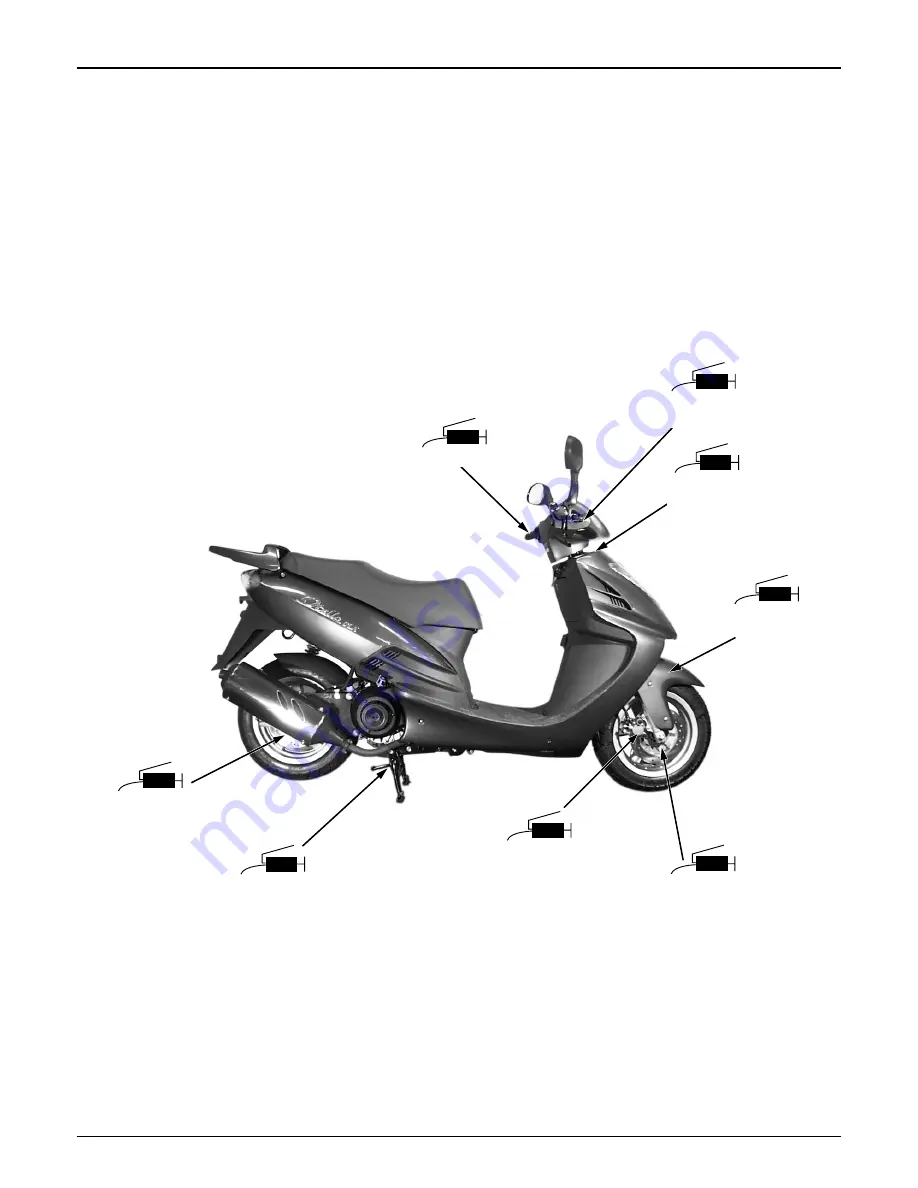
Lubrication
2-9
Lubrication Points
Unless specifically designated, use general grease to
lubricate the lubrication points. For sliding parts
not shown here, add oil or grease.
Control Cable Lubrication
Remove and clean the upper assembly of the throttle
cable, and apply oil. If the cable has expanded,
replace it.
Wheel
bearing
Side/main stand pivot
Brake caliper
bracket
Wheel bearing
/speedometer gear
Front fork
dust seal
grease
grease
grease
grease
grease
grease
grease
grease
Front brake
lever pivot
Setting head
bearing
Throttle grip
Summary of Contents for NS125DLX
Page 1: ...SERVICE MANUAL...
Page 4: ...Service Information 1 2 Identification Numbers Frame serial number Engine serial number...
Page 22: ...MEMO...
Page 43: ...MEMO...
Page 44: ...Fuel System 5 0 Fuel tank Fuel strainer Fuel pump Carburetor...
Page 54: ...MEMO...
Page 58: ...L Crank Case Cover Kick Starter Continuously Variable Transmission 7 0 L crank case cover...
Page 76: ...Generator Starter Clutch 8 0...
Page 107: ...MEMO...
Page 108: ...Transmission Crankshaft Crank Case 11 0 R Crank Case Crankshaft L Crank Case...
Page 154: ...MEMO...
Page 168: ...MEMO...
Page 172: ...MEMO...
Page 180: ...MEMO...
Page 182: ...MEMO...
Page 190: ...2001 4 PRINTED 2001 4 PUBLICATION SERVICE MANUAL NO COPY...