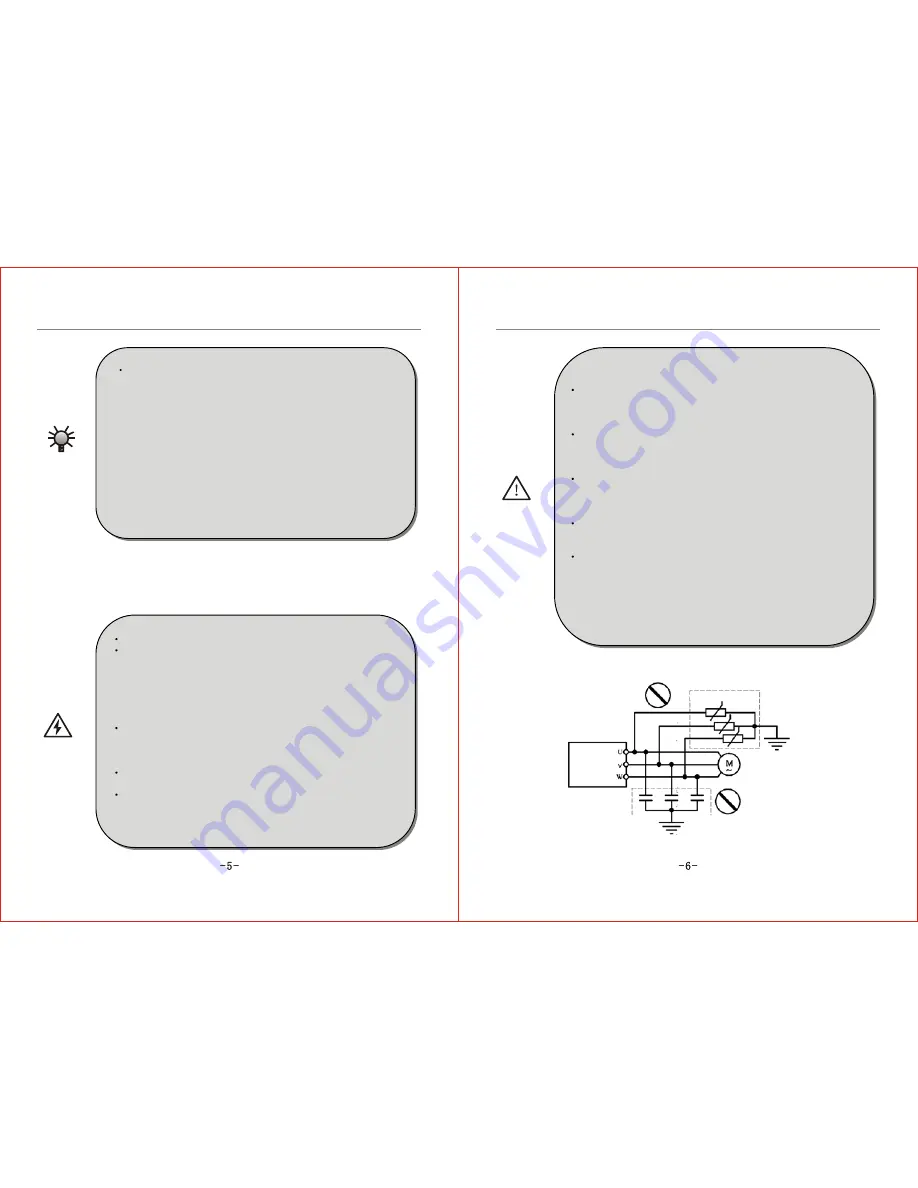
Chapter 1 Safety Instructions
Chapter 1 Safety Instructions
CAUTION
It is not advisable to install an electromagnetic contactor in the side of
output power supply, because the operation of open and close to the
contactor when the motor is running may cause damage to the inverter
arising from over-voltage produced during this process. But it is still
necessary to install a contactor if one of the following three points occurs:
1.The system of frequency converting governor used to control energy-
saving usually works at a rated rotation speed. To run the governor
economically, there is a must to remove the inverter.
2.The inverter participates in some import procedure and cannot stop
operating for a long period of time. To realize free shift in various control
systems and improve the reliability of these systems, there is a must to
install a contactor.
3.When an inverter controls several motors, there is a must to install a
contactor.
Caution: DO NOT operate the contactor if there is output of the inverter.
1.5 Cautions for Operation
HAZARD
Do not operate electrical equipment with wet hands.
An inverter stored for a year or longer should be given
powerup test before use so that the main circuit filter capacitor
could be recovered.When the inverter is in the state of powerup,
it is necessary to raise the voltage gradually to the rated value
with a voltage regulator. Generally, the charging time should be
controlled within 1~2 hours. Otherwise, there is the danger of
electric shock or exposure.
Do not touch the inner side of the inverter while the power is
ON, nor put any foreign matter, i.e., rod or other matter inside the
inverter. Otherwise, it may result in serious damage to the
equipment or death to personnel.
Do not open the front cover while the inverter is powered ON.
Otherwise, there is the danger of electric shock.
Be careful to select the Restart Mode. Otherwise, there is
the danger of personnel death.
WARNING
If the inverter runs at a frequency higher than 50Hz, DO confirm
it is within the speed range acceptable by your motor bearing and
mechanical device. Otherwise, there is the danger of damage to the
motor.
It is not advisory to run the reduction box, gear and other
mechanism that need lubricating at low speed for a long period.
Otherwise, it may reduce the service life of these equipment or
even damage the equipment.
A general motor should be derated before use due to less
effective of heat dissipation when it runs at a low frequency. If it is
a constant torque load, then a forced method or a special variable
frequency motor should be used to release heat.
DO cut off the power supply of an inverter set aside for a long
time to avoid foreign matter or other things enter in it which may
cause damage to the inverter or even lead to fire.
The output voltage of inverter is PWM impulse wave. DO NOT
install a capacitor or surge current sink (i.e., a varistor) in the
inverter output port. Otherwise, there is the danger of fault tripping
of the inverter or damage to its power elements. DO remove such
kind of things if already installed. See the Figure 1-3 below.
Forbidden
Forbidden
Inverter
Power factor
compensation
capacitor
Surge current sink
Figure 1-3
Summary of Contents for ZVF9V-G/P
Page 8: ...M Integration Module S Schism Module...
Page 12: ......
Page 16: ......
Page 21: ...Inverter...
Page 33: ......
Page 87: ......