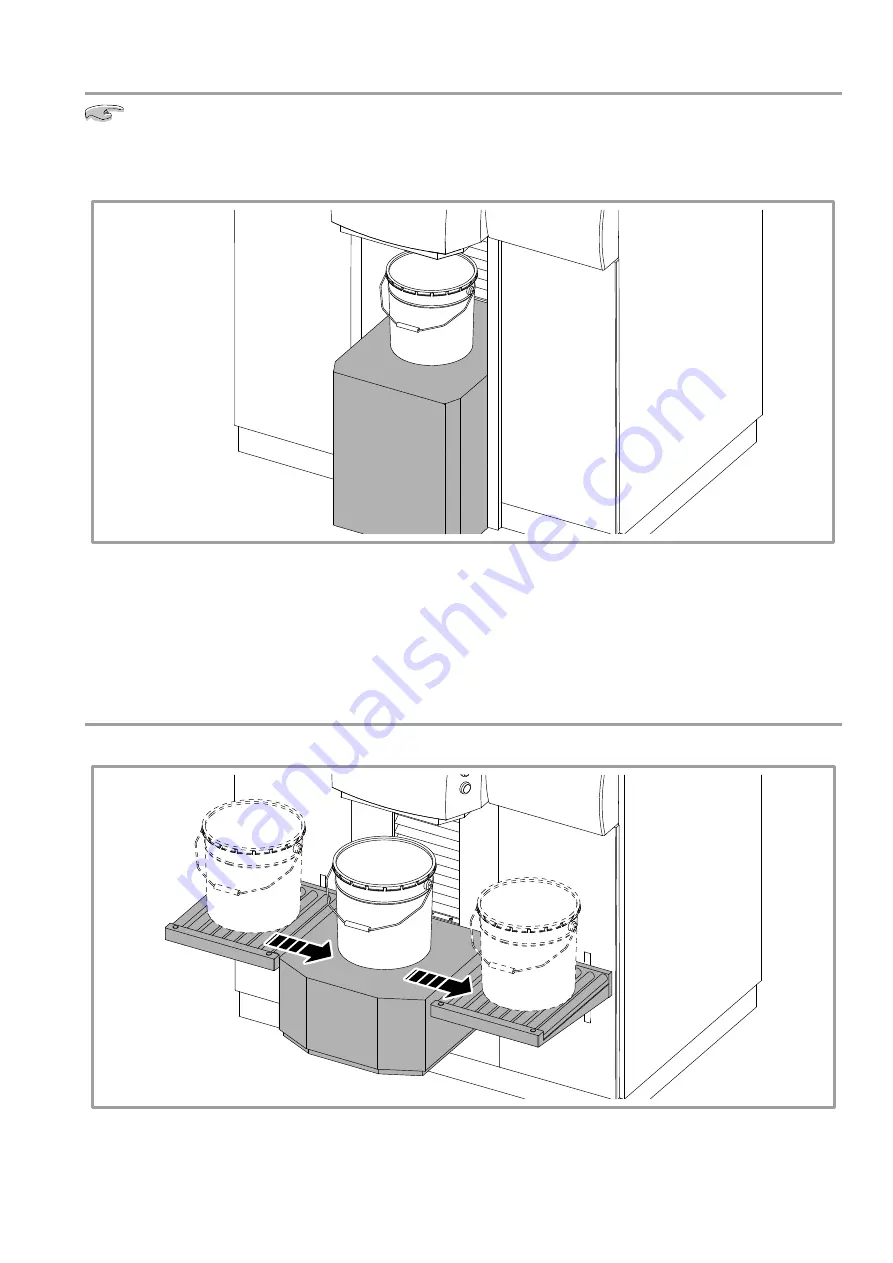
USING THE DISPENSER
- 33 -
COROB™ D600 - D700 - D800TX
6.3.2
Loading the can - Automatic shelf
With the purpose to prevent any crushing risks, the machine is fitted with two safety plates (chapter
The safety plates intervene by causing the shelf to stop if they are inadvertently touched by the operator.
1.
Place the can on the shelf. Use the panel roll conveyors, if fitted, to slide and ease heavy cans on the shelf
The management program controls the movement of the automatic shelf, checks for the can presence and that
the can placed on it is actually the one selected through the program for dispensing the formula.
These checks are also carried out by a photocell located underneath the nozzle center. The shelf automatically
stops when the can is detected by the photocell.
After a can has been positioned, the program will indicate an error if the can is missing from the shelf, or if it is
larger or smaller than the one selected for dispensing.
6.3.3
Loading the can - Panel roll conveyor
Place the can on the roll conveyor and slide it under the dispensing nozzles.