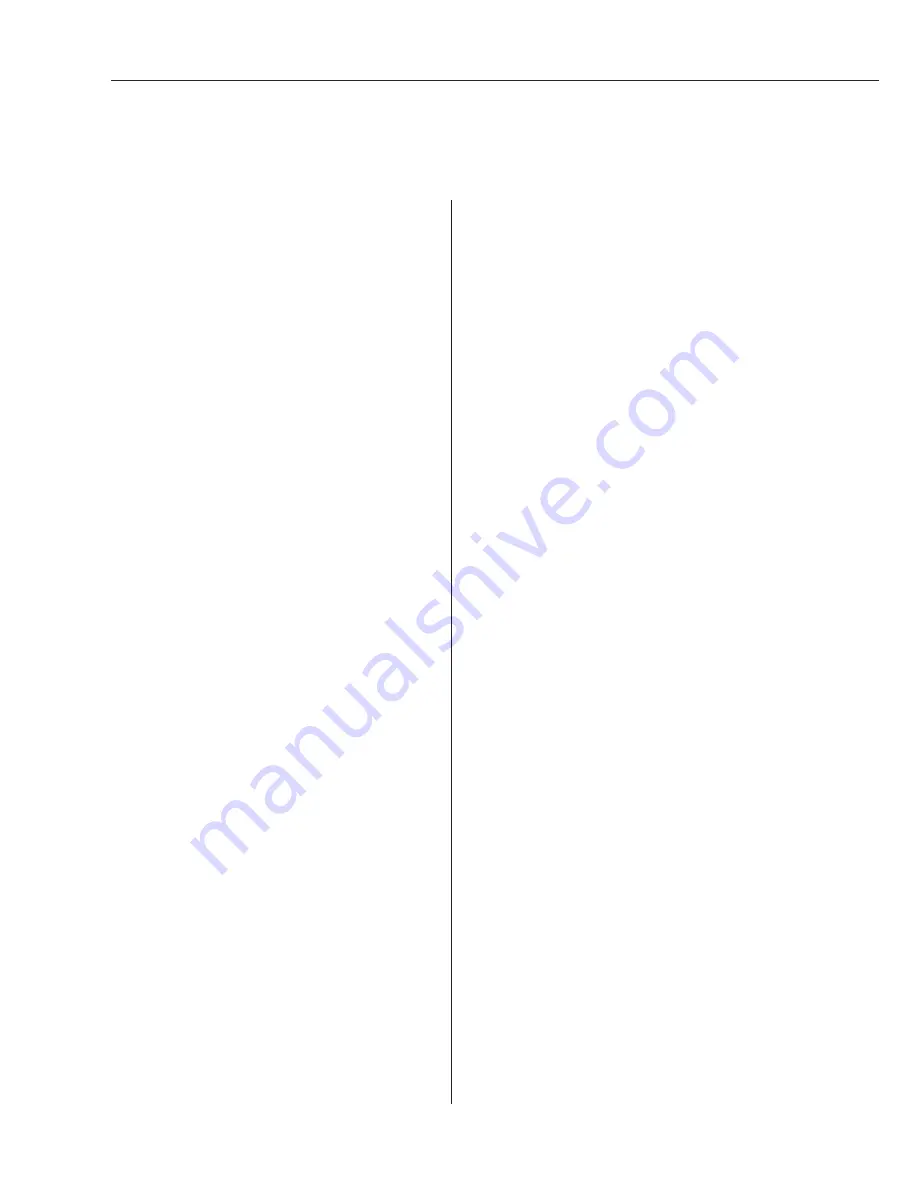
14
GLC 353/503/553 MC3
Operating instructions
General instructions for shielded gas
welding
With MIG/MAG shielded arc welding machines both
short arc and spray arc can be used.
Short arc is also called “dip-transfer arc”. When using
the short arc procedure, there is a relatively low welding
density on the welding wire so that the additional
material passes on to the workpiece in the shape of
individual drops (approx. 50 - 80 drops per second).
The heat input itself is relatively low so that with this
method thin sheet as well as root and vertical up seams
with thicker plate can be welded (also awkward position
welding).
With the spray arc technique a high current density is
used on the wire cross section. The welding material no
longer passes in drops onto the workpiece but as a
spray. Wherever an adequate welding performance as
regards the fusion quantity is required, the spray arc
process is the only one to consider.
At less than approx. 180 Amps/mm
2
current density
with steel wire short arc welding is generally considered,
whereas with more than 200 Amps/mm
2
the spray arc
technique starts to be used. The transition from short
arc to spray arc varies according to the different kind of
gases.
Using CO
2
as shielding gas, deep penetration is a
feature with steel welding, whereas, Argon S 5 (Ar +
5 % O
2
) for example gives only slight penetration. Using
gas mixtures (normal ratio about 90 % Ar + 5 % CO
2
+
5 % O
2
) penetration lies somewhere between the two
above gases.
Due to the deep penetration when using CO
2
, the
wedge angle must not exceed 30 - 40°. Less welding
material is therefore required on the one hand and on
the other, the welding efficiency is increased.
In the case of thin sheet, up to 3 mm maximum, the
vertical down seam position is advisible, as this results
in a higher welding speed and the surface appearance
of the seams is also improved.
High alloy steels are welded using protective gas K2 (Ar
+ 3% CO
2
).
Non-ferrous metals such as aluminium, copper, bronze,
etc. are welded with pure Argon 99.9% or gas mixtures
consisting of Argon and Helium (65 % Ar + 35 % He).
In the case of copper welding it is also necessary to
preheat the workpiece from 4 - 5 mm thickness upwards
to coat the welding edges with a deoxidizing paste.
During welding the welding torch must be held at an
angle of 5° towards the vertical of the workpiece. The
tip is approx. 15 mm away from the workpiece wire
diameter.
Special instructions for pulsed arc
welding
Spray arc
Using Argon or Argon mixtures with less than 20% CO
2
and sufficient high power and voltages the material
transition is carried out freely in the form of small drops
or drop chains without short circuit formation. Therefore
a spatter free welding is possible with the spray arc. A
precondition is, however, the use of the above shielding
gases. Due to the high energy input and the high
deposit efficiency this technique is only used - similar to
the semishort circuiting arc weldment - for the filler and
cover pass welding in the w- and h-position.
Pulsed arc
The short-circuit free material transition of the spray arc
is made use of by the pulsed arc technique. The energy
source switches periodically to a higher pulse current,
which makes an aimed and well controllable material
transition possible, while the base current serves for
the ionization of the arc distance and the preheating of
the wire electrodes end and the material surface. By
means of these current pulses a free material transition
in the rhythm of the pulse frequency is achieved.
This technique allows a good mastery of the molten
pool, which is very important for out-of position welding.
Due to the high pulse currents in the case of small base
currents relatively thick electrodes can be used.
The working range in the pulse technique is restricted
to the min. or max. current capacity of the wire electrode
used.
The disadvantage of the complicated adjustment of the
welding process (max. 5 parameters) is compensated
in case of an aimed variation of the welding parameters.
Therefore the degree of dilution in case of deposit
welding is for example kept small, or when selecting a
material transition with one drop per pulse with
corresponding drop size a virtually spatter-free welding
is achieved.
The correct pulse current adjustment is achieved when
the wire end can be seen as tip in the arc.
Summary of Contents for GLC 353 MC3
Page 2: ......
Page 6: ...4 GLC 353 503 553 MC3 Operating instructions...
Page 8: ...6 GLC 353 503 553 MC3 Operating instructions...
Page 18: ......
Page 28: ...B 10 Operation GLC 353 503 MC3...