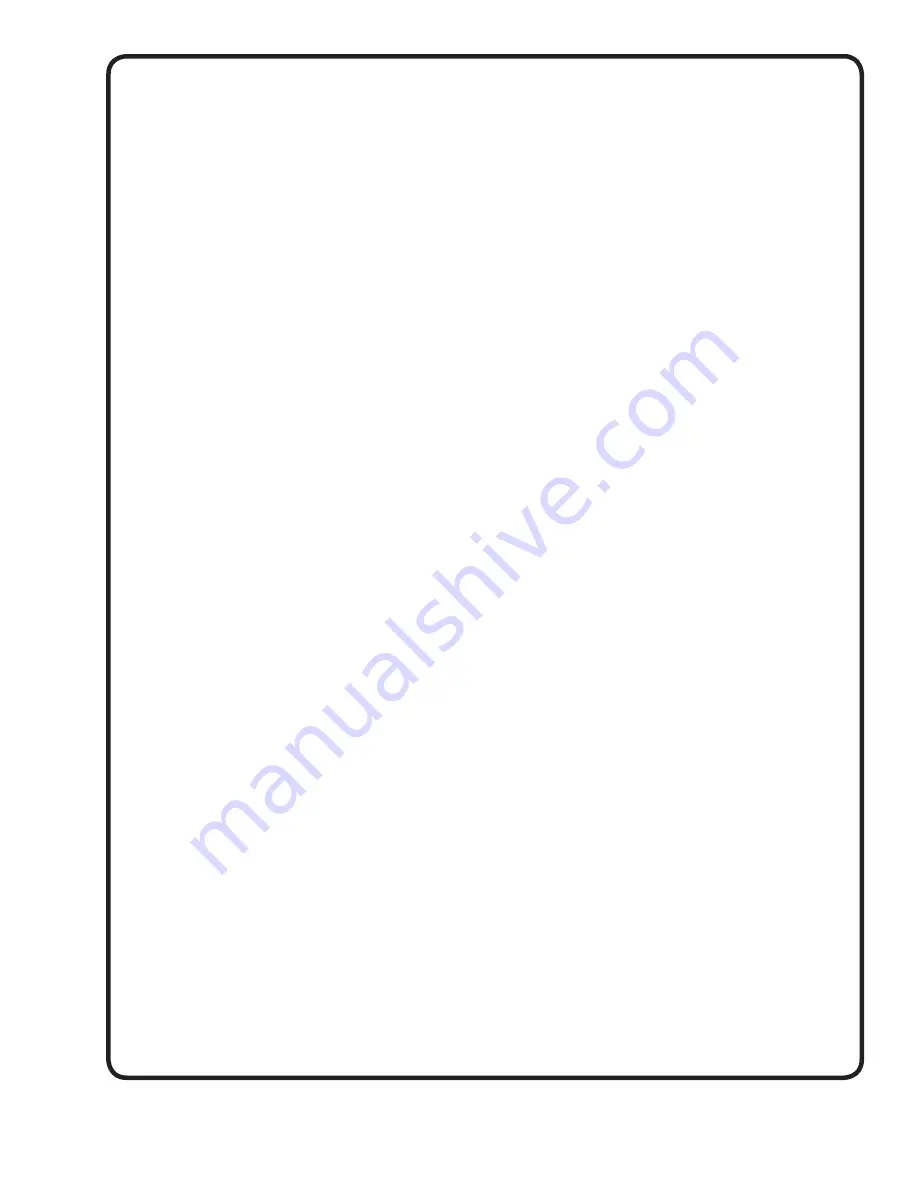
13
E - LOCATING TROUBLE
1. No Liquid Delivered
a. Pump not primed - See Priming
b. Speed too low - Check motor speed and nameplate
c. Discharge head too high
d. Suction lift too high
e. Impeller completely plugged
f. Wrong direction of rotation - Check wiring
g. NPSHA may be too low - pump cavitates check
total
NPSHR
h. Suction or discharge valves closed
i. Impeller installed backwards
2. Not Enough Liquid Delivered
a. Air leaks in suction piping
b. Speed to low - Check motor speed
c. Discharge head higher than anticipated.
Check discharge valve/system requirements
d. Suction lift too high
e. Impeller partially plugged
f. Wrong direction of rotation
g. Not enough suction head for hot liquid
h. NPSHA may be too low - pump cavitates
i. Mechanical defects
1. Impeller damage
2. Wear rings worn
j. Air entrainment
k. Flow meter improperly calibrated
l. Impeller installed backwards
3. Not Enough Pressure
a. Speed too low - Check motor speed
b. Air or gas in liquid
c. Incorrect impeller diameter - Check system
requirements
d. Obstruction in pump or piping
e. Air leaks in suction piping
f.
Specifi c gravity lower than specifi ed - May
require larger pump impeller
g. Defective pressure gauge
h.
Mechanical
defects
1. Impeller damaged
2. Wear rings worn
4. Pump Works For A While Then Quits
a. Air leaks in suction piping
b. Obstruction in pump or piping
c. Suction lift too high
d. Air or gas in liquid
e. Incomplete priming - See Priming
f. Air leak due to defective shaft packing
g. Air leak through stuffi ng box when operating with
high vacuum or high suction lift. Install
recirculation piping or pressurize from outside
liquid
source.
5. Pump Takes Too Much Power
a. Speed too high - Compare Pump and motor
nameplates
b. Head lower than rating - pumps too much liquid.
Check system requirements
c. Liquid specifi c gravity or viscosity greater than
expected. Requires large motor.
d. Pump and driver misalignment - Check casing for
pipe strain. Support piping and realign unit
e. Wrong direction of rotation
f. Electrical defects - Check power supply and motor
g. Impeller oversized for system requirements
h. Partial freezing or thickening of liquid when
pumped. Check liquid characteristics.
i.
Mechanical
defects
1. Bent pump shaft.
2. Impeller binds in casing - Check impeller
adjustment
3.
Stuffi ng box packing too tight. See Packing
6. Excessive Pump Vibration
a. Cavitation at pump suction due to insuffi cient
NPSHA. Alter installation to reduce NPSHR
b. Impeller out of balance - Check mechanical
(static)
balance
c. Pump and motor misalignment
d. Obstruction in pump impeller
e. Pump shaft bent
f. Worn pump bearings
g. Impeller imbalance due to wear or corrosion
h. Motor imbalance
i. Base plate loose on foundation or insuffi cient
strength to support the load
7. Pump and/or Motor Noise
a. Pump and motor misalignment
b. Pump cavitation
c. Base plate loose or not grouted
d. Pump bearings worn
e. Motor bearings worn or fan rubs housing
f. Foreign matter in pump
g.
Broken
shaft
h. Liquid velocity in pump or valves due to greater
liquid
fl ow than anticipated.
i. Pump impeller imbalance due to wear.
Summary of Contents for Deming 5260 Series
Page 7: ...7 Figure 3 ...
Page 22: ...Notes ...