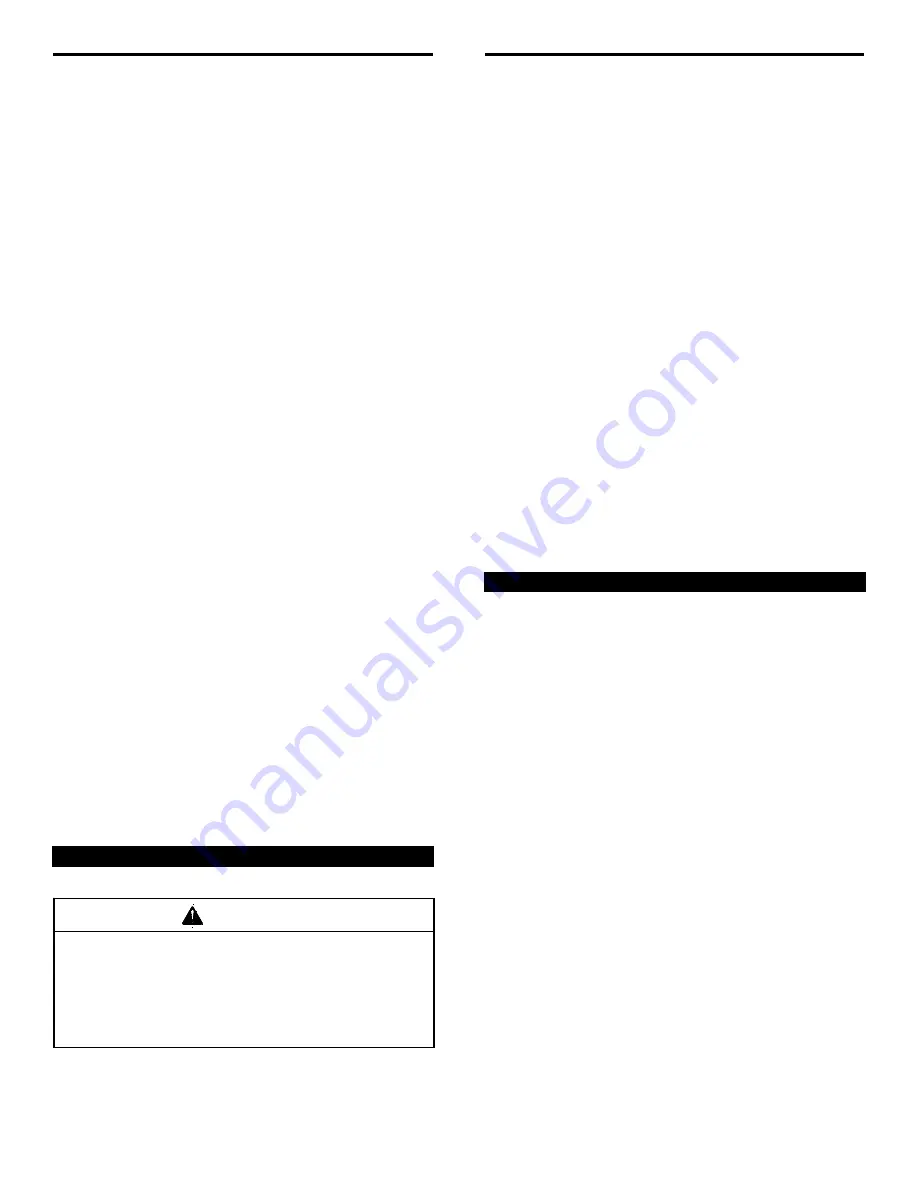
PREFACE
instrument should be used to determine when surrounding
atmosphere is clear of dust and safe to breathe.
•
NIOSH-approved, supplied-air respirators are to be worn
ONLY in atmospheres:
• NOT IMMEDIATELY dangerous to life or health and,
• from which a user can escape WITHOUT using the
respirator.
•
Clemco supplied-air respirators
DO NOT REMOVE OR
PROTECT AGAINST CARBON MONOXIDE (CO) OR ANY
OTHER TOXIC GAS.
Carbon monoxide and toxic gas removal
and/or monitoring device must be used in conjunction with
respirator to insure safe breathing air.
