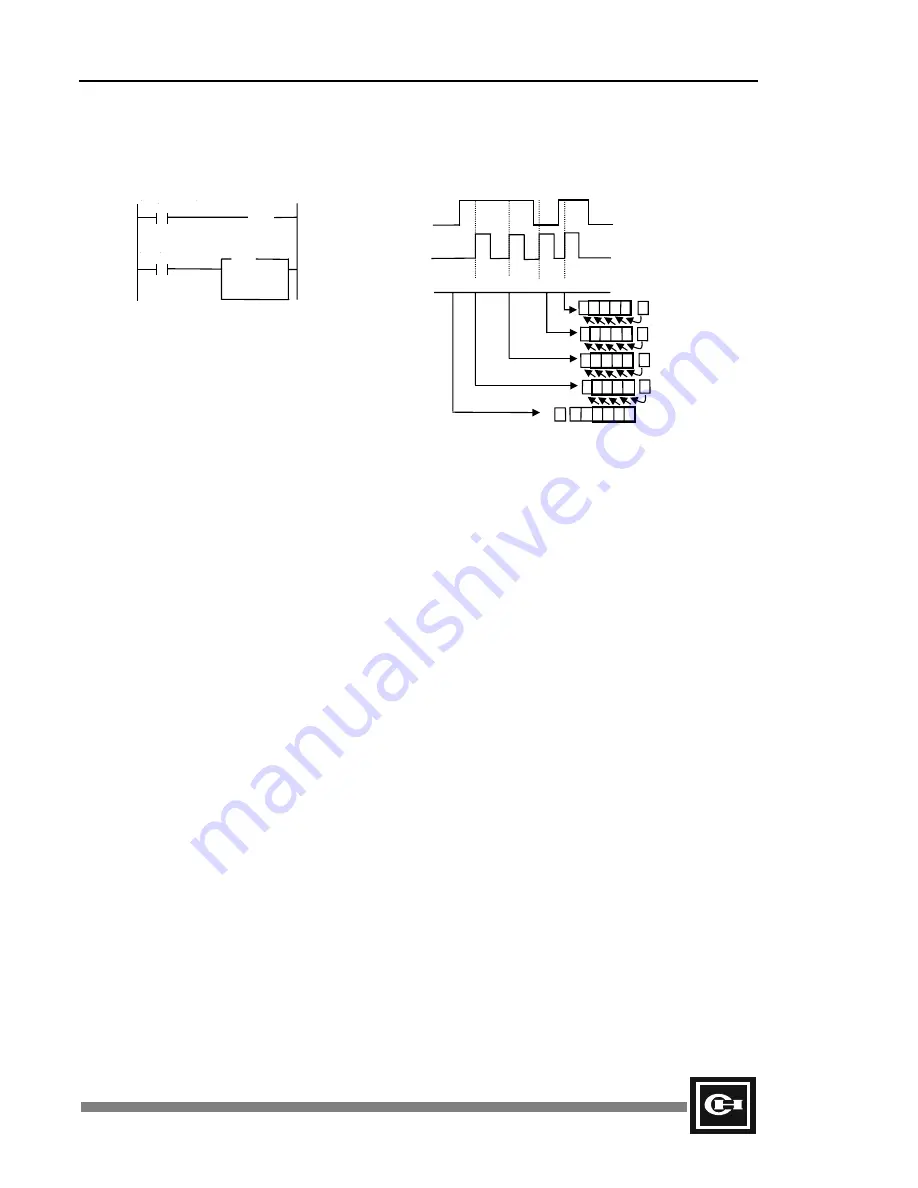
Chapter 6: Instructions
119
Example
Program Expression
Operation Results
If N = 1, the bits shift by one, and the LSB is always
input from F1.8.
If N = 2, the bits shift by two. The bits are shifted one
position, and the first data input to the LSB is F1.8.
The original MSB is stored in F1.8. The bits are
again shifted one position, with the LSB being set by
the new F1.8, and F1.8 being changed to the state of
the last MSB.
R0.0
R
R0.1
R
ROL
D =MO
N = 1
F1.8
(OUT)
M0 $00 $01 $03 $06 $0D
(word)
… 1 1 0 1 1 C
… 0 1 1 0 0 C
… 0 0 1 1 1 C
… 0 0 0 1 1 C
C 0 0 … 0 0 0 0
R0.0
R0.1
Summary of Contents for D320 PLC
Page 1: ...D320 PLC User s Manual...
Page 18: ...6 D320 PLC User s Manual...
Page 28: ...16 D320 PLC User s Manual...
Page 34: ...22 D320 PLC User s Manual...
Page 78: ...66 D320 PLC User s Manual...
Page 176: ...164 D320 PLC User s Manual...
Page 210: ...198 D320 PLC User s Manual...
Page 258: ...246 D320 PLC User s Manual...