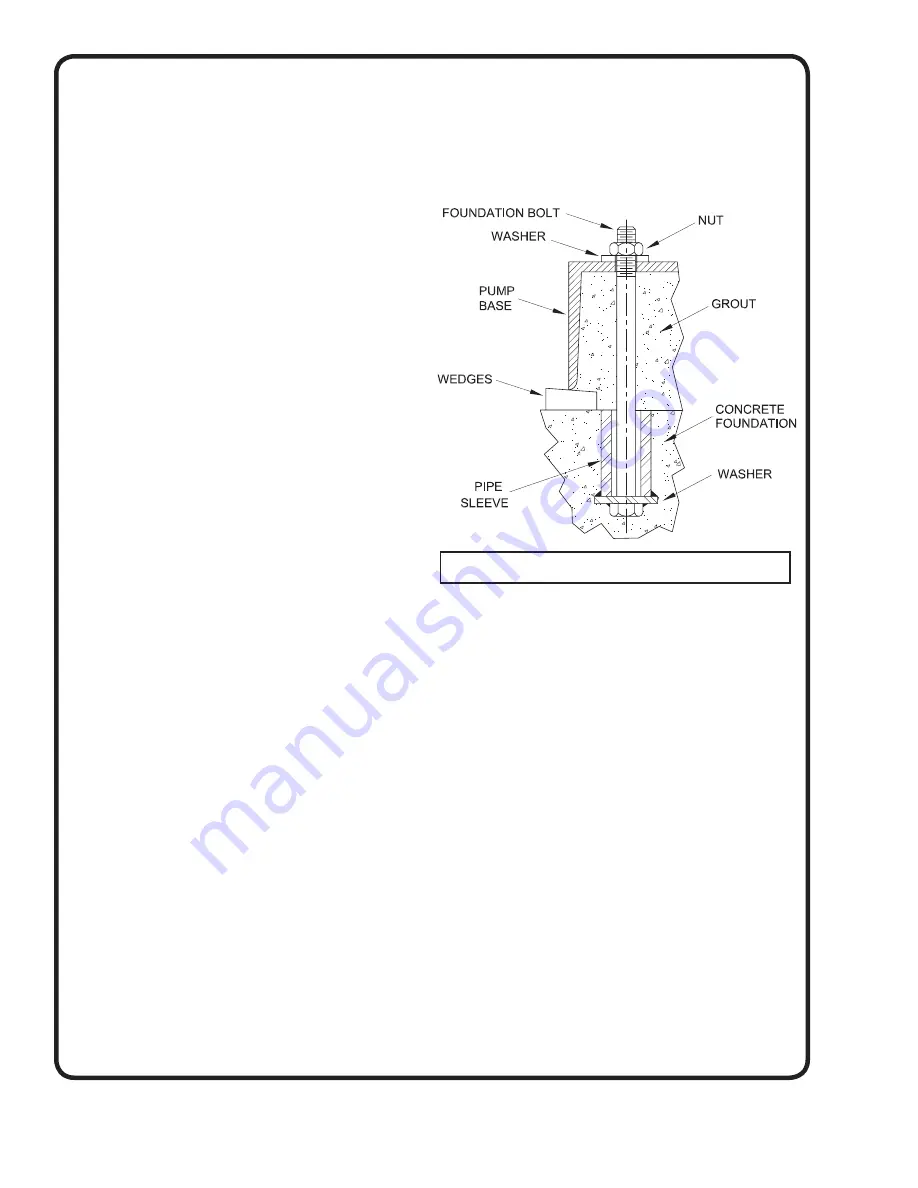
4
A - GENERAL INFORMATION
TO THE PURCHASER:
Congratulations! You are the owner of one of the fi nest
pumps on the market today. These pumps are products
engineered and manufactured of high quality components.
With years of pump building experience along with a
continuing quality assurance program combine to produce
a pump which will stand up to the toughest applications.
Check local codes and requirements before installation.
Servicing should be performed by knowledgeable pump
service contractors or authorized service stations.
RECEIVING:
Upon receiving the pump, it should be inspected for
damage or shortages. If damage has occurred, fi le a claim
immediately with the company that delivered the pump.
If the manual is removed from the crating, do not lose or
misplace.
STORAGE:
Short Term -
Pumps are manufactured for effi cient
performance following long inoperative periods in storage.
For best results, pumps can be retained in storage, as
factory assembled, in a dry atmosphere with constant
temperatures for up to six (6) months.
Long Term -
Any length of time exceeding six (6) months,
but not more than twenty four (24) months. The units
should be stored in a temperature controlled area, a roofed
over walled enclosure that provides protection from the
elements (rain, snow, wind blown dust, etc..), and whose
temperature can be maintained b40 deg. F and
+120 deg. F. Pump should be stored in its original shipping
container and before initial start up, rotate impeller by hand
to assure seal and impeller rotate freely.
SERVICE CENTERS:
For the location of the nearest Deming Service Center,
check your Deming representative or Crane Pumps &
Systems Service Department in Piqua, Ohio, telephone
(937) 778-8947 or Crane Pumps & Systems Canada, Inc.,
Bramton, Ontario, (905) 457-6223.
B - INSTALLATION
1. LOCATION
The pump should be installed as near the source of liquid as
possible with a minimum of piping on the suction side of the
pump. The discharge piping should be as direct as possible
with a minimum of fi ttings to lower friction loss.
The unit should be installed with adequate head room and
a maximum area for inspection and service. The installation
should be dry, well ventilated, and protected against moisture
and fl ooding.
2. FOUNDATION
The pump foundation should be suffi ciently substantial
to form a level, rigid support for the combined weight
of the pump and driver and maintain alignment of the
installed unit. Foundation bolts, of the proper size, should
be imbedded in the concrete. A pipe sleeve, about 2½”
diameters larger than the bolt, should be used to allow for
fi nal positioning of the bolts. See Figure 1.
3. MOUNTING:
Pumps and drivers that are received from the factory
with both machines mounted on a common base plate,
were accurately aligned before shipment. All baseplates
are fl exible to some extent and, therefore, must not be
relied upon to maintain the factory alignment. Preliminary
alignment is necessary after the complete unit has been
leveled on the foundation, and again, after the unit is
piped, and rechecked periodically as outlined in the
following paragraphs.
Position unit on foundation and level the base plate,
using rectangular metal blocks and shims, or wedges
having a small taper. A gap of 3/4” to 1½” should be
allowed between the base plate and foundation for
grouting.
Adjust the metal supports or wedges until the shafts of
the pump and driver are level. Check the coupling faces,
as well as the suction and discharge fl anges of the pump
for horizontal or vertical position by means of a level.
Correct the positions, if necessary, by adjusting the
supports or wedges under the base plate, as required.
Figure 1. Foundation Bolt Location and Anchorage
Summary of Contents for Deming 5260 Series
Page 7: ...7 Figure 3 ...
Page 22: ...Notes ...