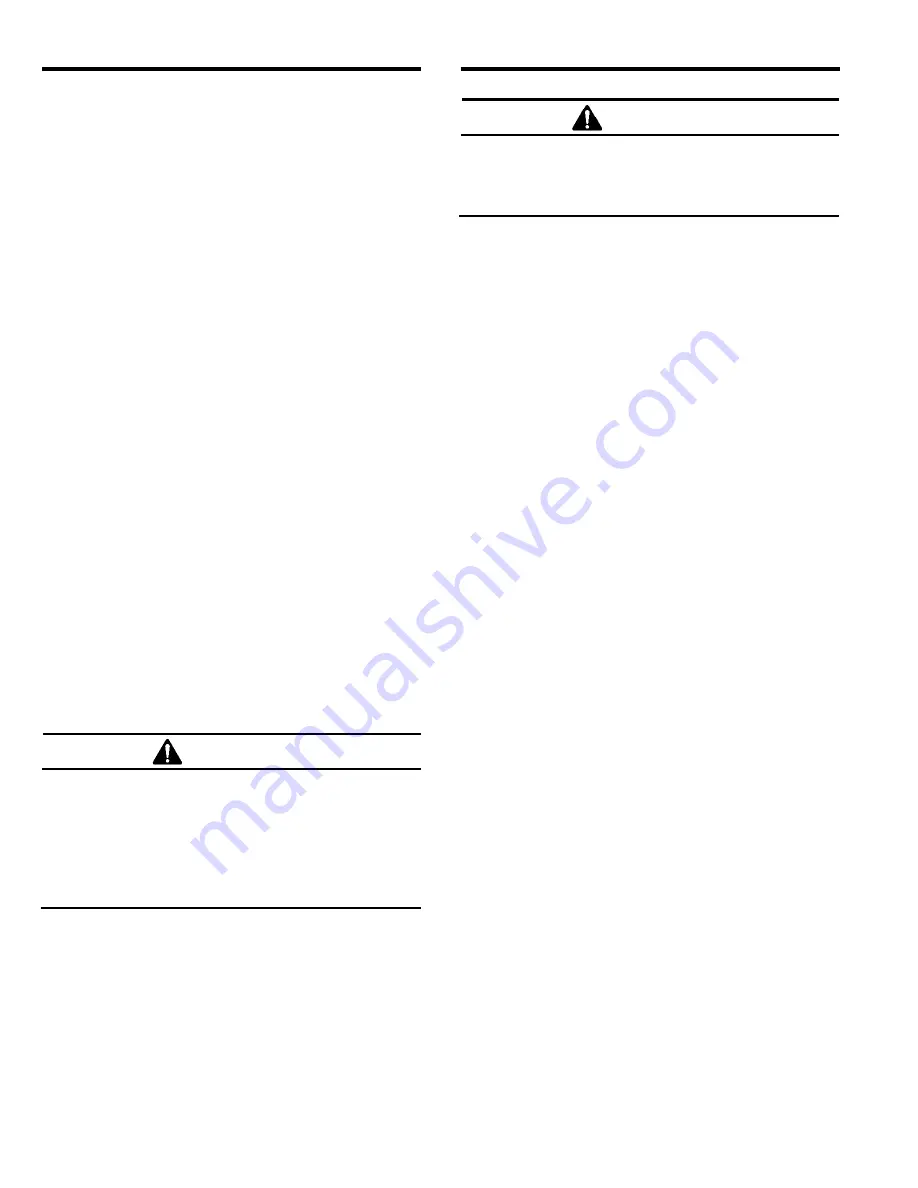
PULSAR
®
III-P/III-PE and VI-P/VI-PE PRESSURE CABINETS
Page 4
© 2019 CLEMCO INDUSTRIES CORP.
www.clemcoindustries.com
Manual No. 21527, Rev. I, 02/19
separation. Dust and fines are first separated from
reusable media and pass into the dust collector. Next,
reusable media is screened for oversize particles and
returned to the reclaimer for reuse. Dust and fines
entering the dust collector are removed from the air
stream as they pass through the filters, discharging
clean air. When the foot pedal is released, the blast
machine depressurizes and blasting stops. Media
stored in the reclaimer automatically refill the blast
machine when blast machine pressure equalizes and
the pop-up valve drops.
