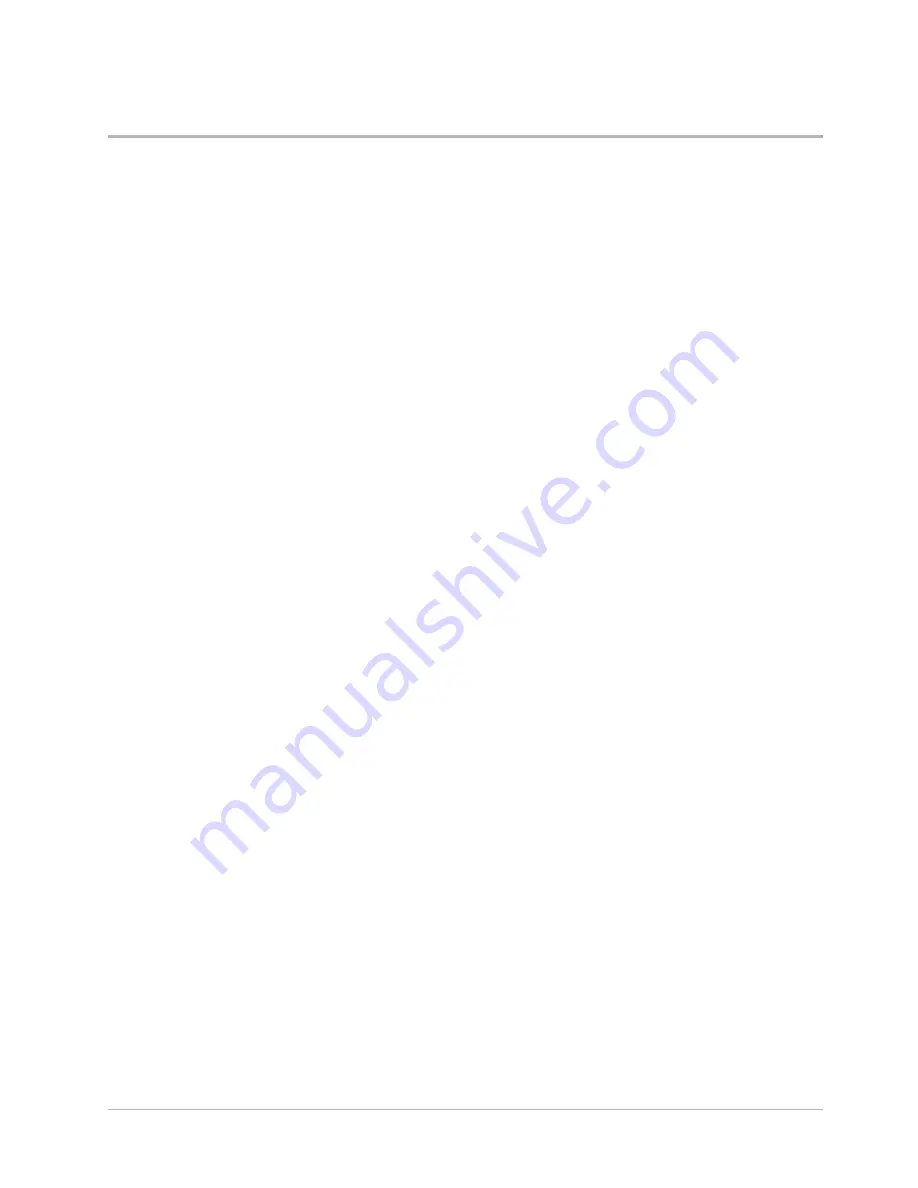
2005 Precedent IQ System Electric Golf Car Maintenance and Service Manual
Page i
FOREWORD
Club Car vehicles are designed and built to provide the ultimate in performance efficiency; however, proper
maintenance and repair are essential for achieving maximum service life and continued safe and reliable
operation.
This manual provides detailed information for the maintenance and repair of the electric Precedent vehicles,
and should be thoroughly reviewed prior to servicing the vehicle. The procedures provided herein must be
properly implemented, and the DANGER, WARNING, and CAUTION statements must be heeded.
This manual was written for the trained technician who already possesses knowledge and skills in electrical
and mechanical repair. If the technician does not have such knowledge and skills, attempted service or
repairs to the vehicle may render the vehicle unsafe. For this reason, Club Car advises that all repairs and/or
service be performed by an authorized Club Car distributor/dealer representative or by a Club Car factory-
trained technician.
It is the policy of Club Car, Inc. to assist its distributors and dealers in continually updating their service knowl-
edge and facilities so they can provide prompt and efficient service for vehicle owners. Regional technical rep-
resentatives, vehicle service seminars, periodic service bulletins, maintenance and service manuals, and
other service publications also represent Club Car’s continuing commitment to customer support.
This manual covers all aspects of typical vehicle service; unique situations, however, do sometimes occur
when servicing a vehicle. If it appears that a service question is not answered in this manual, you may write
to us at: Club Car, Inc.; P.O. Box 204658; Augusta, Georgia 30917; Attention: Technical Services, or contact
a Club Car Technical Service Representative at (706) 863-3000, ext. 3580.
Copyright © 2005 Club Car, Inc.
Club Car
and
PowerDrive
are registered
trademarks of Club Car, Inc.
This manual effective August 2, 2004.