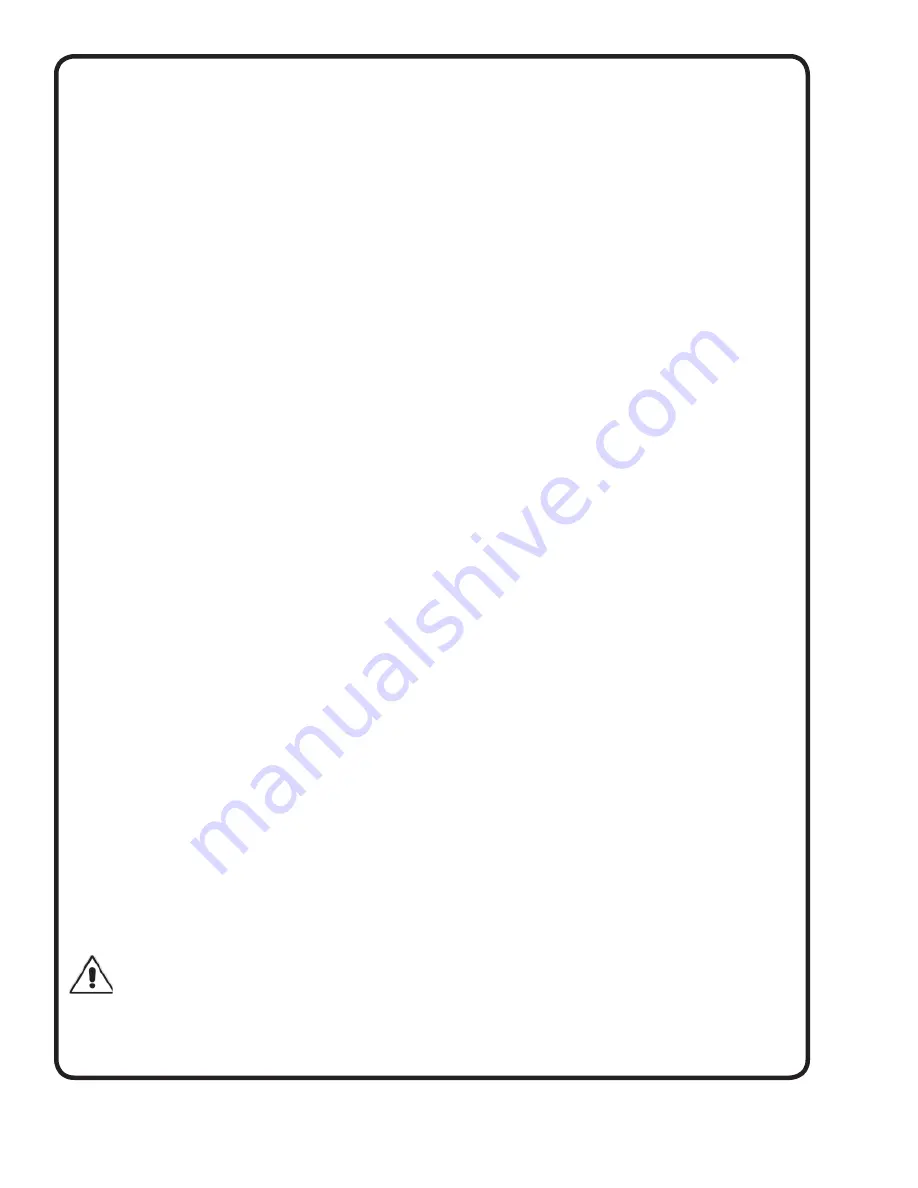
8
A pump operating under a suction lift may be primed by
any of the following methods, as may be best suited to the
conditions. The discharge valve should be closed during
priming operation.
Priming by Ejector or Exhauster
This method is used when steam, high pressure water, or
compressed air is available.
1. Attach an air ejector to the highest point in the pump
casing. This will remove the air from the pump and
suction
line.
