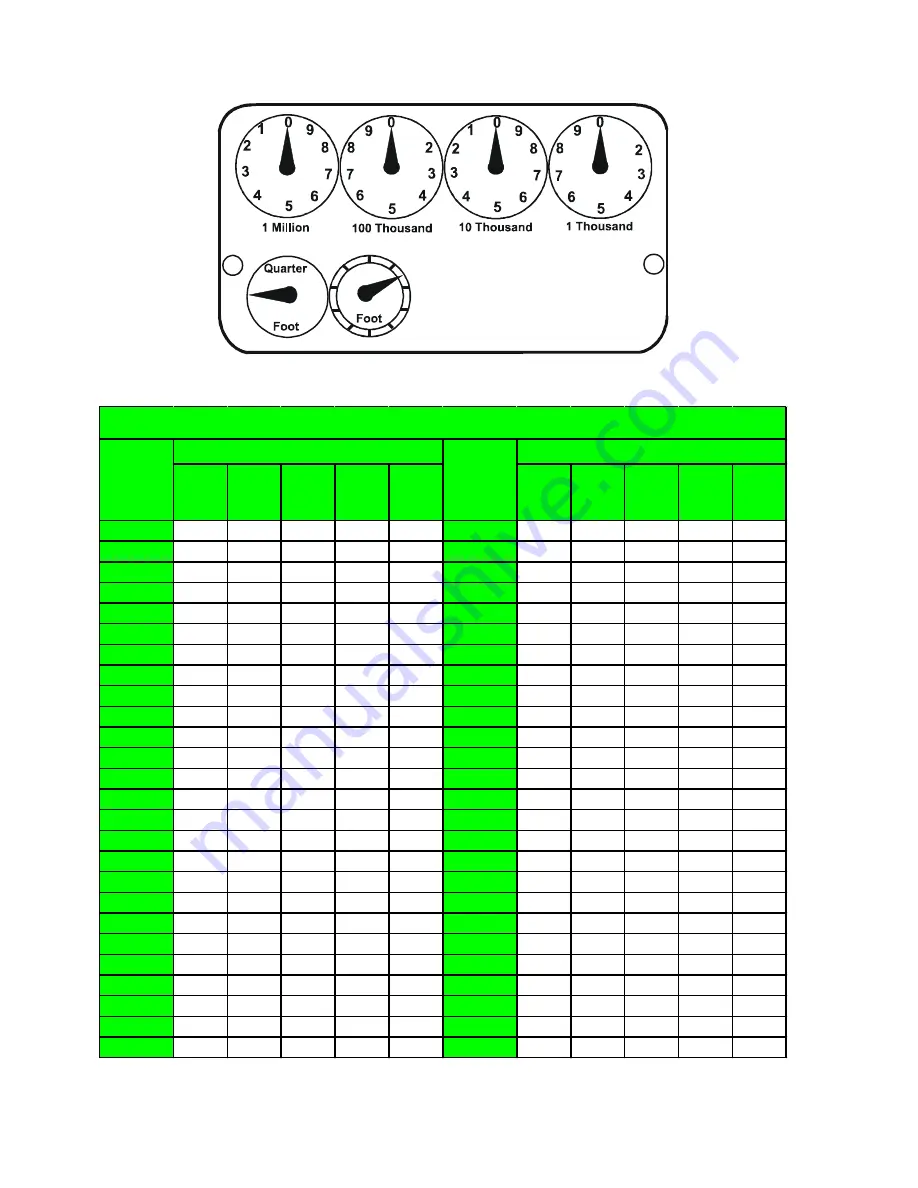
36
SERVICING
CUBIC
FEET
1
1
One
1/4
cu/ft
1/2
cu/ft
1
cu/ft
2
cu/ft
5
cu/ft
1/4
cu/ft
1/2
cu/ft
1
cu/ft
2
cu/ft
5
cu/ft
10
90
180
360
720
1800
36
25
50
100
200
500
11
82
164
327
655
1636
37
--
--
97
195
486
12
75
150
300
600
1500
38
23
47
95
189
474
13
69
138
277
555
1385
39
--
--
92
185
462
14
64
129
257
514
1286
40
22
45
90
180
450
15
60
120
240
480
1200
41
--
--
--
176
439
16
56
113
225
450
1125
42
21
43
86
172
429
17
53
106
212
424
1059
43
--
--
--
167
419
18
50
100
200
400
1000
44
--
41
82
164
409
19
47
95
189
379
947
45
20
40
80
160
400
20
45
90
180
360
900
46
--
--
78
157
391
21
43
86
171
343
857
47
19
38
76
153
383
22
41
82
164
327
818
48
--
--
75
150
375
23
39
78
157
313
783
49
--
--
--
147
367
24
37
75
150
300
750
50
18
36
72
144
360
25
36
72
144
288
720
51
--
--
--
141
355
26
34
69
138
277
692
52
--
--
69
138
346
27
33
67
133
265
667
53
17
34
--
136
340
28
32
64
129
257
643
54
--
--
67
133
333
29
31
62
124
248
621
55
--
--
--
131
327
30
30
60
120
240
600
56
16
32
64
129
321
31
--
--
116
232
581
57
--
--
--
126
316
32
28
56
113
225
563
58
--
31
62
124
310
33
--
--
109
218
545
59
--
--
--
122
305
34
26
53
106
212
529
60
15
30
60
120
300
35
--
--
103
206
514
GAS RATE -- CUBIC FEET PER HOUR
Seconds
for One
Revolutio
n
Size of Test Dial
Seconds
for One
Revolutio
n
Size of Test Dial