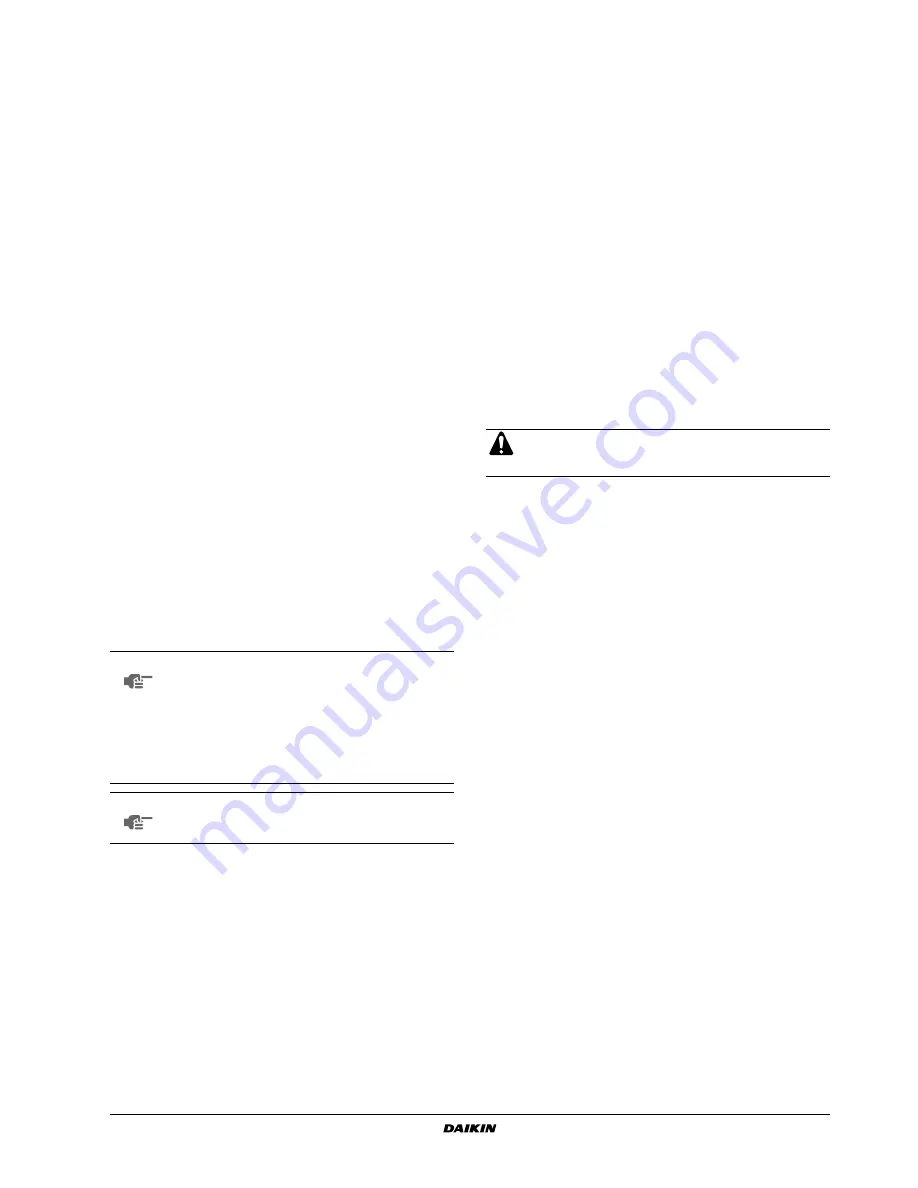
ERAP110~170MBYNN
Air-cooled condensing units
4PW22680-1E
Installation manual
4
4
After completion of procedure step 3, perform an “initial start”
test:
4.1 Start the compressor and wait for the compressor to go through
the star/delta.
Carefully check during start-up:
■
that compressor is not producing any abnormal noise or
vibration;
■
that high pressure rises and low pressure drops within 10
seconds after start to evaluate if the compressor is not
operating in reverse due to wrong wiring;
■
that no safeties are activated.
4.2 Stop the compressor after 10 seconds.
Fine-tuning of refrigerant charge while unit is in operation
5
Use the 3/8” valve on the suction side of the compressor for fine-
tuning of the refrigerant charge and make sure to charge the
refrigerant in its liquid state.
