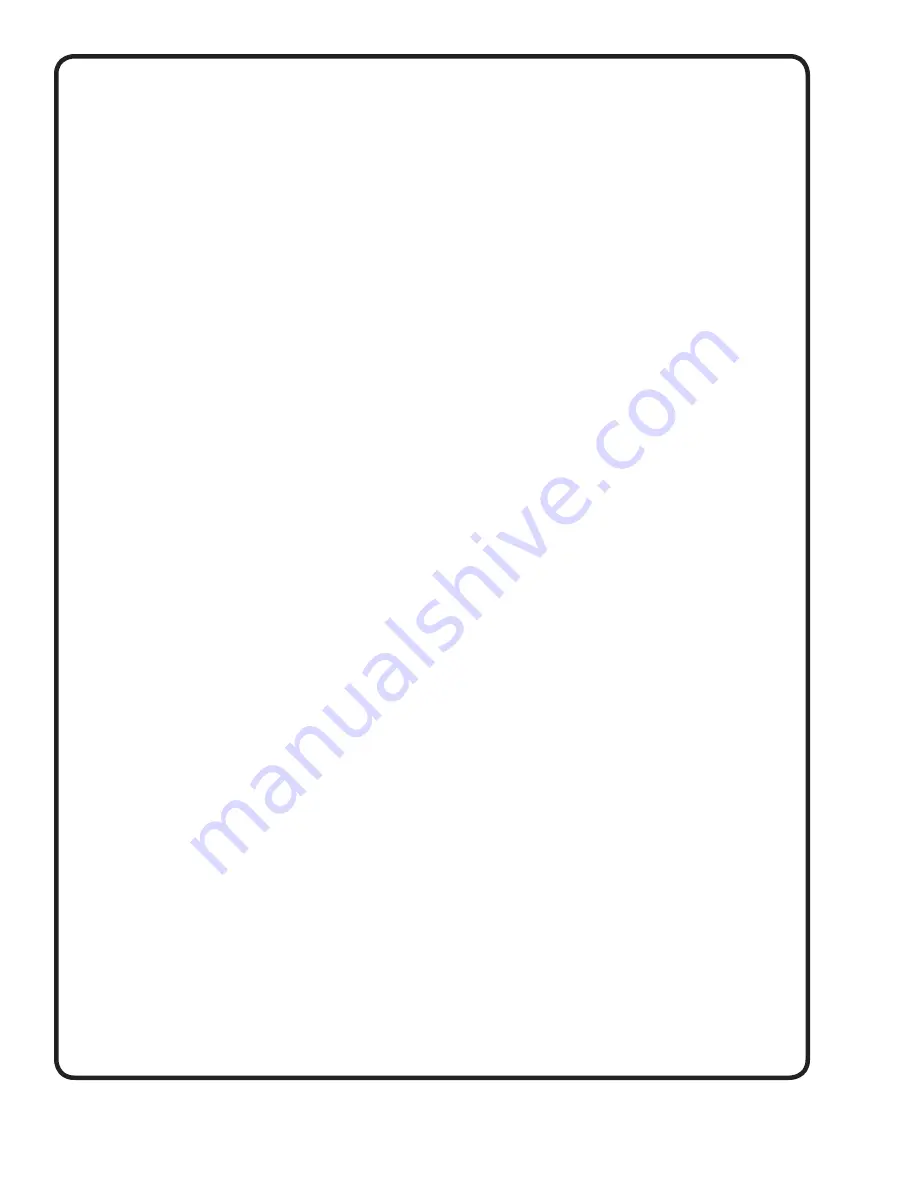
10
2. Install shaft sleeves. Be sure good hub gaskets are
in place on sleeves, to seal between sleeve and
impeller. If sleeves have internal o-rings, be sure
they are good. Make sure there are not sharp edges
or corners to cut o-rings. Line up slots on sleeves
with impeller key. If pack pump, install stuffi ng box
bushing. On mechanical seals, install stuffi ng box
bushing.
3. Clean and polish smooth the sleeves, making
sure there are no sharp edges or corners to cut the
seal’s rubber parts. If seal collars were removed or
being replaced, slide into place.
4. Inspect face of seal washer, if scratched or chipped,
replace. Clean inside of rubber bellows of seal
assembly. (Anti-freeze can be used as a lubrication
for installation of seal). Oil inside of seal bellows
and sleeves, with a mixture of 1/3 part STP and 2/3
part 10W oil. This allows seal assembly to be easily
pushed into position. Be sure the sealing washer is
in the proper position. The notches on the outside
edge of the sealing washer must mate with the lugs
in the retainer.
