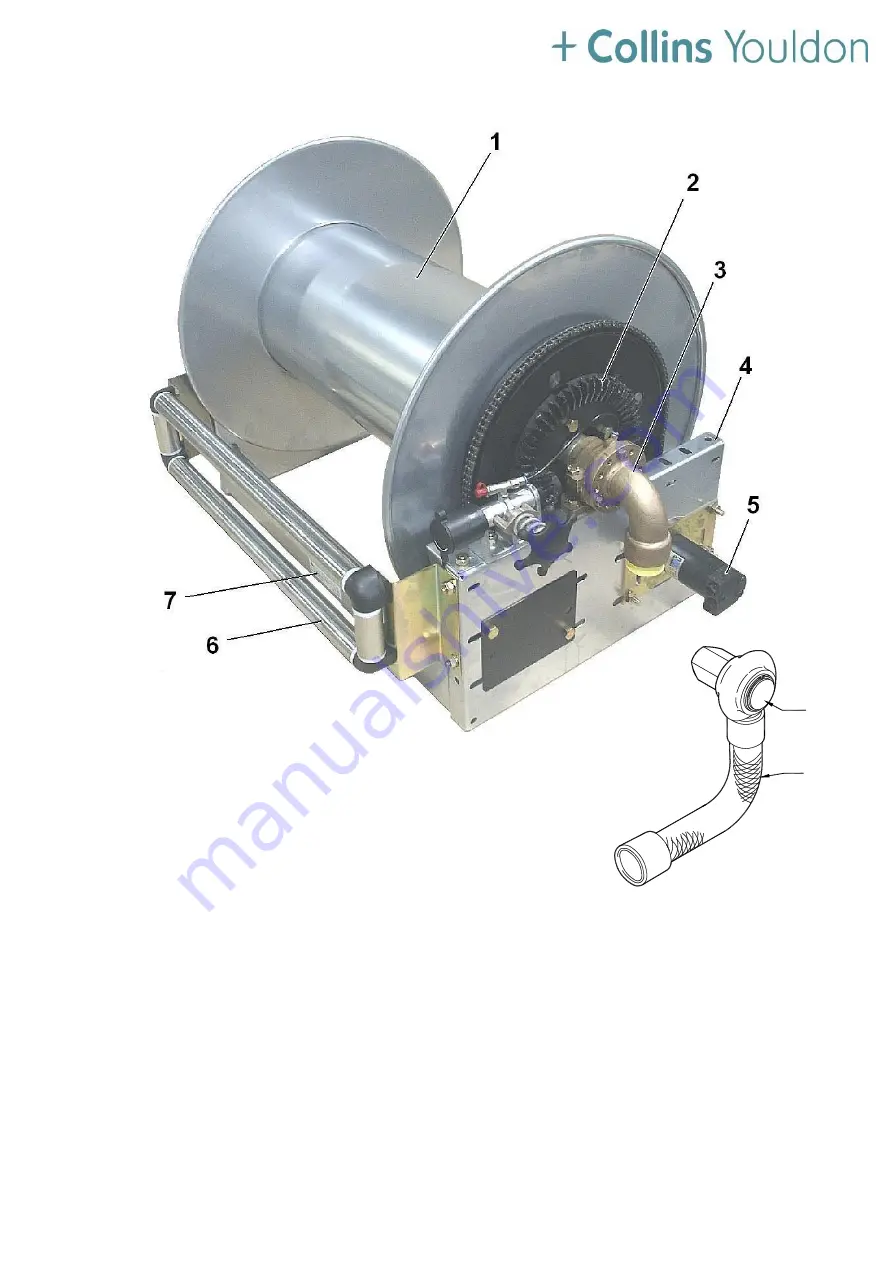
Product Manual
SDM09H-Hosereel Page 3
Issue 2
– April’20
10
11
1
Drum
2
Drive gears and chain
3
Centre shaft inlet / swingjoint connection
4
Frame
5
Hydraulic motor
6
Hose roller guides (if fitted)
7
Serial number plate
10
Swingjoint
11
Flexible connection
Figure 1
– Typical hydraulic motor rewind hosereel
(for more part details refer to Appendix
1)