5.1 For fine-tuning of the refrigerant charge, the compressor must
operate at full load (100%).
5.2 Verify the superheat and subcooling:
■
superheat must be between 3 and 8 K
■
subcooling must be between 3 and 8 K
5.3 Verify the oil sightglass. Level must be within the sightglass.
5.4 Verify the liquid-line sightglass. It should be sealed and not
indicate moisture in the refrigerant.
5.5 As long as the liquid-line sightglass is not sealed, add refrigerant
in steps of 1 kg and wait until the unit runs in stable conditions.
Repeat the complete procedure step 5 until the liquid-line
sightglass is sealed.
The unit must have the time to stabelize which means that this
charging has to be done in a smooth way.
6
Note down the superheat and subcooling for future reference.
7
Fill out the total refrigerant charge on the unit nameplate and on
the refrigerant charge label supplied with the product.
F
IELD
WIRING
Parts table
F1,2,3U .................. Main fuses for the unit
H1P ........................ Indication lamp general operation
H2P ........................ Indication lamp alarm
H3P ........................ Indication lamp operation circuit
L1,2,3 ..................... Main terminals
PE .......................... Main earth terminal
S6S ........................ Changeable input 1
S9L......................... Contact that closes if the fan or pump is working
S10S ...................... Changeable input 2
S11S ...................... Changeable input 3
S12S ...................... Changeable input 4
S13S ...................... Main isolator switch
- - - ......................... Field wiring
Power circuit and cable requirements
1
The electrical power supply to the unit should be arranged so
that it can be switched on or off independently of the electrical
supply to other items of the plant and equipment in general.
2
A power circuit must be provided for connection of the unit. This
circuit must be protected with the required safety devices, i.e. a
circuit breaker, a slow blow fuse on each phase and an earth
leak detector. Recommended fuses are mentioned on the wiring
diagram supplied with the unit.
Connection of the air-cooled condensing unit power supply
1
Using the appropriate cable, connect the power circuit to the L1,
L2 and L3 terminals of the unit.
In case the option "main isolator switch" is installed on the unit,
the power circuit must be connected to the terminals 2, 4 and 6
of the main isolator switch.
2
Connect the earth conductor (yellow/green) to the earthing
terminal PE.
Installation of the thermostat sensor (R4T)
The thermostat sensor is provided with a cable length of 12 m and
can be found rolled up in the switchbox.
■
In case of a water cooled evaporator, this sensor can be
mounted in a sensor holder on the evaporator.
■
In case of an air handling unit, this sensor can be mounted in a
sensor holder in the air cooled evaporator water circuit.
Refer also to
"Annex I" on page 7
for unit setup examples.
Interconnection cables
■
Be sure to interlock so, that the compressor will not come into
operation unless the fan is operated. For this purpose 2 spare
terminals are provided in the switch box. Refer to the wiring
diagram supplied with the unit.
■
Voltage free contacts
The controller is provided with some voltage free contacts to
indicate the status of the unit. These voltage free contacts can
be wired as described on the wiring diagram. The maximum
allowable current is 4 A.
■
Remote inputs
Besides the voltage free contacts, there are also possibilities to install
remote inputs. They can be installed as shown on the wiring diagram.
Cable for remote digital controller
(See remote digital
controller in the operation manual)
1
A remote digital controller can be connected to the PCB inside
the unit by means of a 6-ray cable and a connector located on
the rear side of the remote digital controller in case you prefer to
operate the unit from a distance. You are allowed to use a cable
of up
to 600 metres.
Specifications of the cable: 6-ray telephone
cable with a maximum cable resistance of 0.1
Ω
/m.
NOTE
All field wiring and components must be installed by a
licensed electrician and must comply with relevant
European and national regulations.
The field wiring must be carried out in accordance with
the wiring diagram supplied with the unit and the
instructions given below.
Be sure to use a dedicated power circuit. Never use a
power supply shared by another appliance.
NOTE
Verify on the wiring diagram all electrical actions
mentioned above, in order to understand the operation
of the unit more deeply.
Switch off the main isolator switch before making any
connections (switch off the circuit breaker, remove or
switch off the fuses).