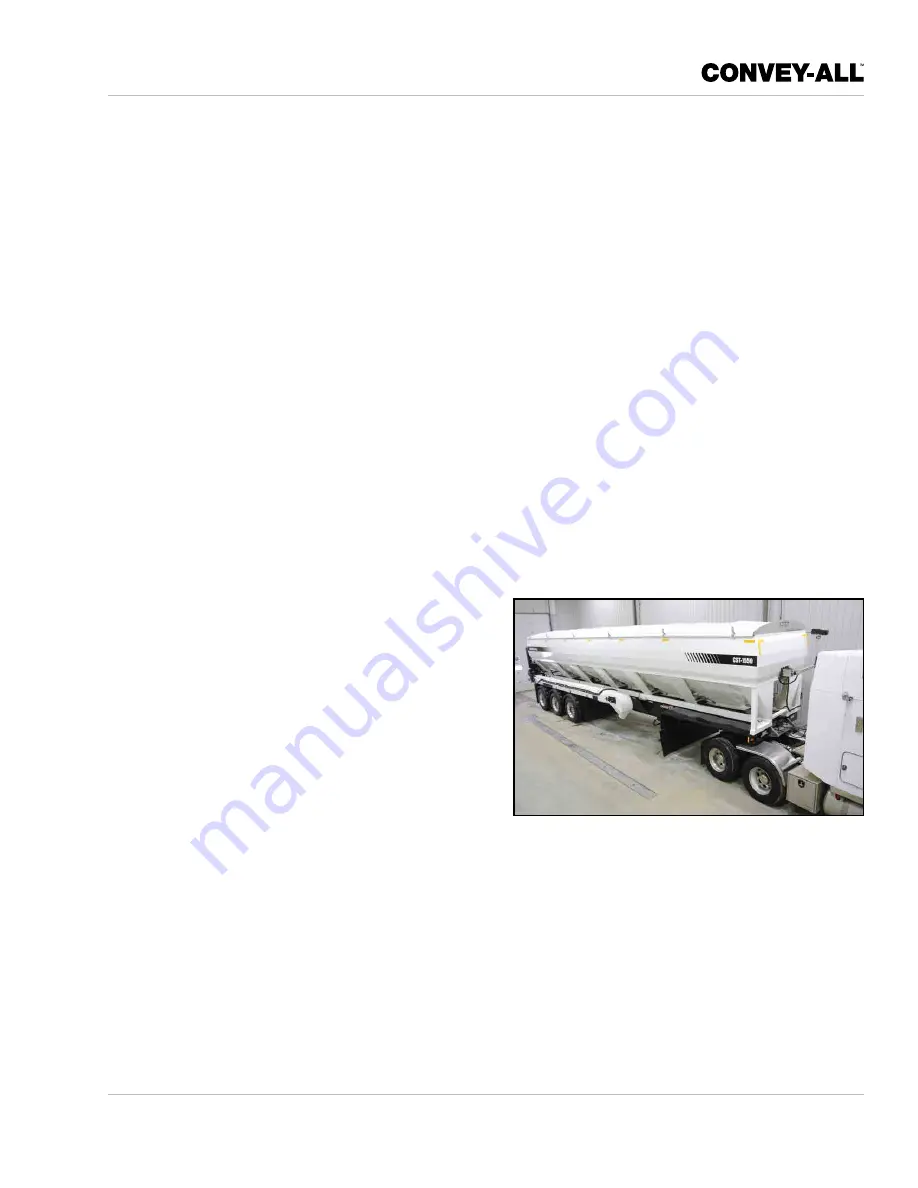
Revised 10.2020
3-19
Operator’s Manual: CST-1550
3.10 STORAGE
After the season's use, or when the CST will not
be used for a period of time, completely inspect
and clean very part of the tender.
Replace or repair any worn or damaged
components to prevent any unnecessary down
time at the beginning of the next season.
1. Remove all the left over product from inside
the compartments, also on and around both
conveyor belts.
2. Thoroughly wash the unit to remove all dirt,
mud, debris and residue.
- Wash inside the compartments and around
the gates.
- Wash the top and under the belts.
- Clean inside the rear conveyor tube.
3. Close roll tarp to prevent unauthorized entry
into the compartments. Also to protect the
compartment coating against sun damage.
4. Inspect all rotating parts for entanglements.
Remove anything caught in the mechanisms.
5. Check the condition of the components
in the hydraulic system. Repair, replace or
adjust as required.
6. Check the condition of the slave and rear
conveyor belts. Replace any damaged belts.
7. Lubricate all fittings and fill grease cavities.
8. Touch up all paint nicks and scratches to
prevent rusting.
Fig 55 - Tender in storage
9. Remove the battery.
- Be sure it is fully charged.
- Store it inside.
- Do not sit battery on a cold, concrete floor.
10. It is best to store the machine inside.
If that is not possible, cover the engine with a
waterproof tarpaulin and tie down securely.
11. Store in an area away from human activity.
12. Do not allow children to climb on or play
around the stored tender.
3.11 REMOVING FROM STORAGE
When removing the tender from storage, follow
the Pre-Trip and Pre Operation Checklists in
Sections 3.4 and 3.5.
Summary of Contents for CST-1550
Page 1: ...OPERATOR S MANUAL COMMERCIAL SEED TENDER CST 1550...
Page 4: ...This page intentionally left blank...
Page 8: ...Operator s Manual CST 1550 1 2 01 2019 This page intentionally left blank...
Page 22: ...Operator s Manual CST 1550 2 14 01 2019 This page intentionally left blank...
Page 42: ...Operator s Manual CST 1550 3 20 01 2019 This page intentionally left blank...
Page 54: ...Operator s Manual CST 1550 4 12 01 2019 This page intentionally left blank...
Page 59: ...Operator s Manual CST 1550 01 2019 6 3 This page intentionally left blank...