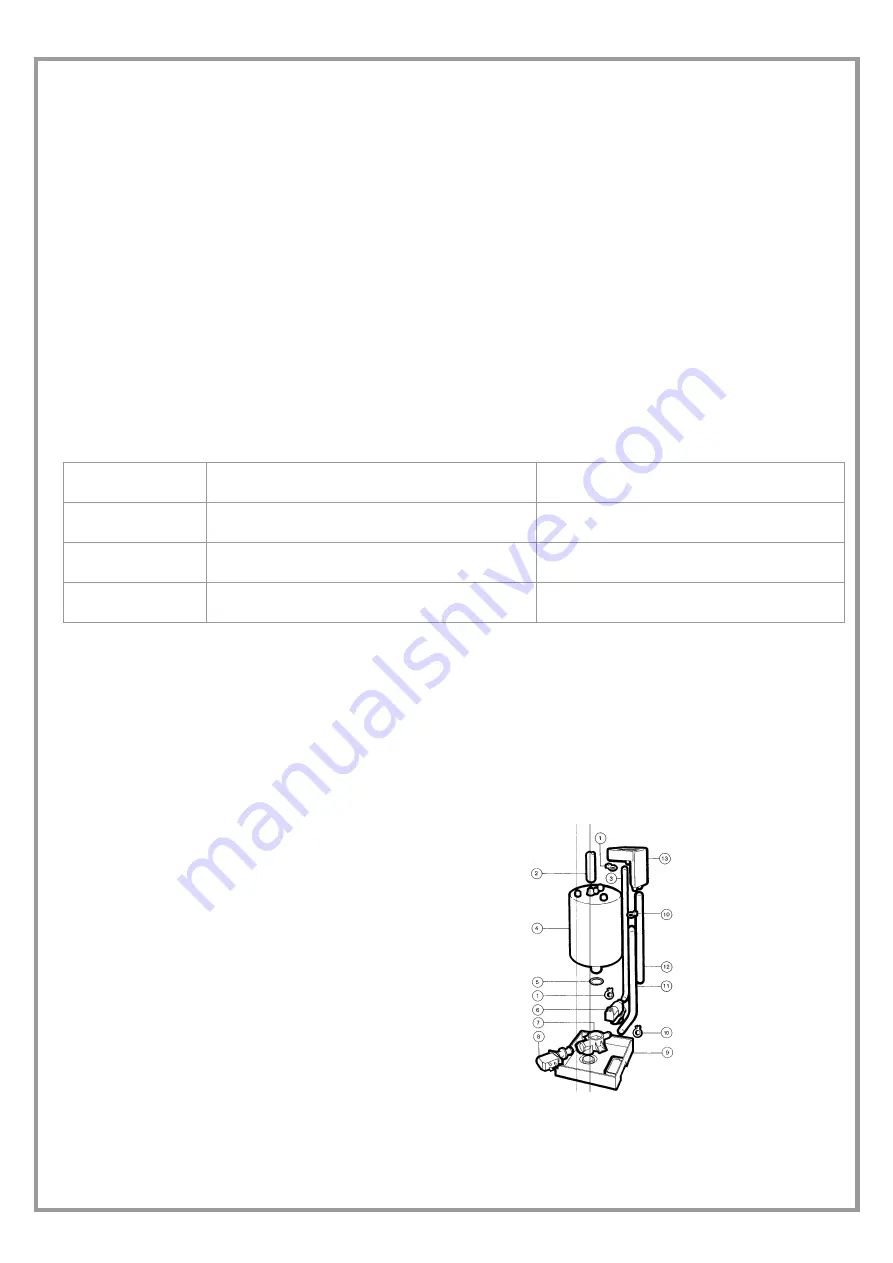
pag
31
DUCTING
Check the fixing screws and the operation of the anti-vibration devices in order to prevent the transmission of vibrations in the
room.
ELECTRIC FANS
Make sure that the fans and the relative protection grids are well fixed.
Check, if possible, the unbalances of the electro-fan evident by noise and anomalous vibrations. Verify that the terminal
protection covers are closed and the cable holders are properly positioned.
STEAM HUMIDIFIER AND IMMERSED ELECTRODES
The humidifier and the cylinder contain live electrical components and hot surfaces. All maintenance operations must be
performed by qualified, experienced personnel who have been trained on possible hazards.
During operation, the steam production cylinder reaches high temperatures!
Maintenance must be performed after the cylinder has cooled. Use protective gloves.
The cylinder must be replaced periodically. This operation is necessary when lime incrustations build up on the inside such
that sufficient current passage does not occur. How frequently this needs to be done depends on the water supply. The harder
the water, the more often the cylinder will need to be replaced. The water supply must not be softened. This causes corrosion
of the electrodes, foaming and possible abnormal operation. After prolonged use or use with very hard water, the solid
deposits on the electrodes may increase in size until they adhere to the inner wall of the cylinder. With especially conductive
deposits, the plastic may heat so much that it melts, resulting in water leakage.
In case of leaks, power off the unit before touching the cylinder, because electrical current may be flowing through the water.
PERIODIC CHECKS OF CYLINDER
fortnightly
after not more than 300 hours of service
check of operation, general condition, lack of
leaks
quarterly
after not more than 1000 hours of service
check of operation, general condition, lack of
leaks, any replacement required
yearly
after not more than 2500 hours of service
(disposable cylinders)
replacement of cylinder
5 years
after not more than 10000 hours of service (for
inspectable cylinders)
replacement of cylinder
YEARLY CHECK OF COMPONENTS
Do not use detergents or solvents to clean plastic components.
To remove incrustations, wash with a 20% solution of vinegar or acetic acid, and then rinse with water.
filling solenoid valve
disconnect the electrical power supply, remove the valve, and clean
the filter
drainage solenoid valve
disconnect the electrical power supply, remove the bobbin,
disassemble the valve body, remove any impurities and rinse
supply tub, pipes
check that they are free and without impurities
REPLACEMENT OF CYLINDER
To remove the cylinder:
•
Completely drain the water.
•
Cut power to the humidifier using the disconnecting switch of the unit.
•
Remove the steam tube from the cylinder.
•
Detach the electrical connections of the electrodes and remove the
plugs from the high-level electrodes.
•
Unscrew the ring nut to remove the nozzle and the filter (when the
filter is outside the cylinder)
•
Lift the cylinder to extract it
Before putting it back in place:
•
The filter body does not need to be replaced. Wash it with water and
place it on the new cylinder, using the new gasket that comes with it.
•
Check the gasket for the seal between the cylinder and the drain group.
•
Put the cylinder back in place by repeating the operations in reverse order
1 - pipe fastening spring
2 - steam pipe
3 - filling pipe
4 - steam cylinder
5 - O-ring seal
6 - filling valve
7 - valve support
8 - discharge valve
9 - bottom tub
10 -pipe fastening spring
11 -filling pipe
12 - overflow pipe
ELECTRICAL HEATING ELEMENTS
The convector finned heating elements need to be checked regularly to ensure that they are clean and properly fastened to the
support.