parts, etc.
Be careful with the installation site of the cooling tower so that
the cooling water does not become highly corrosive.
If installed in the vicinity of contaminated rivers, seaside, plating
plant and chemical plant, or main roads, take care to protect the
cooling tower from inhaling harmful gases directly and increase
the frequency of water examination.
Do not install this product near ammonia facilities, exhaust ports
of toilets or exhaust ports of operating rooms of hospitals,
sewage treatment facilities, etc.
Gas leakage accident due to corrosion of heat exchanger tubes
of the condenser may result.
■
Avoid installing this product in places where sound or vibration
can present problems.
Select a place where operating sound or vibration does not
present possible problems.
In response to such conditions, take proper measures for
vibration isolation and sound insulation.
Vibration may propagate from the installation and produce
sound from floor or wall.
In living areas, special attention is required when you install the
unit in upper stories of a building.
■
Fix the unit with bolts on a flat place that bears the weight of the
unit sufficiently.
Set the unit on a solid and level foundation (the levelness should
be
≤
2 mm/1000 m).
WARNING
Install this product indoors
Do not install this product at places exposed to water
drop or subject to water splash.
Electric leak or electric shock may result.
CAUTION
Take measures against refrigerant leakage
■
Take measures so that the critical concentration
is not exceeded when a leakage of refrigerant
takes place.
■
Exceeding the critical concentration due to
leakage of refrigerant may lead to oxygen
deficiency accidents.
CAUTION
Do not install this product at places with risk of
leakage of flammable gas.
Accumulation of flammable gas around the unit due to
leakage of flammable gas may lead to ignition.
CAUTION
Do not install the unit in special atmospheres
Do not install this product in hot spring resorts,
seaside areas, oily places or atmosphere with
corrosive gases including ammonia. Electric shock or
fire due to corrosion may result.
WARNING
Fix the product correctly with anchor bolts on a
flat foundation that bears the weight of the unit.
Insufficient strength of the foundation and insufficient
fixing may result in water leakage or a roll-over
accident.