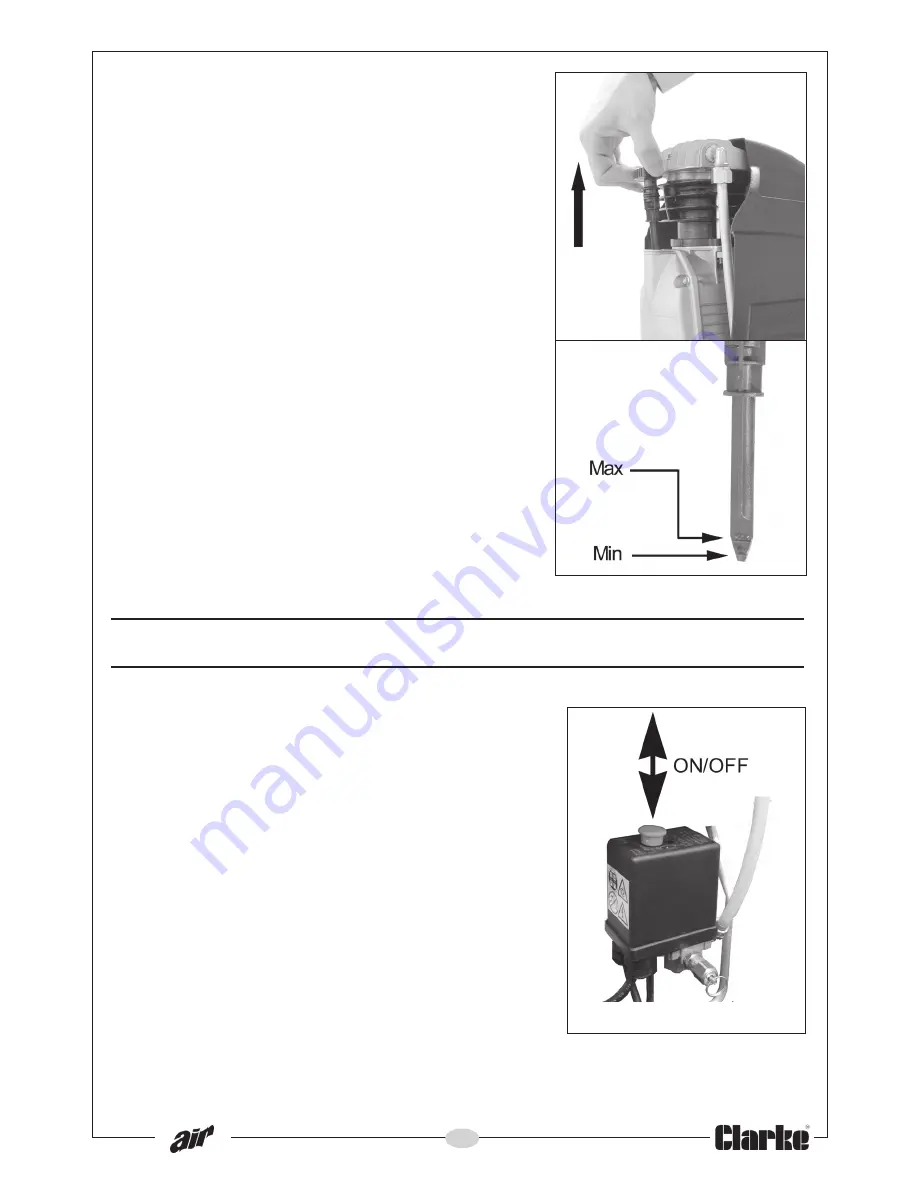
13
CHECKING THE OIL
1. Remove dipstick and check the level of oil is
between the MAX and MIN marks as shown
in Fig 3. If not, top up to the correct level
with Clarke SAE40 compressor oil.
2. After the first 5 working hours, replace the oil
as described under MAINTENANCE on page
16.
OPERATING INSTRUCTIONS
STARTING THE COMPRESSOR
1. Pull the ON/OFF switch UP to start the
compressor as shown in Fig 4.
• The motor should start immediately, and
run, while the tank (reservoir) is being
pressurised.
2. When starting the compressor for the first
time, and before connecting it to the airline
equipment, leave it running for about 10
minutes to permit a good distribution of
lubricating oil.
• Observe that the compressor stops
automatically when the maximum
pressure of 8 bar is reached. The pressure
is indicated on the tank pressure gauge
shown in Fig 6.
Fig 3
Fig 4
Summary of Contents for PIONEER 220
Page 10: ...10 OVERVIEW...
Page 20: ...20 PARTS DIAGRAM AIR RECEIVER CONTROLS...
Page 21: ...21 PARTS DIAGRAM COMPRESSOR...
Page 23: ...23 DECLARATION OF CONFORMITY...
Page 24: ......