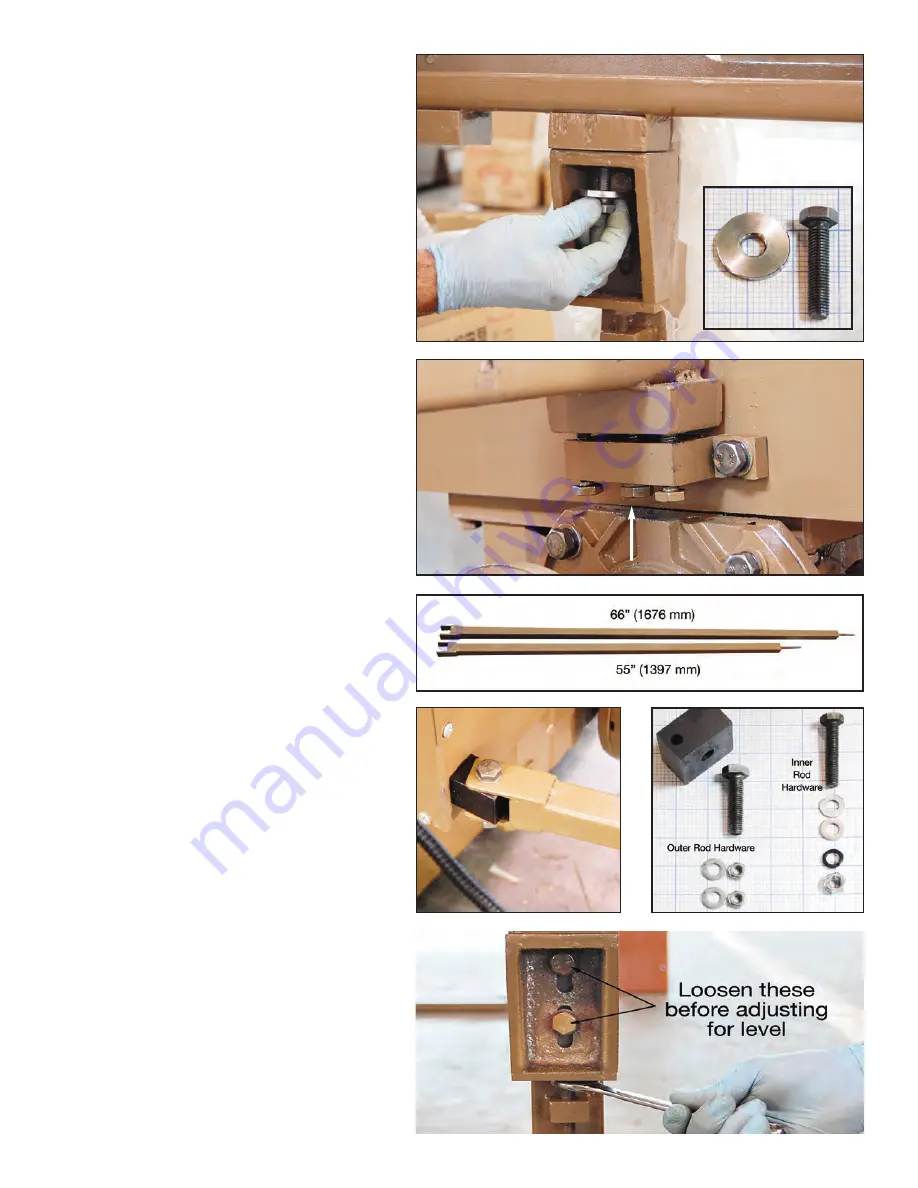
The
outgoing
, inner conveyor bolt is in
the block on the machine. It can’t be
removed due to interference with the
motor and transmission flange. Figure H.
Fit the outgoing conveyor just as you did
the ingoing side.
The Pull Rods that keep the conveyors
aligned are unequal lengths.
• Ingoing (R) side rod is 66” (1676 mm)
• Outgoing (L) side rod is 55” (1397 mm)
Fit the rods with the hardware and
blocks shown in Figures J and K. Before
tightening the rods, be sure the conveyors
are perpendicular to the machine so
glass will run straight into and out of the
machine.
Level the conveyors with the outer bolts
as shown in figure L. Also see Figure 10
in the manual. Now the Pull Rods can be
hand tightened.
Install the timing belts over the outer
pulleys and adjust the tension as shown
in Figure M (next page). Be sure the belt
is centered in the pulley and not riding
on the edge. The belt should be tight
enough that it is flat along the top run.
About 1/2” (13mm) of clearance at the
center of the belt run is normal. Figure N
(next page). Tighten the axle nuts on the
outside pulleys. Figure M
The wooden conveyor covers can be
refitted now. Use the black Allen socket
head bolts.
Figure F
Figure H
Figure G
Figure J
Figure K
Figure L
Pull Rods