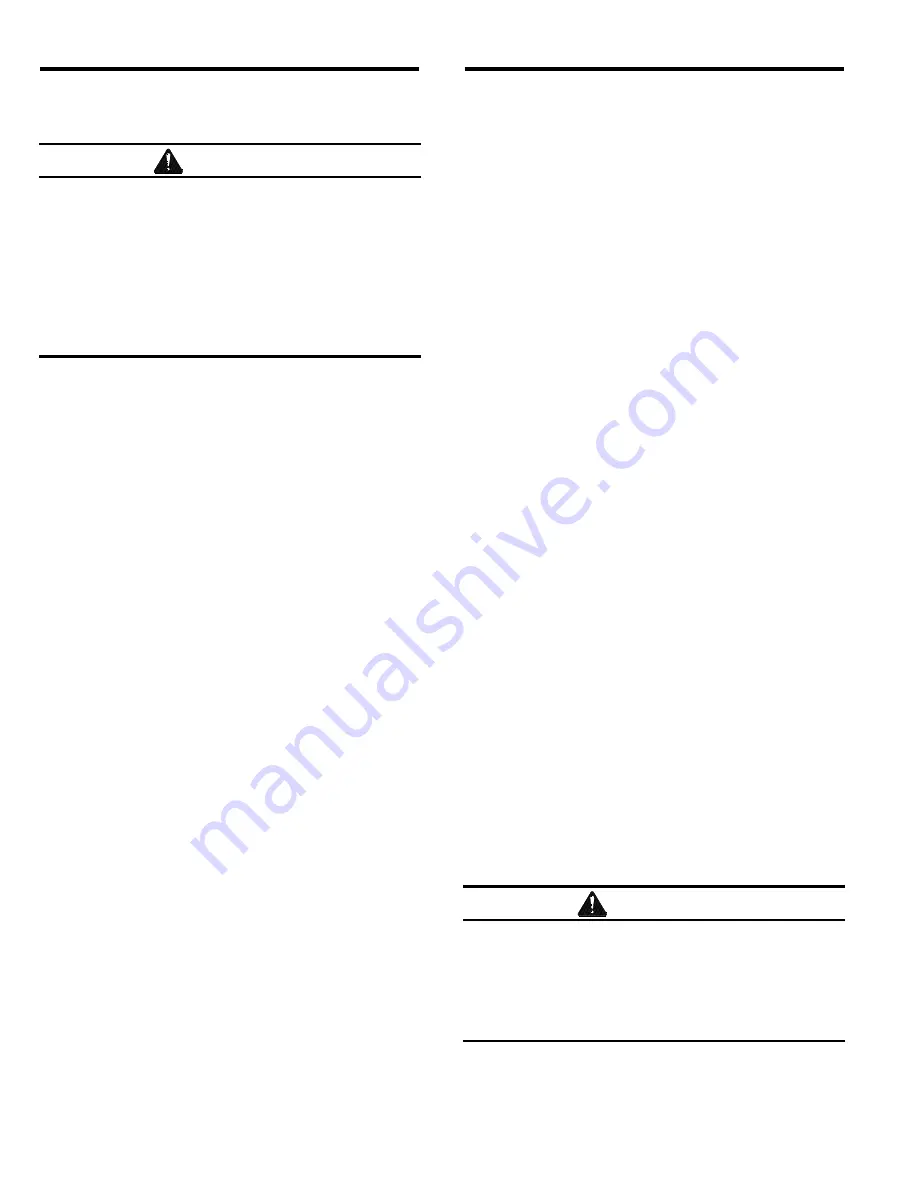
TLR-100/300 SERIES PNEUMATIC REMOTE CONTROLS
Page 8
© 2009 CLEMCO INDUSTRIES CORP.
•
www.clemcoindustries.com
•
Manual No. 22428
5.0 SERVICE
MAINTENANCE
WARNING
Failure to observe the following before
performing any maintenance could cause
serious injury or death from the sudden release
of compressed air.
•
Depressurize the blast machine.
•
Lockout and tagout the compressed air
supply.
•
Bleed the air supply line to the blast
machine.
5.1
Inlet Valve, Ref. Figure 6 (1-1/2
″
valve) or
Figure 7 (1
″
valve).
5.1.1
All service on the inlet valve must be done with
the air off and the air supply locked-out and tagged-out.
5.1.2 Bottom
Section
5.1.2.1
Use a wrench to loosen the bottom cap until it
can be removed by hand.
5.1.2.2
Take care when removing the cap as the
spring(s) (two are used in the 1-1/2
″
inlet valve) and plug
assembly will drop from the opening. Do not allow them
to fall to the ground as that could damage the castings.
5.1.2.3
Clean all parts and inspect for wear as follows:
•
The small spring (only one used in 1
″
valve) is
approximately 1-11/16
″
long. If it is rusted or
compressed, replace it.
•
The large spring (not used in 1
″
valve is
approximately 2-1/16
″
long. If it is rusted or
compressed, replace it.
•
Inspect the valve plug washer, valve plug, and plug
retainer for damage. Replace all damaged parts.
When reassembling the valve plug assembly,
tighten the retainer enough to compress the washer,
but not so tight to cause it to bulge.
•
Look into the lower opening in the valve body. If the
machined seat is worn, replace the body.
•
Inspect the bottom cap seal, and replace if
damaged.
5.1.2.4
If the top section of the valve requires service,
go to Section 5.1.3, otherwise use the illustration in
Figure 6 or 7, and reassemble the valve in reverse
order.
5.1.3 Top
Section
5.1.3.1
Remove the control hose and fittings from the
cylinder cap to ensure they are not damaged by a
wrench.
5.1.3.2
Use a large wrench to remove the cylinder cap.
5.1.3.3
If the bottom cap has not been removed,
remove it, and all other parts per Section 5.1.2.
5.1.3.4
Use a wooden hammer handle or similar object,
inserted into the bottom of the valve body, pushed
through the seat area, to drive the piston stem up. Doing
so will push the piston out the top of the valve body.
5.1.3.5
Inspect all items for wear and damage.
•
The piston cup should fit snug against the cylinder
wall. If it does not, replace the piston assembly.
•
The piston stem should be free of deep abrasion
and move freely in the stem bore. If it is badly
abraded, drags in the bore, or loose in the bore,
replace the piston assembly.
•
If the piston stem O-ring is flattened, replace the O-
ring.
•
Check the cylinder cap O-ring. Replace it if it is cut
or if it does not fit snugly on the cap recess.
5.1.3.6
Lubricate the cylinder wall and piston cup, with
lightweight machine oil or tool oil.
5.1.3.7
Install the piston into the cylinder. As the piston
cup contacts the cylinder it may be difficult to press into
place. Do not pound the piston, as it could damage the
cup. Rotating the piston while applying thumb pressure
eases assembly.
5.1.3.8
Use the illustration in Figure 6 or 7 and
reassemble the valve in reverse order.
5.1.4
Remove the lower twinline hose connection, and
remove the orifice fitting for inspection. Clean the 1/16
″
orifice and reassemble the connection.
WARNING
The orifice fitting must not be removed,
modified, or substituted with another fitting.
Altering the orifice fitting may cause involuntary
activation of the blast machine or some other
malfunction which could result in serious injury
or death.