5. Slip spring retainer and spring over shaft or sleeve
and up against seal collar. Then slide the seal
bellows assembly over the sleeve, compressing
spring against seal collar, and seating spring
against bellows assembly. Gently release pressure.
The mechanical seal is a precision product, and
great care must be taken to avoid damage.
6. Inspect face of stationary seat. If grooved, replace
by removing old seal and cleaning seal cap. Oil
outer seal ring and push new seat into the seal cap
cavity, so the lapped surface side of seal seat will
mate with seal washer or rotating element taking
care not to marr seal surface. It must be seated
fi rmly and squarely.
7. Put casing rings on impeller
8. Put seal cap gaskets and seal caps into place.
9. Put 2 to 3 wraps of Tefl on sealing tape on shaft
threads and start shaft sleeve locknuts when use.
10.
Slide
defl ectors (rubber water slinger) onto shaft
11. Put on outboard bearing cap
12. Put on thrust collar.
13. Clean and check, or replace bearing. Hand pack
with a Lithium base grease
14. Put bearing on by only applying pressure to the
inner race. Care must be taken not to damage
seat, by wrapping a clean rag or paper towel around
shaft between seal cap and seal rotating element.
15. Install retaining ring (bearing snap ring), make sure
it is seated in grove shaft.
16. Clean all the old grease out of the bearing housing.
Check grease for saponifi cation, which is usually
caused by infi ltration of moisture, and noticed by the
whitish color of the grease. Also check for
carbonizing of grease which results from heat
caused by overgreasing. Put bearing housing on
and bolt up to bearing cap.
17. Put on inboard bearing cap.
18. Repeat Steps 13, 14 and 16.
19. Install pump coupling hub and key
20. If new casing half gaskets are to be installed, place
them onto lower half and trim to fi x.
CAUTION: Do
Not cut gasket at end of stuffi ng box in the seal
cap
area.
21. Place rotating assembly into lower case, making
sure
to
fi t holes in case wear rings on roll pins
in lower case half. (Keep seal cap gaskets next
to seal cap, to not tear them. Watch that seal collars
or packing bushings are in stuffi ng box).
22. Bolt outboard bearing housing to lower casing half
23. Bolt inboard bearing housing to lower casing half
24. Center impeller up in volute of lower casing half
25. Tighten shaft sleeve nuts and tighten setscrew in
sleeve
nuts
26. If seal collars were removed or need resetting,
rotate them 30° before tightening set screws. Set
them using the dimensions from Step 15 or
Disassembly Instructions. NOTE: Seal collar face
(Surface next to seal spring) must be perpendicular
to the shaft while rotating shaft.
27. Pack pumps thread and tighten gland studs into
casing. Place one ring of packing into stuffi ng box.
On successive rings of packing, stagger the
packing joints 120° to prevent excessive leakage
through the packing box. Under suction lift
conditions, or when external fl ushing is required,
the pump should be fi tted with lantern rings. Care
must be taken to locate these under the fl ushing
port drilled in casing. Each ring of packing should
be slid into place when being installed until stuffi ng
box is full.
28. Place casing half gaskets in place. When installing
new gaskets a small amount of grease evenly
applied to casing surface will help hold gasket in
place.
29. Put upper casing half (make sure seal caps and
seal cap gaskets will clear upper casing and that
jack screws in upper half have been backed off) into
place, taken care to install as to not slide gasket.
Check casing half gaskets at stuffi ng box and seal
cap area. Check for binding by rotating shaft.
30. Drive in case rollpins (to align upper and lower
halves) check for binding by rotating shaft.
31. Bolt casing halves together by tightening all bolts
until snug. To insure an equal clamping force,
tightening should be done in a sequence of steps.
First start with 50% of the full torque value, following
a “criss-cross” pattern. For instance, start at twelve
o’clock, then six o’clock, then nine o’clock, three,
o’clock,
eleven,
fi ve, eight, two and so on. After the
initial tightening of 50% torque the bolts 70%, then
100% to achieve the required clamping force. Follow
the “criss-cross” pattern in each sequence. After
the initial tightening has been done, the bolts
should be retightened as often as necessary to make
up for the loss of clamping force that occurs as the
gaskets compress. With the torque calculated
properly, using the correct torquing sequence, the
seal against leakage will be assured. Check for
binding by rotating shaft. (Torque requirements).
Summary of Contents for Deming 5260 Series
Page 7: ...7 Figure 3 ...
Page 22: ...Notes ...