•
Air supplied to respirator MUST BE AT LEAST GRADE D
QUALITY as described in Compressed Gas Association
Commodity Specification G-7.1, and as specified by OSHA
Regulation 1910.139 (d).
•
ALWAYS locate compressors to prevent contaminated air
(such as CO from engine exhaust) from entering the air intake
system. A suitable in-line air purifying sorbent bed and filter or
CO Monitor should be installed to assure breathing air quality.
•
ALWAYS use a NIOSH-approved breathing air hose to
connect an appropriate air filter to the respirator. Use of a non-
approved air hose can subject the operator to illness caused
by the release of chemical agents used in the manufacture of
non-approved breathing air hose.
•
ALWAYS check to make sure air filter and respirator
system hoses are NOT CONNECTED to in-plant lines that
contain nitrogen, acetylene or any other non-breathable gas.
NEVER use oxygen with air line respirators. NEVER modify air
line connections to accommodate air filter/respirator breathing
hose WITHOUT FIRST testing content of the air line.
FAILURE
TO TEST THE AIR LINE MAY RESULT IN DEATH TO THE
RESPIRATOR USER.
•
Respirator lenses are designed to protect against
rebounding abrasive. They do not protect against flying
objects, glare, liquids, radiation or high speed heavy materials.
Substitute lenses from sources other than the original
respirator manufacturer will void NIOSH-approval of this
respirator.
BLAST MACHINES AND REMOTE CONTROLS
•
ALWAYS equip abrasive blast machines with
remote controls.
•
Abrasive blast machine operators must wear NIOSH-
approved supplied-air respirators (ref: OSHA
regulations 1910.94, 1910.132, 1910.139 and
1910.244).
•
NEVER modify OR substitute remote control parts. Parts
from different manufacturers are NOT compatible with Clemco
equipment. If controls are altered, involuntary activation, which
may cause serious injury, can occur.
•
Inspect the air control orifice DAILY for cleanliness.
NEVER use welding hose in place of twinline control hose. The
internal diameter and rubber composition are UNSAFE for
remote control use.
•
UNLESS OTHERWISE SPECIFIED, maximum working
pressure of blast machines and related components MUST
NOT exceed National Board approved 125 psig (8.5 BAR).
•
NEVER weld on blast machine. Welding may affect
dimensional integrity of steel wall and WILL VOID National
Board approval.
•
Point nozzle ONLY at structure being blasted. High
velocity abrasive particles WILL inflict serious injury. Keep
unprotected workers OUT of blast area.
•
NEVER attempt to manually move blast machine when it
contains abrasive. EMPTY machines, up to 6 cu. ft.(270kg)
capacity, are designed to be moved:
• on flat, smooth surfaces by AT LEAST two people;
• with the Clemco "Mule"; or
• with other specially designed machine moving devices.
•
Larger empty blast machines or ANY blast machine
containing abrasive MUST be transported by mechanical lifting
equipment.
AIR HOSE, BLAST HOSE, COUPLINGS, AND NOZZLE HOLDERS
•
Air hose, air hose fittings and connectors at compressors
and blast machines MUST be FOUR times the size of the
nozzle orifice. Air hose lengths MUST be kept as short as
possible AND in a straight line. Inspect DAILY and repair
leakage IMMEDIATELY.
•
Blast hose inside diameter MUST be THREE to FOUR
times the size of the nozzle orifice. AVOID sharp bends that
wear out hose rapidly. Use SHORTEST hose lengths possible
to reduce pressure loss. Check blast hose DAILY for soft
spots. Repair or replace IMMEDIATELY.
•
ALWAYS cut loose hose ends square when installing hose
couplings and nozzle holders to allow uniform fit of hose to
coupling shoulder. NEVER install couplings or nozzle holders
that DO NOT provide a TIGHT fit on hose. ALWAYS use
manufacturers recommended coupling screws.
•
Replace coupling gaskets FREQUENTLY to prevent
leakage. Abrasive leakage can result in dangerous coupling
failure. ALL gaskets MUST be checked SEVERAL times during
a working day for wear, distortion and softness.
•
Install safety pins at EVERY coupling connection to
prevent accidental disengagement during hose movement.
•
ALWAYS attach safety cables at ALL air hose AND blast
hose coupling connections. Cables relieve tension on hose and
control whipping action in the event of a coupling blow-out.
WARNING
II