2. As soon as the ejector waste pipe throws water
continuously, the pump may be started. After starting, a
steady stream of water from the waste pipe indicates
the pump is primed. If this stream of water is not
obtained, the pump must be stopped at once and the
process of priming repeated. A foot valve is unnecessary
when this kind of device is used.
3. Open the discharge valve slowly and close off the
ejector.
Priming With Foot Valve
When it is not practicable to prime by ejector or exhauster,
the pump may be primed by the use of a foot valve. The foot
valve will prevent liquid running out through the suction inlet
and the pump can be completely fi lled with liquid from some
outside source. Pet cocks on the top of the pump should
be opened during fi lling to allow the air to escape. A tight
foot valve will keep the pump constantly primed so that the
pump may be used for automatic operation. The valve must
be inspected frequently, however, to see that it does not
develop leaks and thus allow the pump to be started dry.
Priming by Vacuum Pump
When neither of the above methods of priming are practical,
the pump may be primed by the use of a vacuum pump to
exhaust the air from the pump casing and suction line. A wet
vacuum pump is preferable, as it will not be injured if water
enters it. When a dry vacuum pump is used, the installation
must be such as to prevent liquid being taken into the air
pump. The vacuum pump manufacturer’s instructions
should be followed.
2. STARTING THE PUMP
Position of Discharge Valve on Starting
A high or medium head centrifugal pump, when primed
and operated at full speed with the discharge gate valve
closed, requires much less power than when operated at
its rated capacity and head with the discharge gate valve
open. For this reason it is usually advantageous to have
the discharge gate valve closed when the pump is being
started. The pump must not be throttled by the use of a
valve in the suction line.
WARNING! - Operating the pump with a closed
discharge valve can result in excessive heat
build-up and should be limited to the shortest
practical duration. Operating the pump at close
to shut-off head usually places greater bending strains
on the shaft than at operating points near the best
effi ciency.
The following important items should be checked as pump
is started and placed in operation.
a. Pump and driver securely bolted
b. Coupling properly aligned
c. Piping complete
d. Correct pump rotation
e. Pump shaft turns freely
f. Discharge valve closed
g. Suction valve open (if used)
h. Coupling Guard installed
i. Pump fully primed
j. Pump and driver properly lubricated
k. Seal water valve (if used) open
Only after these items have been checked should the
pump be started.
3. INITIAL ADJUSTMENTS
Open discharge valve as soon as operating speed has
been reached. After the pump has been started the
packing box glands should be tightened to eliminate
excessive liquid loss. (Applies only to pumps having
packed stuffi ng boxes.) Packing should not be pressed
too tight, as this may result in burning the packing and
scoring the shaft or shaft sleeve. The best adjustment will
allow the liquid to drip slowly from the packing box gland.
This will permit proper lubrication of the shaft and dissipate
generated heat.
As soon as the pump and driver have reached the normal
operating temperature, the unit should be shut down for
fi nal coupling alignment. This should be done by following
the instructions found in Section B, Part 4.
After the unit has been running for about one week,
the coupling halves should be given a fi nal check for
misalignment caused by pipe strains or temperature
strains. If the alignment is correct, both pump and driver
may be dowelled to the baseplate if desired.
D. MAINTENANCE
1. LUBRICATION
Grease Lubricated Pump
Pump bearings are properly lubricated with grease at the
factory before shipment. Periods of subsequent lubrication
depend on local conditions, loads, speeds, hours of
operation and temperature.
Periodic inspection of bearing lubrication should be made
and additional grease added as needed. At this time the
plug in the bottom of the bearing cover should be removed
and the bearing fl ushed with clean grease. A Chevron
SRI-2 or Shell Dolium “R” grease is recommended for
most installations. Do not overgrease as this causes high
bearing temperatures and shortens bearing life. The pump
should be run a short time to eject any excess grease and
the plug then replaced in the bearing cover.
Summary of Contents for Deming 5260 Series
Page 7: ...7 Figure 3 ...
Page 22: ...Notes ...