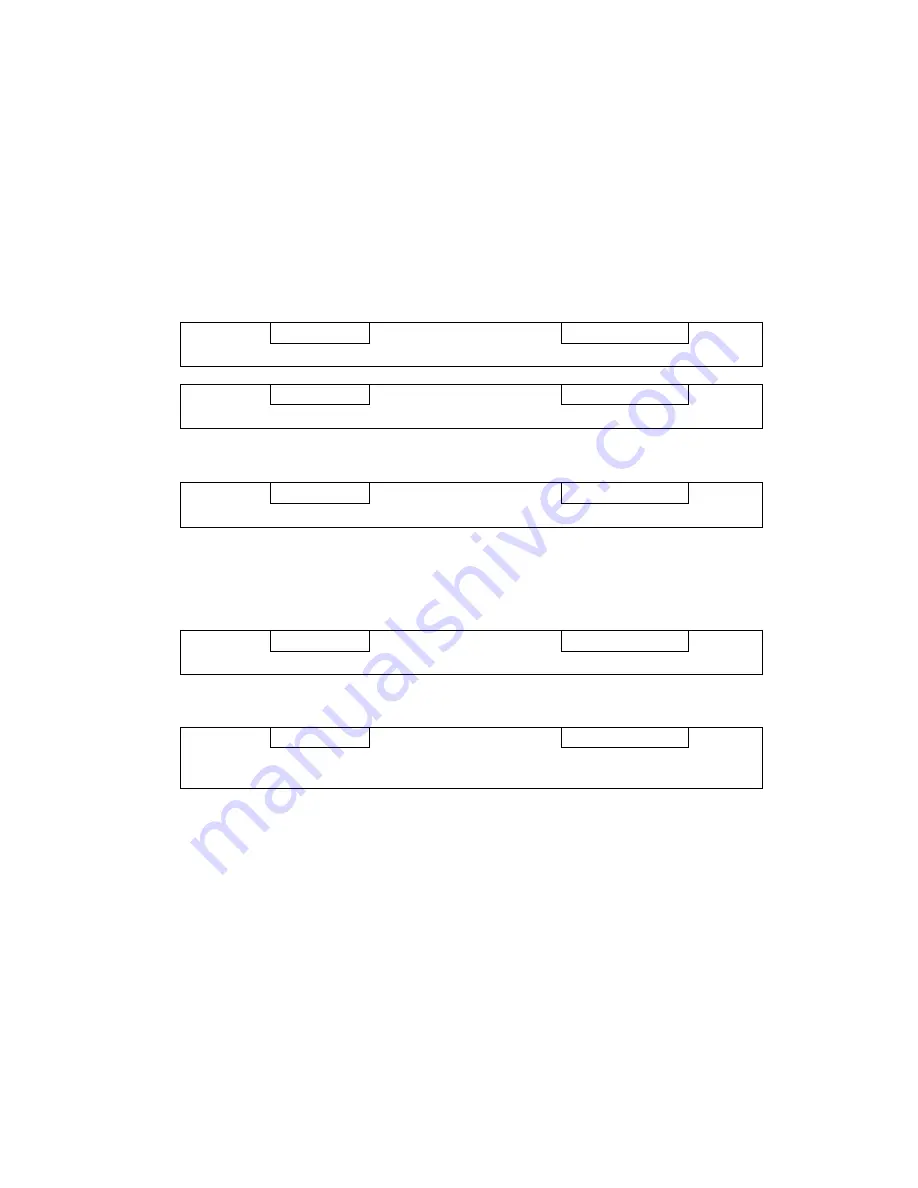
5
15. Remove O-rings (40 and 80) from bearing housing (9).
NOTE:
If neither ball bearing (31) nor seal (51) are to be replaced or inspected, disassembly is complete. If either of
these components are to be replaced or inspected for any reason, proceed as below.
16. Place inboard face of bearing housing (9) on the clean, smooth surface of an arbor press with coupling end
facing up.
17. Remove socket head capscrews (75) and bearing retainer (70).
18. Remove ball bearing snap ring (33).
19. Press shaft (6) out of bearing housing (9) by pushing squarely on coupling end of shaft (6). Rotating member of
seal (51) and its seal spacer (74) will remain on shaft while ball bearing (31) and stationary member of seal (51) will
remain in bearing housing (9).
CAUTION
ATTENTION
Be sure to hold onto shaft (1) when pressing it out of bearing housing (9).
CAUTION
ATTENTION
Take extreme card during this step to avoid damaging seal faces.
20. Remove ball bearing (31) from bearing housing (9) by lightly tapping it out with brass rod from inboard side.
CAUTION
ATTENTION
Be careful not to damage stationary face of seal (51) with brass rod.
NOTE:
If mechanical seal (51) is not to be replaced, disassembly is complete. Take care to prevent damage to
seal components. If mechanical seal (51) is to be replaced, proceed as below.
21. Press stationary part of mechanical seal (51) out of bearing housing (9).
CAUTION
ATTENTION
Be careful not to damage stationary face of seal (51) when pressing it out.
22. Loosen set screw and remove rotating part of mechanical seal (51) from shaft (6)
.
CAUTION
ATTENTION
Take great care not to touch or damage the rotating face of the seal (51). This seal face
is very sensitive to chipping and/or scratching.
23. Remove seal spacer (74) from shaft (6) if applicable.
H. INSPECTION OF PARTS
1. BALL BEARING – Ball bearings should be free turning and quiet. Their grease should have a soft consistency
and not look or smell burned.
2. GEAR FACES – Some light scratching is acceptable, but if there is any scoring, the part should be replaced.
These faces cannot be ground to remove a heavy score mark because their width is critical to performance of
pump. Grinding more than several ten thousandths of an inch will cause low capacity. If the face is not flat, pump
seizure could occur.
NOTE:
Rework other than light stoning or cleaning of gears or gear housings is not recommended. New gear
housings are provided with sleeve bearing factory installed.