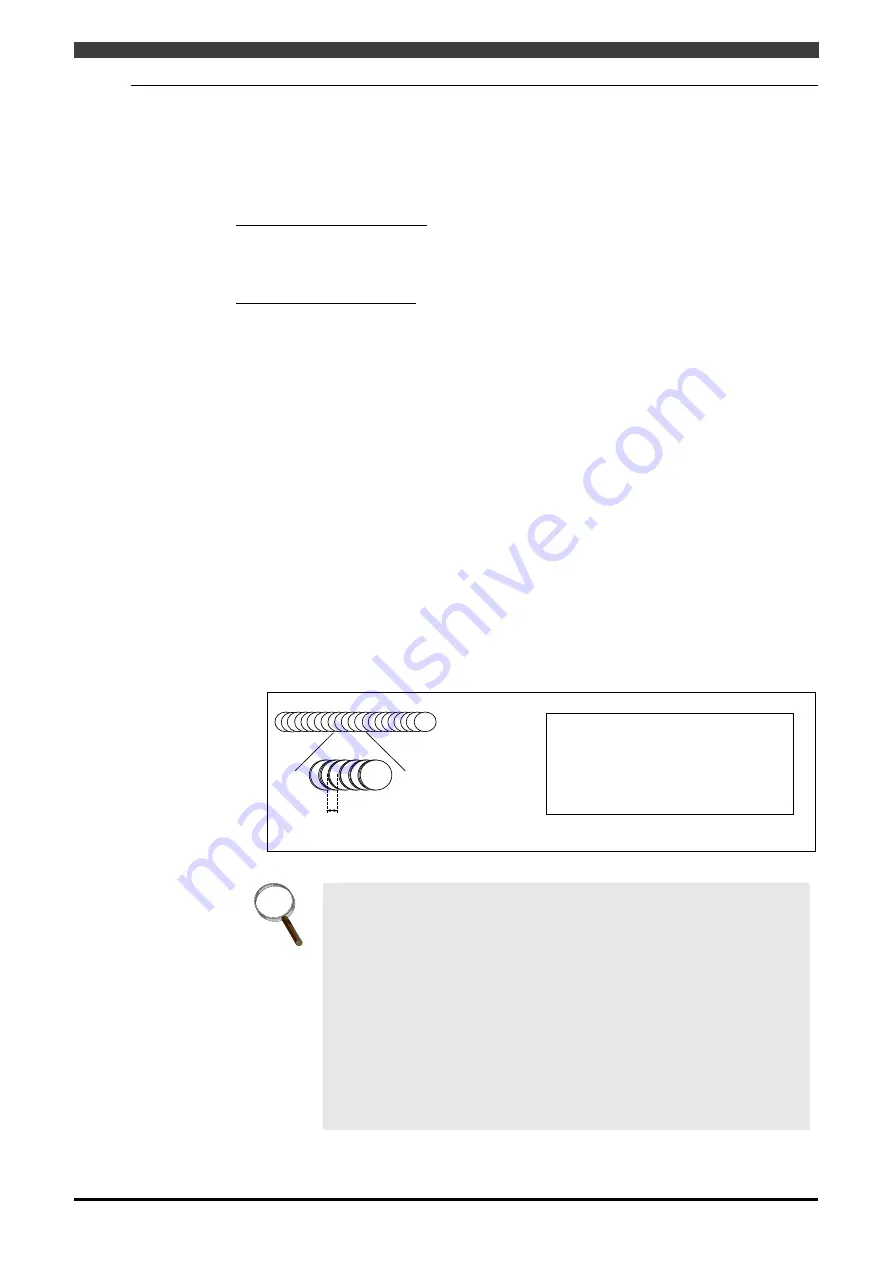
3.10 Welding conditions of WB-P350/P400
3-33
3.10.3 To adjust the pulse conditions
Generally, to adjust the pulse conditions, the following two parameters are the only ones that need
to be changed.
• Arc characteristic ... For hardening or softening the condition of the arc.
• Wave frequency ... For adjusting the ripple pitch of the beads shaped like fish scales.
What are the arc characteristic?
The arc characteristic is a parameter used for internally, adjusting the pulse rise time and
pulse fall time. When its value is increased, an expansive soft arc is obtained; conversely,
when it is reduced, a concentrated hard arc is obtained.
What is the wave frequency?
For the wave pulsed welding method periodical changes of the wire feed speed and the unit
pulse condition can be made in low frequencies. Furthermore, synchronizing this periodic
cycle, then the deposition rate can be increased / decreased and the vibrations of the molten
pool can be made.
For aluminum alloy welding, beads shaped like fish scales can be formed. This welding
improves the ability to counter gaps that may exist in the welded areas. Furthermore, grain
size can be minimized by the stirring effect, caused by the molten pool vibration, and tolerance
of welding cracks will also be improved.
For steel and stainless welding, the melted metal takes time to solidify. Therefore, in this
welding, there are cases where clear beads, shaped like fish scales, cannot be formulated,
because the metal flows before it can solidify. However, the blowhole can be reduced by the
stirring effect caused by the molten pool vibrations.
The wave pulsed welding method will change the wire feed speed, unit pulse conditions, etc.
However, for changes of the wire feed speed, if the wire feed motor’s response characteristic
comes close to a limiting value, the feed amplitude will automatically be reduced. If the wave
frequency is over 3 Hz, the speed of the wire feed will gradually be reduced. If it exceeds over
5 Hz the amplitude will run out. In this case, the wire feed speed with stabilize and only the unit
pulse condition will change.
For aluminum alloy welding where the beads can be formed in shapes of fish scales, it is
possible to adjust the ripple pitches freely, depending on the combinations between the
welding speed and wave frequency.
The width of the pitches will become narrow if the wave frequencies are expanded without
changing the welding speed. Vise versa, if the frequencies are made smaller with the welding
speed unchanged, the pitches will widen.
Bead
Detail
The ripple pitch
The beads shaped like fish scales can
be adjusted using the wave frequency.
During automatic operation a fixed
interval is maintained, but the ripple pitch
interval may be disrupted by temporary
stop and restart thereafter.
Fig 3.10.1 Adjustment of beads shaped like fish scales using wave frequency
INFO.
•
In some cases, ripple patterns of the welded beads may not be precisely
visible depending on the type of material used, welding speed and the heat
input during welding. Especially, the patterns of welding materials such as
the SUS, a mild steel that takes time to harden, cannot be seen unlike the
welded beads of aluminum alloy welding.
•
There is a major relationship between the reduction of blowholes and the
measure of the melted metal’s vibration. The bigger the extent of the molten
pool, the bigger the vibrations as well; reducing more blowholes. On the
contrary, if the molten pool is small, then fewer blowholes will be eliminated.
If thicker beads are used for welding, the effects are bigger. However,
blowholes should not be taken away from all of the welding materials such
as extremely thick coated or oil-based steel products and cast materials.
•
If short-circuit occurs frequently while welding using soft aluminum, the
overview of the bead could appear black.
Summary of Contents for OTC Almega AX Series
Page 10: ......
Page 69: ...1 4 Welding mode lists 1 59...