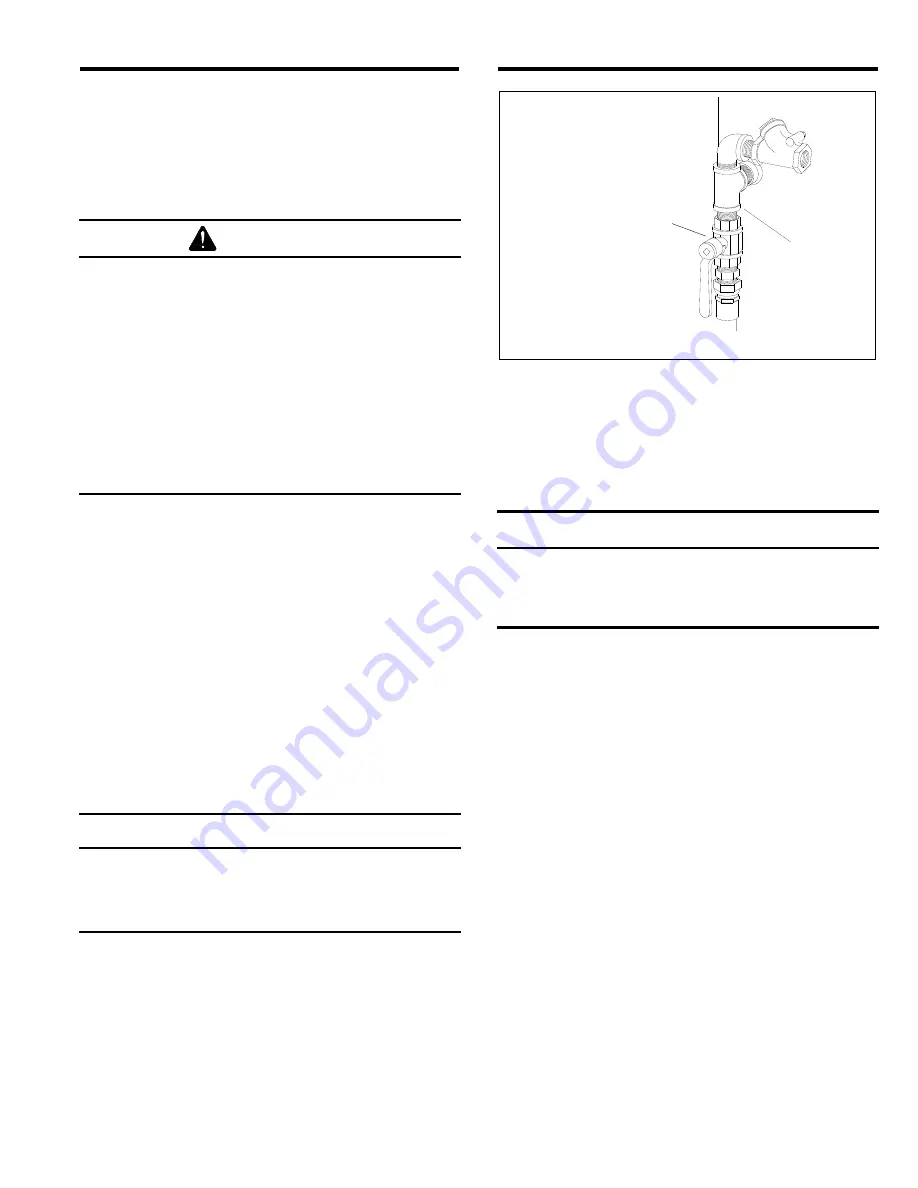
PULSAR
®
III-P/III-PE and VI-P/VI-PE PRESSURE CABINETS
Page 13
© 2019 CLEMCO INDUSTRIES CORP.
www.clemcoindustries.com
Manual No. 21527, Rev. I, 02/19
4.5.6
Insert hands into gloves.
4.5.7
To blast, firmly grasp the nozzle holder or hose
just behind the nozzle holder, point the nozzle toward
the object to be blasted, and apply pressure to the foot
pedal; blasting will begin almost immediately.
WARNING
Shut the cabinet immediately if dust leaks are
detected from the dust collector or cabinet.
Make sure the dust-collector filter(s) are
correctly seated and not worn or damaged.
Prolonged breathing of any dust can result in
serious lung disease or death. Short-term
ingestion of toxic dust such as lead, poses an
immediate danger to health. Toxicity and health
risks vary with type of media and dust
generated by blasting. Identify all material being
removed by blasting and obtain a safety data
sheet (SDS) for the blast media.
4.5.8
Adjust the pilot pressure regulator to the
required blasting pressure, per Section 5.1. The
regulator is located on the top-left side of the cabinet.
NOTE: Pressure registers on the gauge only while
blasting.
NOTE: When holding parts off the grate, use a solid
conductive backrest to support the part. Without this
assist, especially with longer blasting operations, the
operator will tire easily from resisting blast pressure, and
static electricity could build up in the ungrounded part
and cause static shocks. Whenever possible, avoid
holding small parts that require blasting into the glove.
4.5.9
If an object should fall through the grate, stop
blasting immediately and retrieve it.
NOTICE
To prevent rapid frosting of the view window,
install a view-window cover lens, per Section
7.4, and avoid pointing the blast nozzle toward
the view window
4.6
Operation and Function of the Choke Valve
Figure 14
4.6.1
Always fully open the choke valve while blasting;
open is when the handle is vertical and aligned with the
piping, as shown in Figure 14.
Figure 14
4.6.2
Closing the choke valve while blasting lowers
pressure in the pusher line from the pressure in the
vessel. Closing the valve forces media through the
metering valve to clear minor blockage, such as damp
media, or it is used to rapidly empty the machine to
change media.
NOTICE
Do not blast with choke valve closed or partially
closed. Prolonged blasting with the choke valve
partially closed will accelerate wear on the
metering valve.
4.7
Blasting Technique
4.7.1
Blasting technique is similar to spray painting
technique. Smooth, continuous strokes are usually most
effective. The distance from the part affects size of blast
pattern. Under normal conditions, hold the nozzle
approximately 6" from the surface of the part.
4.8
Stop Blasting
4.8.1
To stop blasting, remove pressure from the foot
pedal. The blast machine will depressurize each time the
foot pedal is released.
4.8.2
. The blast machine refills with media stored in
the reclaimer each time the foot pedal is released and
the blast machine depressurizes. Refill takes
approximately 15 seconds when the machine is empty.
4.8.3
Use the blow-off nozzle to blow media off
cleaned parts.
4.8.4
Keep doors closed and exhauster running until
the cabinet is clear of all airborne dust.
Choke Valve
Valve is shown open;
the position of the
handle is aligned with
the piping.