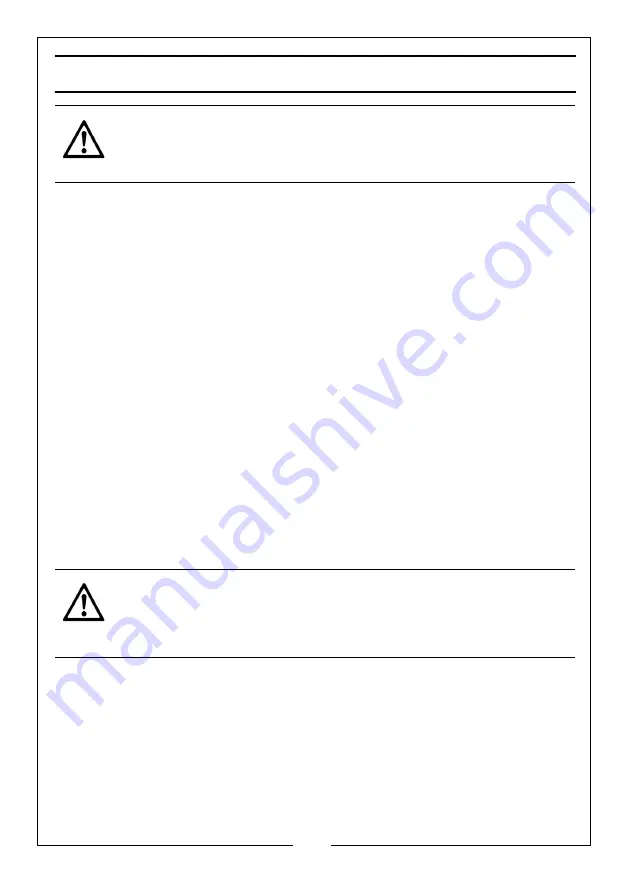
3
Parts & Service: 020 8988 7400 / E-mail: [email protected] or [email protected]
SAFETY AND GENERAL WARNINGS
1. Make sure that the unit is earthed and that the supply line has an
adequate earth connection.
2. Make sure that any workbench used has a satisfactory earth connection.
3. Avoid contact between the metal being cut and bare skin or damp
clothes.
4.
DO NOT
lean on the workpiece being cut or hold it in your hands.
5.
DO NOT
use in a damp environment or on wet surfaces.
6.
DO NOT
use the unit if the torch or cables appear damaged.
7.
ALWAYS
turn the unit off before replacing the electrode, the nozzle or the
spreader tip of the torch.
8.
DO NOT
allow debris to collect as this could obstruct air flow to the
machine.
9.
ALWAYS
switch the unit off and remove the power cable from the mains
socket before carrying out any maintenance on the uni
t.
10. All the panels of the unit should be correctly closed after carrying out
maintenance.
HARMFUL FUMES AND GASES
Harmful fumes and metallic powders are produced during the cutting
operation. Metals which are painted or coated or which contain mercury,
cadmium, zinc, lead and graphite may produce harmful concentrations of
toxic fumes during cutting. To protect the operator or other persons from
exposure to possible toxic fumes, fume respirators should be worn and work
areas should be adequately ventilated.
When working in enclosed environments, suction units should be fitted below
the cutting areas.
CAUTION: IF DURING THE CUTTING OPERATION A SLIGHT ELECTRIC
SHOCK IS FELT, STOP WORK IMMEDIATELY AND DO NOT USE THE UNIT
UNTIL THE FAULT HAS BEEN DISCOVERED AND RESOLVED.
CAUTION: WHEN HALOGENATED SOLVENTS OR DEGREASING AGENTS
ARE PRESENT, THE MATERIAL TO BE CUT SHOULD BE CLEANED PROPERLY
TO PREVENT THE FORMATION OF TOXIC GASES. SOME CHLORINATED
SOLVENTS MAY DECOMPOSE IN THE PRESENCE OF THE RADIATION GIVEN
OUT BY THE ARC AND MAY GENERATE PHOSGENE GAS.7
Summary of Contents for 6015700
Page 24: ......