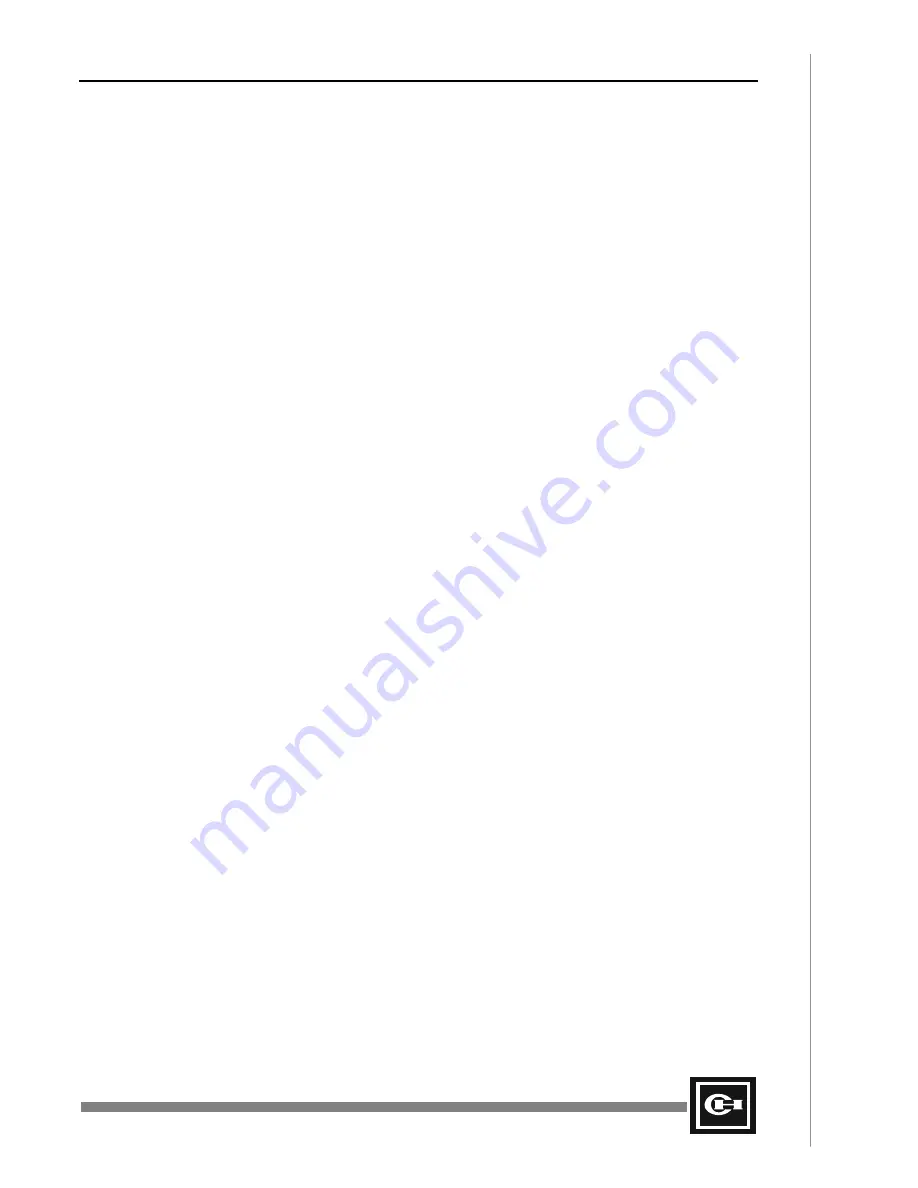
225
Ladder Program
The final step in setting up the example PID loop control application is programming the PLC. The
following ladder was generated for the D320 using the Cutler-Hammer GPC5 Programming Software.
Initialization of the PID loop parameters occur in the first scan of the program after power-on or a stop
to start transition. This is accomplished through the use of the special “First Scan On” contact F1.0.
During every consecutive scan, the analog input value (which comes in through I/O register R7) is
stored in the PV register (W1602), while the CV register (W1604) is sent out to the analog output (I/O
register R3).
To observe the operation of the PID loop control, simply monitor the PID register block W1600 to
W1631, paying special attention to the interaction of the PV, SP, and CV. Changing the SP value will
cause the PID loop to recalculate on a continuous basis the necessary CV to achieve the desired PV.
Modification of the Proportional, Integral, and Derivative terms will modify the reaction speed and
stability of the PID process.
Summary of Contents for D320 PLC
Page 1: ...D320 PLC User s Manual...
Page 18: ...6 D320 PLC User s Manual...
Page 28: ...16 D320 PLC User s Manual...
Page 34: ...22 D320 PLC User s Manual...
Page 78: ...66 D320 PLC User s Manual...
Page 176: ...164 D320 PLC User s Manual...
Page 210: ...198 D320 PLC User s Manual...
Page 258: ...246 D320 PLC User s Manual...