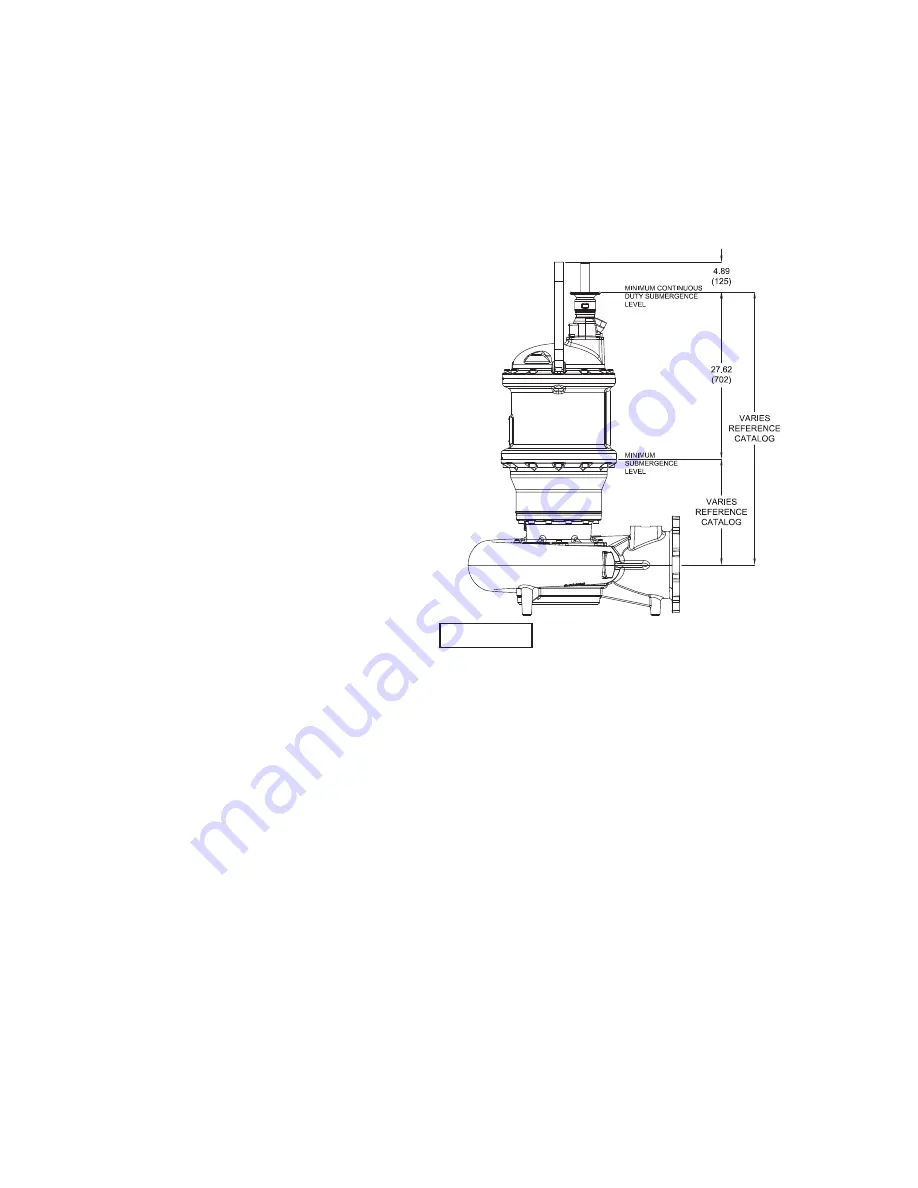
4
SECTION A: GENERAL INFORMATION
A-1) To the Purchaser:
Congratulations! You are the owner of one of the finest pumps
on the market today. CP&S pumps are products engineered
and manufactured of high quality components. Over one
hundred years of pump building experience along with a
continuing quality assurance program combine to produce
a pump which will stand up to the toughest applications.
This manual will provide helpful information concerning
installation, maintenance, and proper service guidelines.
A-2) Receiving:
Upon receiving the pump, it should be inspected for
damage or shortages. If damage has occurred, file a
claim immediately with the company that delivered the
pump.
MAKE CERTAIN TO RETAIN THIS MANUAL!
A-3) Storage:
Short Term-
CP&S Pumps are manufactured for efficient
performance following short inoperative periods in storage.
For best results, pumps can be retained in storage, as factory
assembled, in a dry atmosphere with constant temperatures
for up to six (6) months.
Long Term
- Any length of time exceeding six (6) months,
but not more than twenty-four (24) months. The unit should
be stored in a temperature controlled area, a roofed over
walled enclosure that provides protection from the elements
(rain, snow, wind-blown dust, etc.), and whose temperature
can be maintained b40 deg. F and +120 deg. F.
(4.4 - 49°C). Pump should be stored in its original shipping
container. On initial start up, rotate impeller by hand to
assure seal and impeller rotate freely. If it is required that
the pump be installed and tested before the long term
storage begins, such installation will be allowed provided:
1.) The pump is not installed under water for more than
one (1) month.
2.) Immediately upon satisfactory completion of the test,
the pump is removed, thoroughly dried, repacked in the
original shipping container, and placed in a temperature
controlled storage area.
A-4) Service Centers:
For the location of the nearest Deming Service Center,
contact Crane Pumps & Systems, Inc., Service Department
in Piqua, Ohio, telephone (937) 778-8947 or Crane Pumps
& Systems Canada, in Brampton, Ontario, (905) 457-6223.
SECTION B: INSTALLATION
B-1) Location:
These self-contained pumping units are recommended for
use in a sump, lift station or basin. This pump is designed
for submerged continuous duty (15 minutes duty in air
at nameplate horsepower), pumping sewage, effluent,
wastewater or other nonexplosive or noncorrosive liquids
not above 104°F (40°C). Never install the pump in a trench,
ditch or hole with a dirt bottom; the legs will sink into the dirt
and the suction will become plugged.
B-1.1) Submergence:
It is recommended that the pump be operated at the
minimum continuous duty submerged condition (See Fig. 1).
The time required to draw the well down from top of motor
to the minimum submergence level should not be greater
than 15 minutes.
NOTE:
Outer shaft seal must be in liquid
when motor is operated, whether motor is submerged or in
air.
B-2) Discharge:
Discharge piping should be as short as possible. Both a
check valve and a shut-off valve are recommended for
each pump being used. The check valve is used to prevent
backflow into the sump. Excessive backflow can cause
flooding and/or damage to the pump. The shut-off valve
is used to stop system flow during pump or check valve
servicing.
Crane Pumps & Systems manufactures a break away
fitting discharge system designed to allow the submersible
wastewater pump to be installed or removed without
requiring personnel to enter the wet well. Place the Break
Away Fitting (BAF) in position. Temporarily secure the
guide rails in the upper mounting brackets and locate the
base elbow on the bottom of the wet well. Level the base
elbow with grout and/or shims. Install the intermediate
support brackets, if required. Make sure the rails are in
a true vertical position so the pump will clear the access
opening and will slide freely down the rails into place on
the discharge base elbow. Once the rails are in proper
alignment, bolt the base elbow into the floor of the station
and connect the discharge pipe to the elbow. Connect the
movable portion and other supplied fittings of the BAF onto
the pump and lower into wet well. See the Break Away
Fitting manual for more information.
FIGURE 1
Summary of Contents for DEMING 7365N-X54-95-30N
Page 18: ...18 FIGURE 9 Vortex Enclosed CROSS SECTIONS FIGURE 10 ...
Page 19: ...19 EXPLODED VIEWS FIGURE 11 ...
Page 22: ...22 Notes ...