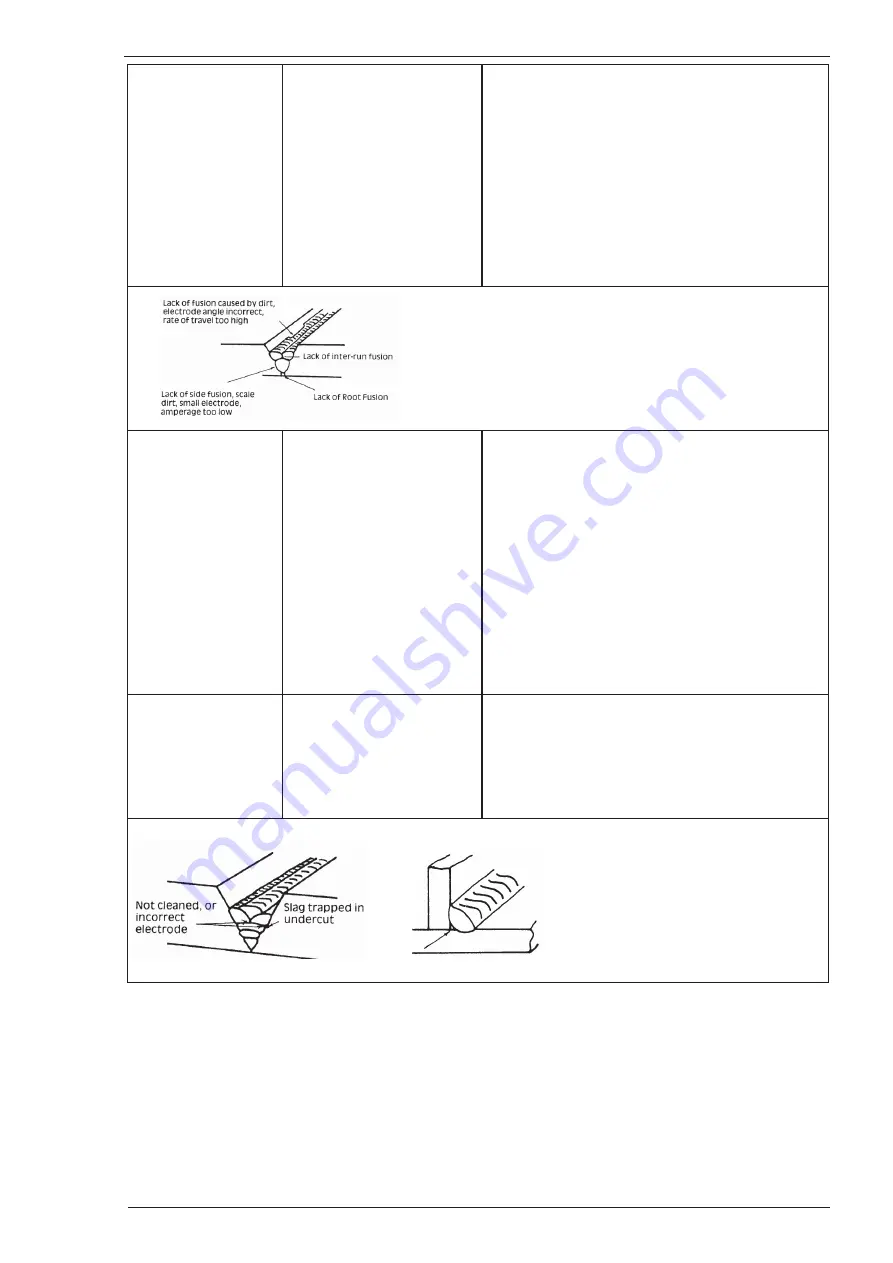
TRANSTIG 220 AC/DC AND 300AC/DC POWER SOURCE
Manual 0-5293
4-13
BASIC WELDING GUIDE
5 Portions of the
weld run do not
fuse to the surface
of the metal or
edge of the joint.
A Small electrodes used on
heavy cold plate.
A Use larger electrodes and preheat the plate.
B Welding current is too low. B Increase welding current.
C Wrong electrode angle.
C Adjust angle so the welding arc is directed more
into the base metal.
D Travel speed of electrode
is too high.
D Reduce travel speed of electrode.
E Scale or dirt on joint
surface.
E Clean surface before welding.
Art: A-04972
Figure 2: Example of Lack of Fusion
6 Gas pockets or
voids in weld
metal (porosity)
A High levels of sulphur in
steel.
A Use an electrode that is designed for high sul-
phur steels.
B Electrodes are damp.
B Dry electrodes before use.
C Welding current is too
high.
C Reduce welding current.
D Surface impurities such as
oil, grease, paint, etc.
D Clean joint before welding.
E Welding in a windy envi-
ronment.
E Shield the weld area from the wind.
F Electrode damaged ie flux
coating incomplete.
F Discard damaged electrodes and only use elec-
trodes with a complete flux coating.
7 Crack occurring in
weld metal soon
after solidification
commences
A Rigidity of joint.
A Redesign to relieve weld joint of severe stresses
or use crack resistance electrodes.
B Insufficient throat thick-
ness.
B Travel slightly slower to allow greater build up in
throat.
C Weld current is too high. C Decrease welding current.
Art: A-04973
Figure 3: Example of Slag Inclusion
Table 4-2: Welding Problems MMAW (Stick)
Summary of Contents for A-12030
Page 6: ......