1.5.2
The dust-collector filter cartridge is cleaned by a
pulse of high velocity compressed air expanding against
the inner surface of the cartridge. The pulse occurs each
time the foot pedal is pressed or released. The expanding
air momentarily reverses airflow through the cartridge to
release dust accumulated on the outer surface. The dust
particles fall away from the cartridges and into the hopper
for removal. An optional automatic pulse kit can be added
to pulse the cartridge at timed intervals during blasting.
(See
Section 9.1: Optional Accessories.
).
1.6
Blast Machine and Controls
1.6.1
Clemco certifies its blast machines (pressure
vessels) to conform to the ASME (American Society of
Mechanical Engineers) Boiler and Pressure Vessel
Code, Section VIII, Division 1. It is the owner’s
responsibility to maintain the integrity of the vessel in
accordance with state regulations. Regulations may
include regular inspection and hydrostatic testing as
described in National Board inspection code and
jurisdictional regulations and/or laws.
WARNING
Welding, grinding, or drilling on the blast
machine can weaken the vessel. Compressed-
air pressure can cause a weakened blast
machine to rupture, resulting in death or
serious injury. Welding, grinding, or drilling on
the vessel without a National Board R Stamp
voids the Clemco ASME certification.
1.6.2
All welding repairs to the vessel must be
performed by certified welders at shops holding a
National Board R stamp. Welding performed by any
welder not properly qualified per the ASME code voids
the Clemco ASME certification.
1.6.3
Do not exceed the maximum working pressure
rating (PSI) of the blast machine. The maximum
pressure rating is stamped into the ASME nameplate,
which is welded to the side of the vessel.
WARNING
Excessive compressed-air pressure can cause
a blast machine to rupture. To prevent serious
injury or death, do not exceed the rated
pressure of the blast machine.
1.6.4
OSHA does not require pressure-relief valves
on blast machines when air compressors supplying air
to the blast machines are built to American Society of
Mechanical Engineers Boiler and Pressure Vessel
Code, Section VIII, Division 1 and comply with OSHA
regulation 29 CFR 1910.169, which refers to the ASME
code when describing the necessity of pressure-relief
valves on compressed air equipment.
DO NOT
operate
blast machines with air compressors that are not
equipped with properly functioning pressure-relief valves
with maximum pressure less than or equal to the
maximum-allowable working pressure (MAWP) stamped
on the vessel nameplate.
1.6.5
When the cabinet is set up, the blast machine is
ready to blast by actuating the foot pedal. Pressing the
foot pedal opens the normally closed main inlet
regulator and closes the normally open outlet valve. The
incoming air pressurizes the blast machine, and blasting
begins. When pressure on the foot pedal is released,
the blast machine depressurizes and blasting stops.
1.7
Nozzle Options
1.7.1
Unless otherwise specified at the time of
purchase, the cabinet is provided with a 3/16" orifice
tungsten carbide nozzle. Optional 1/8" and 1/4" orifice
nozzles are also available.
1.7.2
Nozzles with an orifice larger than those
recommended could cause air leakage from the cabinet
and impair recovery from the cabinet hopper.
1.7.3
Use boron carbide nozzles when blasting with
aggressive media noted in Section 1.11.3. Nozzles lined
with boron carbide extend nozzle wear life. Refer to
Section 9.1
:
Optional Accessories
.
1.8
Reclaimer Options
1.8.1
Replaceable rubber reclaimer liners:
Rubber
liners are available for Pulsar VI, 600 cfm reclaimers
that have a removable top and that are designed to
accept liners. The liners prolong service life of the
reclaimer, and should be installed when using silicon
carbide, aluminum oxide, or other aggressive media, as
noted in Section 1.11.3. Rubber reclaimer liners are
shown in
Section 9.1
:
Optional Accessories, Figure 40.