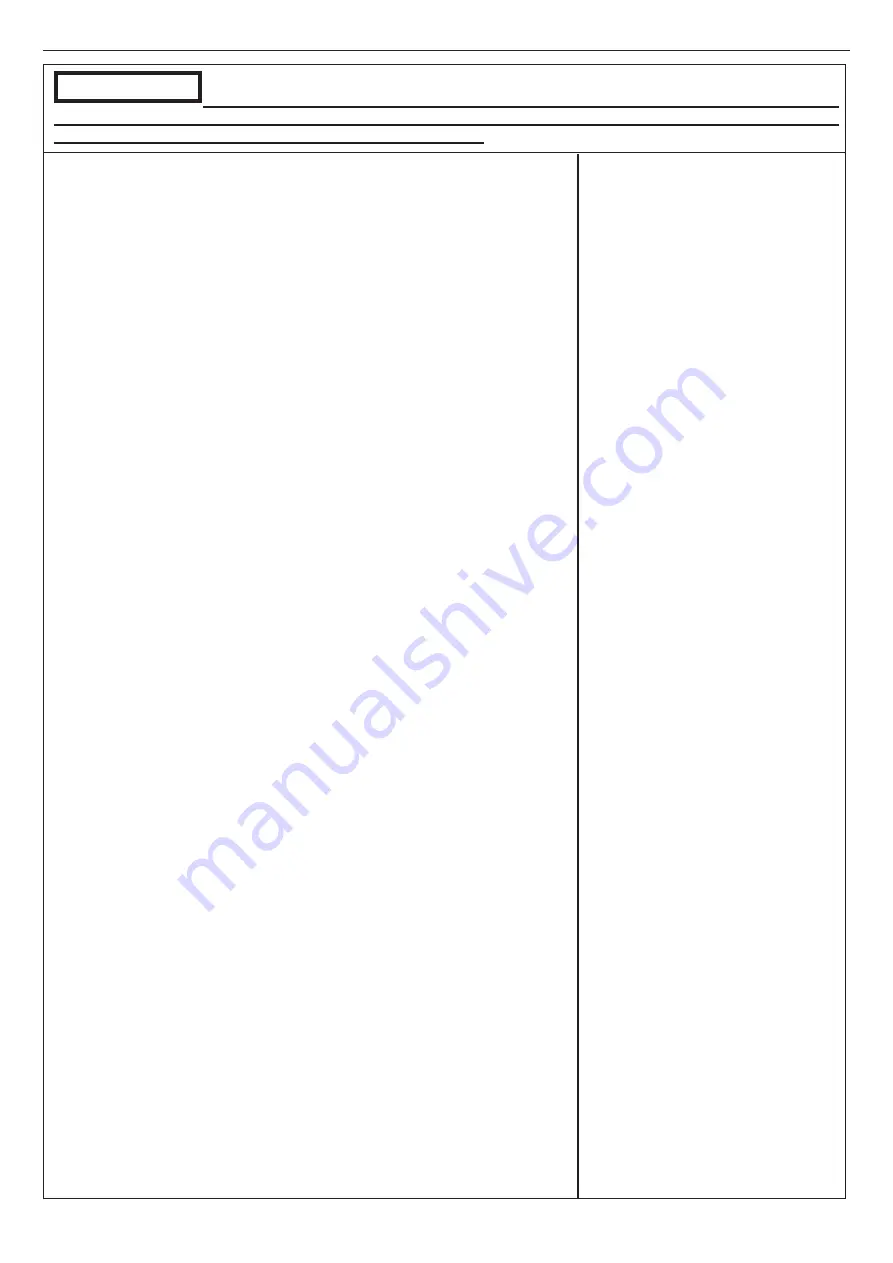
3
AGUAPLUS
COSMOGAS
Installation location: The heater
must be located in an area where
leakage of the tank or connections
will not result in damage to the area
adjacent to the heater or to lower
floors of the structure. When such
locations cannot be avoided, it is
recommended that a suitable drain
pan, adequately drained, be installed
under the heater. The pan must not
restrict combustion air flow.
Installation location: The heater must
not be installed on carpeting.
In the event of a breakdown and/or
malfunction of the heater, turn off the
unit and do not make any attempt to
repair it. The heater must be serviced
exclusively by a Qualified installer
using original spare parts.
Installation, modifications
Seal the adjustment devices after
every calibration.
In agreement with the provisions
for use, the user must keep the
installation in good working order and
guarantee reliable and safe operation
of the appliance.
We also highlight the importance of
an annual scheduled maintenance
contract with a professionally
qualified technician.
The end user must have maintenance
performed on the appliance only by
professionally qualified technicians
in accordance with this manual and
in full compliance with both local and
national standards.
Before performing any cleaning
or maintenance, disconnect the
appliance from the mains power
supply.
After any cleaning or maintenance,
before reconnecting the power
supply, make sure that all internal
parts are properly dry.
This appliance is not intended for
use by persons (including children)
with reduced physical and sensory
conditions or lack of experience and
knowledge, unless they have been
given supervision or instruction
concerning use of the appliance by
a person responsible for their safety.
This manual is an integral and
essential part of the product and
must be kept carefully by the user,
for possible future consultation. If the
appliance must be transferred or if
you should move and leave the unit
to another user, always ensure that
this manual remains with the new
user and/or installer.
Do not use “homemade cures” or
“heater patent medicines”. Serious
damage to the heater, personnel, and/
or property may result.
Do not use petroleum-based cleaning
or sealing compounds in the heater
system. Gaskets and seals in the
system may be damaged. This can
result in substantial property damage.
Technical drawings
All drawings in this manual relating
to electrical wiring, hydraulic and gas
layouts are purely indicative. The
external services such as electrical
cable types and sizes, water pipes and
gas pipes must always be checked by
a professionally qualified technician or
engineer to verify compliance with all
relevant standards, Laws and codes of
good practice.
NOTICE!
Local approval of the flue system and
the condensate connection to the public
sewer system may be required.
The local building regulations stipulating
the installation rules at the time of
installation.
When calling or writing about the heater
– Please have the heater model and
serial number from the heater rating
plate.
Any claims for damage or shortage in
shipment must be filed immediately
against the transportation company by
the consignee.
The manufacturer declines all liability,
contractual or otherwise (warranty
included), for any damage to people,
animals property or this same appliance,
caused by:
a) - incorrect installation;
b) - failure to comply with this or any
other instruction provided by the
manufacturer;
c) - failure to comply with the applicable
local and/or national regulations in
force;
d) - incorrect use of this appliance
e) - inadequate or incorrect service
f) - inadequate or incorrect maintenance.
SAFETY INSTRUCTIONS
CAUTION!!!
FAILURE TO COMPLY WITH THESE PROVISIONS AND REQUIREMENTS MAY
COMPROMISE THE SAFETY OF THE UNIT AND CAN RESULT IN A FIRE OR EXPLOSION CAUSING
PROPERTY DAMAGE, PERSONAL INJURY, OR DEATH.