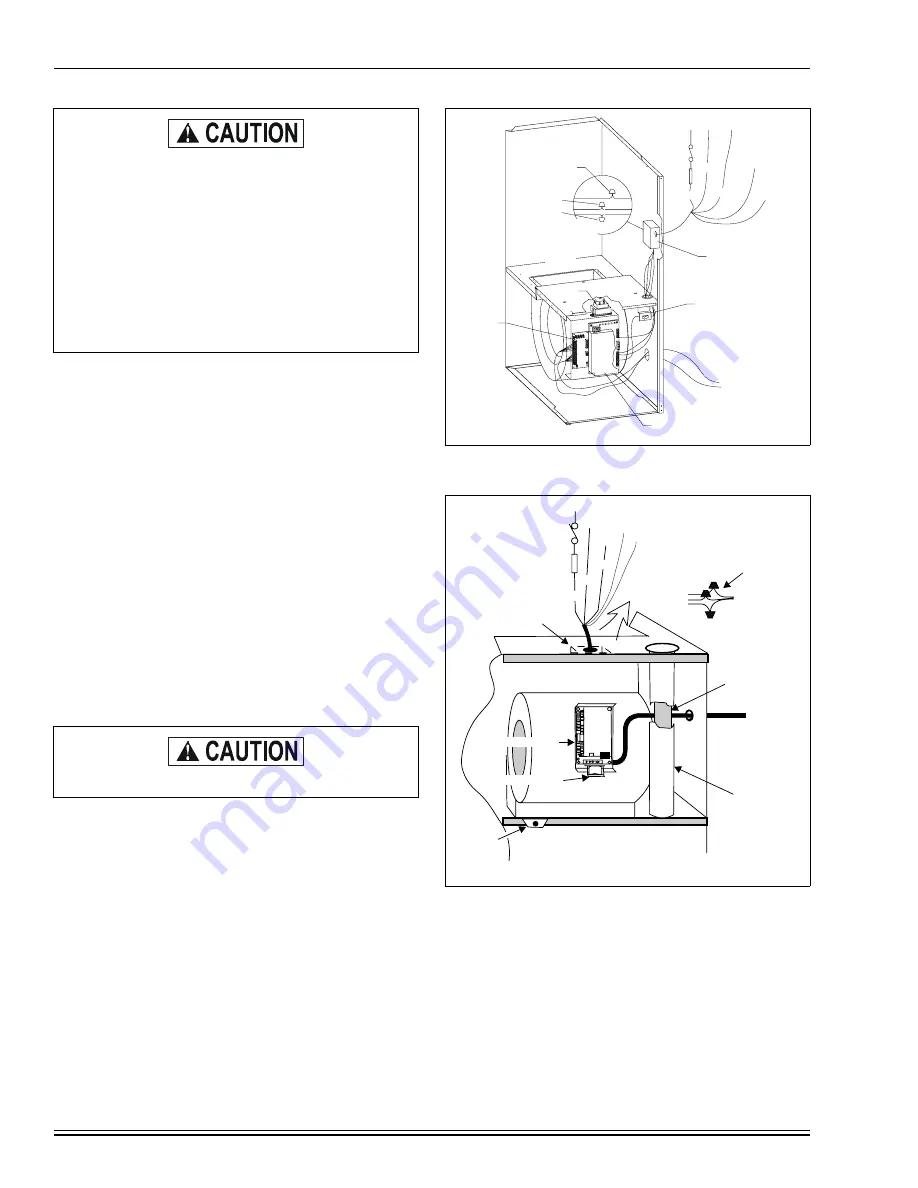
035-17468-001 Rev. A (801)
12
Unitary Products Group
ELECTRICAL POWER CONNECTION
Field wiring to the unit must conform to and be grounded in
accordance with the provisions of the National Electrical
Code ANSI/NFPA No. 70-latest edition, Canadian Electric
Code C22.1 Part 1 - (latest edition) and/or local codes. Elec-
tric wires which are field installed shall conform with the tem-
perature limitation for 63°F / 35°C rise wire when installed in
accordance with instructions. Specific electrical data is given
for the furnace on its rating plate and in Table 1 on Page 5 or
Table 2 on Page 6.
Provide a power supply separate from all other circuits. Install
overcurrent protection and disconnect switch per local/
national electrical codes. The switch should be close to the
unit for convenience in servicing. With the disconnect switch
in the OFF position, check all wiring against the unit wiring
label. Also, see the wiring diagrams in this instruction.
NOTE:
The furnace’s control system depends on correct
polarity of the power supply and a proper ground connection.
Refer to FURNACE CONTROL DIAGNOSTICS on Page 37,
for symptoms of reversed power supply polarity.
Connect the power supply as shown on the unit wiring label
on the inside of the blower compartment door and Figure 11
or 12 on Page 12. The black furnace lead must be connected
to the L1 (hot) wire from the power supply. The white furnace
lead must be connected to neutral. Also, the green equip-
ment ground wire must be connected to the power supply
ground.
Remove the screws retaining the wiring box cover. Route the
power wiring through the opening in the unit into the junction
box with a conduit connector or other proper connection.
Make wiring connections referring to Figure 11 or 12 and
replace the junction box cover and screws.
An alternate wiring method is to use a field provided 2 x 4 box
and cover on the outside of the furnace. Route the furnace
leads into the box using a protective bushing where the wires
pass through the furnace panel.
Compounds used on threaded joints of gas piping
must be resistant to the action of liquefied petroleum
LP gases. After connections are made, leak-test all
pipe connections.
After all gas piping connections are completed, leak
test all joints, fittings and furnace connections with
rich soap and water solution, commercially available
bubble type leak detection fluid, or other approved
means.
Do not use an open flame or other source of
ignition for leak testing.
Use copper conductors only.
FIGURE 11 :
Electrical Wiring - Upflow Models
FIGURE 12 :
Electrical Wiring - Downflow / Horizontal
Models
BLK/BLK
WHT/WHT
GRN/GRN
HUM
EAC
WIRING INSIDE
JUNCTION BOX
BURNER
COMPARTMENT
CFM/TIMER
BOARD
BLOWER
COMPARTMENT
IGNITION MODULE
CLASS 2 SYSTEM
CONTROL WIRING
TO THERMOSTAT
DOOR SWITCH
JUNCTION BOX
EAC (HOT)
HUM (HOT)
GND.
N
L1
(HOT)
WHT
GRN
BLK
JUNCTION
BOX
BLK/BLK
WHT/WHT
GRN/GRN
VENT PIPE
CLASS 2 SYSTEM
CONTROL WIRING
TO THERMOSTAT
L1
(HOT)
GND
N
WIRING INSIDE
JUNCTION BOX
BLOWER COMPARTMENT
FLUE
CHASE
DOOR
SWITCH
BURNER COMPARTMENT
TRANSFORMER
IGNITION MODULE
GRN
WHT
BLK
EAC (HOT)
HUM (HOT)